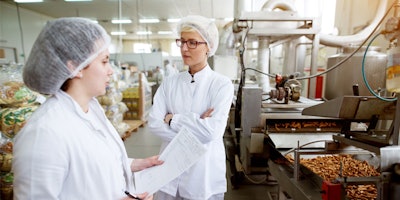
,
Meeting Food Retailers’
Requirements Through
X-Ray Inspection
By Michael Ahern and Rob Tiernay, Anritsu
B ig-box retailers have tightened their quality requirements on food manufacturers, and with good reason. Regulations are deepening as the regulators gain more
authority over the marketplace. Consumers are becoming more
educated and aware about the food they buy.
One indicator of the industry’s response is that nearly all food
suppliers’ mission/vision statements contain powerful language
about their commitments to quality, health, and trust.
RISK AWARENESS IN FOOD MANUFACTURING
Both food manufacturers and food retailers have an enormous
responsibility in providing consumers with safe, contaminant-
free food. Liability is a major concern for both parties, as
contaminated products can cause sickness, injury, or even
death. Should either unfortunately occur, it’s a very difficult
incident for a company to recover from.
Further, food recalls can be very costly — the average food
recall costs a company around $10 million. Brand reputation
and consumer confidence are also at risk for manufacturers
and retailers when products must be recalled. In the digital age,
news travels quickly through the internet and social media.
If recalls aren’t addressed and remedied swiftly, damage to
brand reputation and consumer loyalty can further escalate
monetary losses.
As food production plants become faster and more automated,
the risk for foreign-body contaminants in final products rises.
High-speed automation can cause more machinery wear and
failures that that drop machine fragments into lines. Unwanted
product pieces, such as bones from meat trimming, find their
way into processing. Naturally occurring objects, such as stones
from field harvest, enter the production process.
In response, retailers have become more vigilant about maintaining
strict quality specifications from suppliers.
Most retailers have standard, product-specific policies for food
manufacturers. For instance, a large retailer will set a policy for
bone fragments within ground beef. All ground beef producers
wishing to sell their products to that retailer must meet the
retailer’s requirements.
PREPARING FOR FUTURE
REQUIREMENTS AND REGULATIONS
Big-box retailers and regulators holding food manufacturers to
a higher standard is just the beginning. As time progresses, we
expect policies, requirements, and regulations will only become
more stringent. So, what can be done to prepare for them?
First, it’s important to have a quality champion in the plant.
Generally, this is the food safety manager, though titles vary. The
important thing is that someone takes the lead on safety and
quality and always strives for continuous improvement. This means
not just meeting current requirements but exceeding them. Being
ahead of the curve means your plant is never playing “catch up.”
A plant’s quality champion should absorb as much information
at every opportunity possible and share it with colleagues. Trade
shows provide an excellent opportunity to network with both
peers and solutions providers to learn the latest state-of-the-art
technologies and best practices.
The quality team should have well-defined inspection goals.
For example:
• Find 0.8 mm (or smaller) stainless steel in most food products.
• Achieve false reject rates of no more than 5 in 10,000
inspections.
FINDING THE RIGHT INSPECTION
EQUIPMENT AND PROVIDER
How can food manufacturers meet big-box retailers’ requirements
while running cost-efficient and productive processing lines? The
answer lies in choosing the right product inspection technology. In
many cases, X-ray inspection offers the most effective solution to
detect and eliminate contaminants.
The cost of X-ray systems may present financial obstacles for small
operations looking to do business with large retailers. To combat
this, retailers may offer incentives to their trusted suppliers to meet
the requirements. This could include, for example, setting aside a
small percentage of every pound of product sold for the supplier to
purchase the required equipment.
Finding the best inspection technology for your unique business is
imperative. One of the biggest mistakes a food manufacturer can
make in their search for inspection equipment is to buy the first
available option without research.
When buying a car, do you just go out and buy the first one you
come across? Or do you search for a car that provides the features
and conveniences you desire at an affordable price? Buying
inspection technology is no different. There are a wide variety of
Meeting Food Retailers’ Requirements
Through X-Ray Inspection
suppliers and models with numerous features, specifications, and
application suitability.
The right inspection system will fit two criteria:
1. Fulfill the requirements of the retailer and their audits.
2. Meet the food manufacturer’s needs and parameters and their
internal audits, as well as third-party audits they are subject to.
