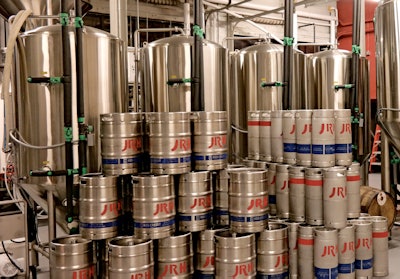
When John Henritze was 18, a senior class trip took him to Virginia’s Busch Gardens Williamsburg. While there, the idea of a brewing career first struck him. Despite that ambition, Henritze started working as a Physician Assistant out of college, but eventually his goal was realized. In 2011, he was accepted into the American Brewers Guild’s 2013 Craftsbrewer Apprenticeship program, a coveted, 28-week intensive introduction to brewing science and engineering.
At first, he enrolled to improve his home-brewing skills, but then decided he’d rather brew beer than toil in a 9-to-5 job the rest of his life. “Our motto is, ‘Life is short, don’t wait for the things you want to do,’” he says.
Soon after completing the Guild’s program, Henritze opened JRH Brewing in Johnson City, Tennessee, a municipality of 66,000 near the Blue Ridge Mountains. It consists of a brew pub and brewery, including a 48-seat tasting room that offers six different beers - stouts, IPAs, and pale ales, plus many more seasonals. He cans his biggest seller, Tree Streets Pale Ale, for a distribution to a growing fan base in the region
Challenge: Efficiency, Precision, Repeatability
JRH Brewing’s 5,000 square-feet brew house can produce 10 barrels, or 310 gallons, of beer at a time. The operation consists of four 10-barrel fermenters, one 30-barrel fermenter, and a 30-barrel brite tank. The latter is used to clear and condition beer, including carbonation, before packaging in either kegs or cans. Canning of the Tree Streets Pale Ale is outsourced to a mobile canning unit that comes to the brew house when needed.
“From the day we brew our beer to the day it’s packaged takes about a month,” Henritze says.
Henritze had bought the brew house equipment for his operation as a turn-key package from an OEM in Virginia, and learned that its design, especially most of its manual controls, were not located within easy reach. Brewing days became workouts. “When I first bought the brew house there were things I immediately noticed weren’t optimal with the process,” he says. “Most all the hand valves are located far away from the brewing platform, mainly because that’s just where they were put.”
So, while one hand valve for controlling beer flow from the brew pots was on the brewing platform, the temperature gauge was several steps down off the brewing platform, about 10 yards away from the heat exchanger. “And the manual valve for the cold liquor tank was another 10 yards further,” Henritze says.
If all his back and forth running between gauges, valves and controls wasn’t enough of a problem, Henritze found precision to be an issue, too. “I’d be running the pumps between tanks, then running down steps to reading the temperatures, which have to be managed precisely,” he says. The result was inconsistent liquid transfers with temperature variations that would affect the quality of the end brew product.
“If the temperature crept up, I’d have to run back over to the platform, run up the steps, slightly adjust the knob and then run back down to the temperature gauge,” he says. “It was like an old TV comedy, but I’d rather not have the workout and be able to focus more on making great beer.”
Enter Siemens
Fortunately, one of Henritze’s best customers was a Siemens automation engineer with whom he happened to mention his brewing issues. Given the engineer’s intimate knowledge of the Siemens industrial automation and control capabilities, it became obvious that JRH Brewing’s operations would make an ideal application for a SIMATIC solution.
Automating the process required the engineer to learn the details and the steps Henritze takes – literally and figuratively – while brewing beer. This included a walk-through of the brewery. At the conclusion of this discovery process, he designed a control system consisting of three primary components.
- Siemens SIMATIC S7-1200 programmable logic controller. This SIMATIC PLC model provides efficiency in performing basic automation tasks associated with managing the various temperatures and valves Henritze was trying to manage manually.
- Siemens SIMATIC TP700 Comfort Panel human-machine interface. With a 7" diagonal touch-screen, this HMI panel features 16 million high-resolution colors in providing a visual process diagram and dashboard.
- Siemens SINAMICS G120 variable frequency drive. This is general purpose vector drive that controls the two-horsepower, centrifugal pumps used to transfer wort and other liquids between tanks and pots. A 200V model was deployed.
The components communicate with each other using PROFINET industrial Ethernet. The system was programmed in just two days using the Siemens SIMATIC TIA Portal. With the Siemens SIMATIC automation and control system in place, JRH Brewing has increased the productivity and efficiency of its operations manyfold, Henritze reports.
“When we first tried it out, I was just amazed,” he recalls. “I could literally just stand there and push the button to get the pumps going to start the transfer. I don’t have to run up and down steps anymore. It’s fantastic.” Henritze figures that eliminating his physical back-and-forth meter readings and manual valve adjustments has cut his time on the brewhouse platform by more than 50 percent.
Henritze is also amazed at the new levels of precision he has in his brewing operations. “I’ve been able to reduce the variability in my brewing processes by about 80 percent,” he says. “That has helped me ensure that I can deliver the highest quality possible in my end products.”
For more information about the SIMATIC S7-1200 PLC, visit: https://www.siemens.com/global/en/home/products/