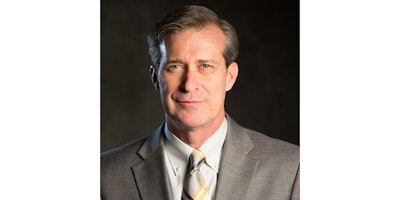
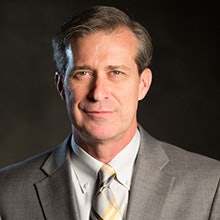
For decades, taste and convenience were the primary driving factors behind consumer purchases in the food and beverage industry. Today, choices and considerations are becoming more complex as consumers have an increased focus on health, influenced by cleaner labels, perceived benefits or risks (e.g., GMOs), and sustainability. Therefore, standing out and achieving market dominance can be difficult in this continually shifting landscape. Fortunately, modern software can help manufacturers focus on product consistency, product quality, and strict compliance. Quality can become an important differentiator, giving consumers recognizable distinctive characteristics that lead to brand loyalty.
Defining the Challenges
“Quality” is a very broad, all-encompassing term. To consumers, it typically refers to basics like appealing taste, texture, color, freshness and safety. To the manufacturer, packaging integrity, good manufacturing practices, shelf-life monitoring, and reliable compliance are the factors that deliver the quality consumers want. Managing all of these factors can be complex and costly for manufacturers since there is no single stop in the production line or one ingredient that can be the magic answer to quality.
When established, the objective behind the Food Safety Modernization Act (FSMA) was to have companies take a more proactive approach to food quality. Nearly all departments and operational stages in food manufacturing have an impact on final quality. Maintaining operational and product quality, therefore, involves many issues such as, the small print on packaging and large shipments of seasonal produce which must be processed quickly to ensure freshness.
Other challenges include:
- Need for Faster, More Precise Recall Readiness: Companies need to be able to quickly isolate suspect products, and the raw materials used to create them, to quickly remove any potential problems from the market
- Equipment Safety and Maintenance: One cause of quality problems in a food plant is poor equipment maintenance. Having solutions in place to monitor the equipment lifespan and performance is an often-overlooked element.
- Responsive to Regulation Inquiries: Regulatory agencies can require input from multiple individuals or departments, often taking time and causing delays which then affect freshness. Having collaborative and cloud-based solutions help teams expedite their response.
- Planning and Scheduling: One old – but still reoccurring – quality problem is caused by poor sequencing in the plant. For example, manufacturing a product without nuts after a run with nuts which can lead to allergy issues.
- Global Compliance: Labeling and formulation compliance is difficult, and even more challenging when the manufacturer distributes products in multiple countries.
- Flexible Quality Management: Quality testing requirements vary by product and customer account. Systems, therefore, need to be highly flexible and able to track a wide range of attributes.
- Unified Document Management: Manufacturers need to improve consistency and speed of communication internally and externally regarding specifications, lab results, labelling, etc. Without an advanced document management solution, version control can become confusing and lead to errors.
Applying Solutions
Mindset. Making improvements to quality starts with a commitment from the top. Quality control involves a mindset and a commitment of resources. Without the allocation of time, talent, and funds, making substantial improvements to quality will be difficult and slow. Top executives must set the standards and establish accountability. Additionally, teams need to be put in place, along with definitions, standards, check points, and action-plans. Turning quality into a differentiator is a company-wide endeavor. It does not happen overnight—or on a shoestring budget.
High Stakes. Keeping pace with modern definitions of quality and consumer expectations for traceability, consistency, reliability, and safety require advanced systems be put in place and backed by technology. Managing compliance testing, label accuracy, and tracking the journey of raw resources from the farm to the table can no longer be adequately managed by manual processes. The factors are too complex; the stakes are too high. One recall can destroy brand credibility and place major financial burdens on the company.
Visibility. Modern quality control and compliance solutions can be deployed to help eliminate silos, build connectivity internally and externally, monitor the many variables, assign tasks to team members, and streamline processes. Some of the tedious tasks can be automated, giving the workforce more time to focus on problem-solving and creative innovation. New solutions, developed by solution providers with deep expertise in the Food and Beverage (F&B) industry, can be valuable tools in connecting people and processes, as well as managing data, and creating visibility through the entire supply chain.
Speed. Access to data is not enough. Just as the consumer’s decision factors have become complex, the amount of data which can be collected about ingredients, specifications, testing results, equipment performance, sales, and customer feedback can be complex and overwhelming. The workforce needs tools to help sort and consume the data in order to draw meaningful conclusions. This means analytics with self-service reporting, dashboards, and role based Key Performance Indicators (KPIs). The workforce needs tools to make well-informed decisions quickly and efficiently. In the industry where freshness means success, timing is everything.
Agility. F&B manufacturers today face increased demands for new product introductions and offerings reflecting trends in wellness, sustainability, convenience, and clean labels. Trendy ingredients and packaging “buzz words” come and go quickly. Companies often respond to pressure with mergers, acquisitions, or Research and Development (R&D) investment in new product lines. IT systems need to be flexible and agile. Cloud solutions support the need for fast roll-outs in new facilities, new regions, or with new partnerships.
How to Get Started
Turning quality into a differentiator begins with evaluating the current customer bases’ perception of quality, identifying the existing production gaps and roadblocks, then crafting a strategic plan for making changes. Working with a solution provider who is well-versed in the industry will also be very helpful. Experience with proven applications is the difference between a theoretical concept and a practical application that generates measurable Return on Investment (ROI).
However, the most important consideration is to begin immediately. Keeping pace with demands and digital trends requires timely action and bold, confident moves. Companies who stall or struggle to invest in technology will fall behind, lose market share, and be at risk for remaining relevant. Get started by forming a task force to evaluate options, research potential partners, and draft the strategy. With some investment of talent and funds, quality can be an important differentiator, leading to lasting brand loyalty.
Mike Edgett is Director of Industry and Product Strategy at Infor.