From there, manufacturers should research vendors and systems
capable of meeting those criteria. This can include asking advice
from retailers and other processors that make similar products, as
well as conducting independent research.
In most cases, several companies will claim to meet all the
manufacturer’s inspection needs, so it’s important to thoroughly
test the equipment from all potential vendors. The right inspection
equipment will meet or exceed the contaminant specs of the
retailer, the manufacturer, and the third-party auditor.
Performance
Here are some critical questions to ask when evaluating the
performance of X-ray candidates.
• What are your primary contaminant goals (type and size)?
• Does the equipment repeatedly meet the contaminant
specifications at actual production speed, with actual
products?
• Are the contaminant test samples consistent? (For example,
typical glass test spheres can vary in density by as much as 15
percent. That’s why Anritsu tests with synthetic quartz glass.)
• Do the contaminant test samples faithfully represent the test
goals?
• Is the inspection system giving false rejects? If yes, how
frequently? Is it possible to have the inspection equipment
meet virtual-zero false rejects — between one and five per
10,000 inspected products — based on the manufacturer’s
potential contaminants and size?
COST/TCO
Cost of the equipment is another important consideration, but not
just the up-front capital investment. Be sure to review the total cost
of ownership (TCO) over the life of the inspection system. Other cost
factors include parts, durability, labor, and energy consumption.
Equipment, the durability of parts, along with the cost of
replacement parts and maintenance should also be addressed.
What kind of warranty does the equipment come with? Is servicing
the machine incorporated into the initial cost of the equipment or
are there additional charges for diagnostics, parts, and service?
X-ray inspection equipment has two expensive replacement parts:
the tube and the detector. Be sure to consider how long these parts
will last and the costs associated with replacing them.
It’s also important to understand the relationship between high
performance and low-power use. Typically, power settings on
X-ray inspection equipment will affect the longevity of it and its
components. At higher power settings, components fail sooner.
At lower power settings, image quality and detection limits can be
compromised.
Anritsu has developed technology to offer end users the
benefits of high-power use and machine longevity. Learn more
about it here.
Another important consideration is labor. How many person
hours will it take to operate the inspection equipment each
day? Is the machine labor-intensive or highly automated?
How much training will be required for end users to properly
and effectively use the equipment? The answers to these
questions will play a part in the decision-making process.
Remember to also factor in energy consumption. How much power
will the inspection use during operation? Does the inspection
system have power-saving capabilities when not being used? Less
power contributes to a lower cost of ownership.
BEYOND CONTAMINANT DETECTION
Some X-ray machines offer added value you may not be aware
of, giving you useful capabilities beyond simply finding foreign
materials. This collection of secondary functions allows you check
product properties, including the following:
OVERALL PACKAGE
Virtual Weighing — By estimating weight from the X-ray image
density, the system can help you find over-/underweight products.
Package and Product Defects — The machine may have algorithms
that can identify deformed or broken products or packages with
product caught in the seal area.
Component Counts — This function finds packages with the
wrong number of components; for example, those missing a donut
or having too many in a one-dozen package.
REGIONAL ZONES/AREAS
Virtual Zone Weighing — This is similar to full-product weighing,
Meeting Food Retailers’ Requirements
Through X-Ray Inspection
but instead can identify specific areas in your package that are
over-/underweight.
OEE (Overall Equipment Effectiveness)
When deciding on an X-ray solution, don’t overlook its impact on
overall equipment effectiveness (OEE), a common measure of line
productivity and efficiency. OEE is usually calculated by multiplying
three percentages:
Availability — all events that stop planned production long
enough where it makes sense to track a reason for being down.
(Availability = Run Time/Planned Production Time).
multiplied by
Performance — anything that causes the manufacturing
process to run at less than the maximum possible speed when
it is running. (Performance = (Total Count/Run Time)/Ideal Run
Rate).
multiplied by
Quality — takes into account manufactured products that
do not meet quality standards, including products that need
rework. (Quality = Good Count/Total Count).
A typical OEE target might be 75 percent, which is far more difficult
than it appears. For example, if availability, performance, and
quality are all 90 percent, the OEE percentage would fall short of
the 75 percent goal, at about 73 percent (0.90 x 0.90 x .0.90 = 0.729).
