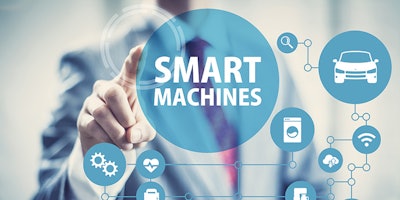
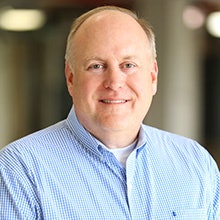
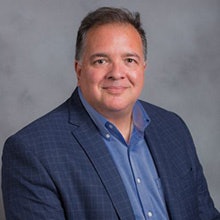
Smart machines and equipment can play a key role in helping food and beverage producers overcome the many obstacles and demands that come with satisfying today’s changing consumer preferences. A smart machine — which generally means one that is leveraging data and information to improve performance — can bring unprecedented flexibility, increased productivity and cutting-edge efficiency to the plant floor.
Despite this vast potential for increased innovation and competitiveness, the adoption of smart machines by food and beverage companies has been gradual, at best. Gardner, Inc., estimates that smart machines will enter mainstream adoption by 2021, with 30 percent adoption by large companies.
Food and beverage companies, understandably, have questions about how these intelligent technologies can fit into their operations. The right original equipment manufacturer (OEM) partner can help answer those questions and optimize producers’ benefits from their smart machine investments. Here are some of the factors food and beverage companies should consider:
Flexibility
Smart machines and equipment offer a new era of flexible production, which is especially important to food and beverage companies eager to please consumers’ tastes. Today’s customers want choices. Consider the proliferation of options in packaged snacks. Chips and crackers are no longer just available in family size. Consumers have their pick from snack packages to large cartons, with more options in between.
This modern appetite for variety among consumers means food and beverage companies need machines that do more, faster — without adding production lines for each new product. That means more frequent changeovers, effective batch and recipe management tools, using the same machine for multiple jobs and being flexible enough to meet future consumer demands.
Technology solutions like independent cart technology (ICT) and robotics can deliver much-needed flexibility on a production line. ICT provides the foundation for intelligent conveyance systems — advanced and efficient alternatives to conventional systems. These unique systems can safely and efficiently manage many carts across a network of linear motors. Using ICT, some OEMs have reduced changeovers from 45 minutes to just one. Overall, ICT minimizes complications and reduces time to market for food and beverage producers.
Robotics can also offer more flexibility to end-of-the-line operations, like packaging. Smart machines based around a single control system with robotic controls can enable faster communication of control, safety and process information, and more accurate control of machine movements.
In addition, advances in scalable batch and recipe management tools allow food companies to build more flexible production lines. In the past, a line may have been dedicated to a single product, but companies can now easily and efficiently change recipes on the same line.
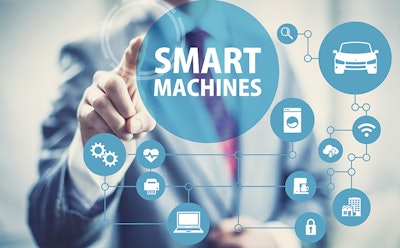
Data And Information
The primary difference between smart machines and traditional machines is information. By tying into an Ethernet-based network, smart machines can deliver invaluable, standardized data that food and beverage companies can use to optimize overall operations. Producers can leverage that information to improve decision-making around product stocking, delays in changeovers and more. Smart machines also open the option of storing data in the cloud, which is becoming more cost-effective and easy to manage.
Sensor technology helps OEMs design self-aware machines that can monitor their own key components and environmental conditions. This level of machine monitoring also enables preventive maintenance, supported by the OEM. Machines can consist of both wired and wireless sensors, allowing production lines to produce products more reliably and efficiently.
Working closely with their OEM, food and beverage producers can also deploy mobile devices to connect with smart machines. This can eliminate the need for operators to stand close to machines, allowing them to multitask while maintaining digital access to monitor and control their machinery.
Protection
Security is a normal concern for new users of digital production technology. With new equipment and exposed data, food and beverage companies naturally worry that proprietary information could accidentally leak outside the organization or be stolen by bad actors.
The good news is that security and safety are fundamental elements in the design of smart machines. Using a defense-in-depth (DiD) approach, robust security helps protect intellectual property, physical and human assets, and the environment. The DiD approach assumes any one point of protection can, and most likely will, be defeated. It employs layers of security through physical, electronic and procedural safeguards.
Data protection isn’t the only safety to think about when considering implementing smart machines. Physical safety in production facilities can also be improved with the integration of a smart machine through safety-system diagnostics that can alert operators when there is an issue within the system. Operators can resolve system issues before they present a risk to safety. As a proactive measure, data on equipment issues can be collected and stored over time to compare and identify trends across sites, allowing operators to take preventive steps to protect physical safety and enhance their interactions with machines. This could include allowing operators to service machines while still in motion.
Food and beverage companies no longer have the luxury of sticking with the status quo. Today’s market is full of fierce competition, and those hesitant to leverage and introduce new technology are falling behind. Smart machines and equipment can be a first step to producers keeping up — and winning — the market.
Steve Mulder is North America packaging segment lead at Rockwell Automation. Damon Sepe is North America process segment lead at Rockwell Automation