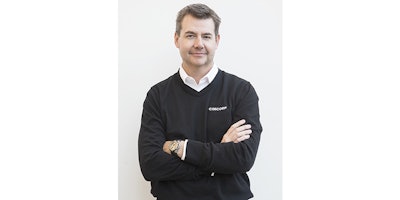
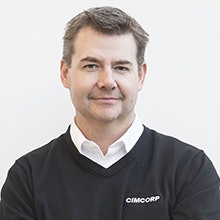
When it comes to food, today’s consumers demand variety, healthy choices and—perhaps most importantly—freshness. To remain competitive, food manufacturers and distributors now have to maneuver through a proliferating number of SKUs and seasonal peaks in business, all while ensuring their products comply with stringent regulations on food quality and safety. One of the most critical points in this complex supply chain is the distribution center, where efficient material flow is necessary to deliver fresh, top-quality products to market.
To keep up with the modern food supply chain, we are seeing more organizations turn toward automation. Through automated solutions, distribution centers can quickly and effectively move products from receiving or storage, all the way through to dispatch. Rapid fulfillment means longer shelf lives, which presents a huge benefit to perishable foods, such as dairy, baked goods, seafood, meats, fruits and vegetables. In addition to speed, robotic automation can help facilities drive down costs, unveil new space savings and run at their best through the ebbs and flows of seasonal demand.
More SKUs, Less Lead Time
Thanks in part to the large selection of product available online, consumers have grown accustomed to having a plethora of options to choose from, including with their food. They want more sizes, flavors, packaging types, as well as organic, nut-free, dairy-free, and gluten-free specialty products. As a result, food manufacturers have vastly multiplied the number of SKUs held in their warehouses. Add to that, the pressures of trying to meet shorter lead times, which are necessary to maximize shelf life and minimize chances of spoilage. Manual warehouses, in particular, can struggle with these distribution challenges.
Faced with a similar dilemma, Spanish grocery store chain, Mercadona, chose to automate its new facility in Guadix, Granada. Mercadona adopted warehouse automation as a means to support a corporate promise for freshness and customer satisfaction. Today, the Guadix distribution center is equipped with robots that provide buffer storage and order picking as one flexible operation. A warehouse control system manages material flow throughout the facility. The integrated system handles around 300 SKUs, covering everything from fresh fruit and vegetables to meat, stored in crates.
Fully integrated with the facility’s manual operations, the system manages goods reception, put-away, retrieval, picking of crates, sorting and assembly of crates into orders, and the loading of orders for delivery. In only six hours, the warehouse can easily fulfill orders for Mercadona’s over 1,600 supermarket stores.
Seasonal Peaks & Shrinking Spaces
The challenges of modern food distribution only compound during seasonal periods of high demand. During these tough times of the year, warehouses struggle not only to get orders out the door as fast as possible, but also to do so with an already limited staff. Further, there are often more products to handle, as manufacturing raises output to satisfy demand. Faced with more orders and on-hand inventory, warehouses end up suffering from a lack of space.
Global bread and roll manufacturer, Martin’s Famous Pastry Shoppe, Inc., experienced these challenges first-hand. In its warehouse in Chambersburg, Pennsylvania, workers previously had to hand pick items and moved orders across the warehouse for dispatch. Not only did this take immense time, with teams having to prepare orders hours in advance of a truck’s arrival, but the added strain of seasonal peak volume and an influx of seasonal workers left the distribution center cramped for space.
To address these challenges, Martin’s Famous Pastry Shoppe, Inc. looked to warehouse automation. It installed a combination of high-density pallet storage and retrieval, along with a robotic material handling system. Robots move inventory to storage in one of approximately 1,300 stack locations. Orders are picked by the robots, put into multi-SKU stacks and placed on a conveyor where they are sent for palletization and loading for transport. Each day, the system can pick 21,000 trays for distribution.
The system improved space utilization, requiring only 50 percent of the space used by its former manual process. Now the warehouse can prepare orders within an hour of dispatch, meaning more on-time deliveries. The automated system also eliminated the inherent work safety risks in manual fulfillment, reduced its man hours by 30 percent and removed human error from order picking.
A Fresh Take on New and Existing Warehouses
When manual inefficiencies can no longer meet the needs of the warehouse, many look to new construction. While it can be a good idea to start anew and design a larger facility ready for the future, advances in automation have made it possible for warehouses to optimize their existing footprints. By using a high-density storage solution, retrofitting can enable better space utilization, while making room for future growth and offsetting the costs of new construction.
Additionally, automation can be phased in over time through modular robotic systems. These types of solutions allow facilities to gradually expand their levels of automation, including their number of robots, based on immediate needs and requirements. This helps to keep costs down for a faster return on investment, and increases the longevity of the investment. For example, through a full-scale retrofit of its existing order picking system Fazer bakeries in Finland was able raise its productivity by 30 percent and secure a lifetime of up to 20 years of support.
For food companies already struggling to manage a growing number of SKUs and seasonal peaks, distribution will only become more challenging as consumer demand increases and the market becomes more complex. Manufacturers and distributors that invest in robotic material handling solutions today—whether through new construction or in a retrofit—will be well equipped to meet the demands of the modern food supply chain.
Derek Rickard is Distribution Systems Manager at Cimcorp.