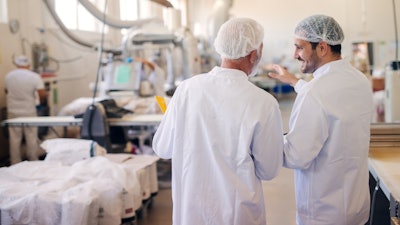
Bacteria accumulation is a serious issue in the food manufacturing industry - it can ruin product and put consumer health at risk.
While many know that Polytetrafluoroethylene (PTFE) is an excellent choice for use in diaphragms and gaskets, most do not realize that there exist varying grades of PTFE. Some lower cost PTFE offerings may contain an excessive volume of pores within their structure which can harbor organic contaminants such as bacteria.
To address this problem, a calendared manufacturing process is used. Calendared PTFE is a premium grade PTFE designed for use in aseptic applications requiring ultra-high purity standards. It is ideal for use in food, pharmaceuticals and a variety of clean markets.
Figure A: Molded Diaphragm Made From Calendared PTFEGarlock
Distinguished by an extremely low void content, calendared PTFE resists permeation and the accumulation of foreign matter, reducing the risk of harboring unwanted bacteria or residual media.
To achieve this, the unique manufacturing process orients the chains of PTFE in a lattice-like structure that reduces voids in the material and provides it with biaxial strength. This unique structure also delivers a very high flex life. When tested in an MIT Folding Endurance Tester, the flex life of calendared PTFE is four-times greater than conventional PTFE materials.
Unlike the skived process that is commonly used for PTFE manufacturing, the calendaring process produces uniform sheets of material with consistent physical properties. This gives calendared PTFE a renowned reputation for predictable performance and quality. The opposite is true for skived PTFE where variable properties lead to varying performance and reliability.
Clean Manufacturing
During clean manufacturing processes where elimination of contaminates is of utmost importance, a Steam-in-Place (SIP) or Clean-in-Place (CIP) process flushes the system without disassembly. During a SIP or CIP process, any harmful bacteria is removed or made inert.
Figure B: The diagram above shows the progression of bacterial growth on the surface of production equipment, most often in low flow or uneven surface areas.Garlock
While undergoing the SIP process, most PTFE materials, owing to their permeability, allow steam to penetrate or become trapped in voids, causing defects such as blisters in the material. This in turn can lead to the increased harboring of bacteria and eventual contamination of a clean manufacturing process (Figure B). Calendared PTFE has a much lower porosity than skived PTFE materials and minimizes these unwanted effects.
To achieve a similar clean system state, Cleaning-in-Place is performed by exposing a system to a mixture of chemicals and heat for a predetermined amount of time, during which a variety of alkaline solutions, acids and additives are used as a disinfecting media. Cleaning temperature, concentration of cleaning media and media exposure time are variables in the CIP process. Due to its unique microscopic structure resulting in extremely low porosity, Calendared PTFE has the ability to be exposed to higher concentrations of cleaning chemicals for longer periods of time.
Calendared PTFE has achieved success in clean markets, owing to its ability to perform in reoccurring CIP/SIP processes without the risk of jeopardizing the structural integrity of the PTFE. Its performance and integrity have earned it multiple certifications, including: USP Class VI (primarily used in the medical and pharmaceutical industries), 3A (dairy, food and pharmaceuticals) and is compliant to both EHEDG and FDA standards. EHEDG is a European-based non-governmental organization devoted to the advancement of hygienic design and food engineering which shares similarities with FDA regulations. Below (in Figure C) is a representation of a standardized test protocol that is focused on determining the effectiveness of a CIP process on system components, in this case gaskets.
Figure C: The diagram above shows the layout of the test per EHEDG Guideline (Doc. 2)Garlock
Shown (in Figure D) is a comparison of calendared PTFE in gasket form to an EPDM gasket after the gaskets were used in a standardized EHEDG testing guideline (Doc. 2) utilizing spore suspension and fermented milk. The combination of low surface energy (<18.5mN/m @ 68°F) and low porosity dramatically reduces the risk that microorganisms grow and contamination occurs on calendared PTFE. This positions calendared PTFE as a superior sealing option over compression molded (skived) PTFE, rubber materials such as EPDM and 316 stainless steel.
Figure D: The images above show the comparison of microbial growth under a fluorescence microscope (living organisms appear green, dead particles appear red).Garlock
The image below (in Figure E) shows a microscopic view of calendared PTFE compared to a competitive PTFE material, which highlights the integrity and impermeability produced by the calendaring process. While voids in the skived PTFE material are vulnerable areas for chemical attack and permeation, the unique calendaring process produces a uniform structure that is unvarying throughout the sheet. This consistency delivers a predictable and reliable performance in applications requiring a low porosity, pure PTFE material.
Figure E: Competitor A PTFE (left), Calendared PTFE (right)Garlock
Resisting Deformation
Unlike other PTFE materials, calendared PTFE resists creep (deformation) or cold flow, due to its tighter microscopic structure and is especially useful when used as a seal or in high-pressure applications.
Additionally, calendared PTFE performs very well in applications where cold temperatures would otherwise compromise reliability, such as cryogenics. It has also proven particularly effective in cold aseptic filling operations, which are used in the production of sports drinks, fruit drinks and a variety of other liquids.
Incorporating calendared PTFE into production systems reduces the chance of batch contamination while simultaneously providing longer run times. The economic advantages of using a next level PTFE are delivered to the end user through improved system uptime and reliability. The unique molecular structure provided by the proprietary manufacturing process makes calendared PTFE an ideal material for use in ultra-high purity markets.
Alex Eanniello is the primary Applications Engineer for the diaphragm product line at Garlock Sealing Technologies, a subsidiary of EnPro Industries, Inc. He has experience in the operation, function and manufacturing of diaphragm products.
Mike Brooks is the Senior Product Line Specialist for diaphragms and fabricated gaskets. He has eight years of experience in the design, operation and applications of diaphragms in various industries.
Alex & Mike can be reached at [email protected].