OEE provides an accurate picture of how effectively manufacturing
processes are running and easily tracks progress over time. The
figure below helps illustrate the OEE calculation.
The following are OEE factors specific to X-ray inspection.
Availability Factors (eliminating downtime)
• Equipment reliability
• Quick cleaning and maintenance
• Ease of operation (setup, adjustments, product switching)
Performance Factors
• Line speed
• Product spacing
• False reject rate
Quality Factors
• Contaminant detection
• Product integrity (virtual weight, missing, defects)
• Clean, sanitary design (minimizing biological
contaminants)
Balancing Detection And False Rejects
Detection – The degree to which you can identify and remove
contaminated products from production.
False rejects – The rate that uncontaminated products are
incorrectly rejected as contaminated.
Detection sensitivity and false reject rates (FRRs) are closely
linked. Having the ability to find smaller contaminants than your
spec gives you more room to balance detection levels and false
reject rates. You can even have two setups for the same product.
For example:
• Sausage product menu #1 detects 1.0 mm stainless steel
with < 1 in 10,000 FRR (Best OEE)
• Sausage menu #2 detects 0.7 mm stainless steel with 10 in
10,000 FRR. (Best detection, or it could be run to release on-
hold products)
Both of the above solutions are possible using the same system,
simply by changing the menu to meet the application needs.
This additional headroom against false rejects
provides more latitude to tune performance when
optimizing production.
Data and Networking
The ability of inspection machines to provide comprehensive
data is critical to track and trace requirements,
troubleshooting, and production optimization. The data
should be accessible on-screen, via USB export and via
industrial networking protocols like EtherNet/IP or OPC UA.
For example, your quality or operations team sees an upward
trend in rejected products while monitoring the status of sliced
cheddar cheese packages. Examining the X-ray images in the
data archive offers clues as to the contaminant type, which may
help identify the causal source of the contamination. The X-ray
image also precisely shows where the contaminant resides in
the product, which can aid in retrieving the contaminant and
making quick, informed decisions.
Meeting Food Retailers’ Requirements
Through X-Ray Inspection
Or, in the event of a recall, your quality manager can reach into
the data to not only help identify the contamination source, but
also the scope of potentially contaminated products.
X-ray Vendor Service And Support
Service, support, and an ongoing partnership should also be
integral parts of searching for an inspection technology provider.
• Phone and web support should be available for
inspection systems 24 hours per day, 365 days per
year. Tech support over the phone should be able to
guide end users through most errors, problems, and
malfunctions. End user training should be included in
the initial purchase.
• A comprehensive kit of spare parts — photo eyes,
X-ray shield curtains, belts, and rollers — should
be considered in the initial equipment investment.
• Should the issue require a technician to visit the plant,
the technician should be on-site within 24 hours of
reporting the problem.
Again, the cost of labor, parts, repair, and downtime should
also be considered. How much will the inspection system being
down cost, and is there a plan to recover that lost revenue?
Not All X-Ray Machines Are Created Equal
A big part of continually exceeding retailer requirements
comes down to inspection equipment choices. X-ray solution
providers vary widely in performance, cost, reliability, and
application suitability. Making the right choices alleviates
concerns over shipping contaminated products, which
leaves you more time to focus on production.
The primary consideration for purchasing X-ray equipment
may be to repeatedly detect and remove the smallest
possible contaminants, but as you can see, the decision
process involves far more. You’ll also consider its ability to
exceed performance requirements, estimate the equipment’s
lifetime cost, evaluate service and support offerings, and
consider the supplier’s character.
As big retailers pressure food manufacturers to improve
quality, manufactures need to up their inspection game. This
means investing in better product inspection technology or
risk losing retail customers and their consumers. Although
X-ray inspection equipment is a substantial expense, it can
rapidly pay for itself if you purchase the right solution for
your environment and application.
Meeting Food Retailers’ Requirements
Through X-Ray Inspection
About Anritsu
Based in Japan, Anritsu was established as an electronics company in
1895, innovating test and measurement technologies for well over a
century. The company manufactures more than 1,200 X-ray machines
annually and is the largest food X-ray inspection system provider in the
world. Anritsu engineers and manufactures its equipment in-house with
top-tier components, offered at competitive pricing. Its X-ray systems are
regularly regarded as having the industry’s best performance.
www.anritsu.com ∙ 847-419-XRAY (9729)