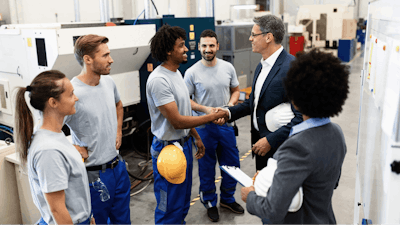
Maintaining a high level of production is one of the overriding objectives of an organization. Coupled with profitability, it ensures market relevance and competitiveness and, hence, its viability to remain in business. ‘Production’ here can as much relate to the rendering of services as it can the manufacturing of products. It is the output of industrial or commercial work and it’s therefore not surprising that it’s given so much importance.
However, an obsessive focus on production can have its downsides. One downside is that employees can get lost, resulting in employee fatigue and burnout, and, inevitably, a working environment in which employees are devalued. The devaluation of employee contributions at the altar of production is not a good thing. The critical key is to achieve a balance between high production and a content, motivated workforce. This article will show how.
The Limitations of a Sole Focus
High productivity is an intrinsically good thing and is central to high levels of production. It indicates that outputs, such as products made or services rendered, are outpacing inputs, namely costs such as labor and materials. It becomes negative when it’s made the be-all and end-all of employee performance.
A sole focus on productivity means ever-tighter deadlines and an ever-faster work pace, with workers usually having to work longer and harder. Unsurprisingly, this results in workers who are tired, stressed, resentful, and unhappy. Overworking is inherently unhealthy (and even dangerously so) for workers, as shown in multiple studies by the Finnish Institute of Occupational Health.
We need to remember that productivity was easy to assess in the days when workers simply clocked on and off with time cards, since the number of hours worked could be evaluated against products made. However, there has been an evolution of work, including flexible working hours and varied modes of workplaces. Even manufacturing has evolved in how shop floors operate. Robotics and automation have been highly disruptive in that regard.
Efficiency, Not Only Productivity
A solution is for managers to stop obsessing about productivity only. Efficiency has its place too.
At its simplest, productivity can be viewed as doing more with the same, while efficiency is fundamentally about doing the same with less. Of critical importance is that productivity is solely focused on output (how much is made), whereas efficiency is more concerned with the quality of work undertaken (how it’s made).
It shouldn’t, therefore, be difficult to realize that the role of the worker has greater value where the emphasis is more on quality of work (as with efficiency targets) rather than quantity of outputs (as with productivity targets). That is why, when management allows for a focus on efficiency, it can better ensure the working conditions and human needs of workers.
Efficiency can also be seen as the ‘bridge’ between inputs and outputs, helping to identify waste - such as wasted labor, time or resources. Productivity has its place, of course, but the focus cannot be solely on output, because to do so will be to the detriment of workers, their health and well-being, and, yes, productivity.
The Work Environment
The importance of a good physical working environment for worker satisfaction cannot be underestimated. An important factor is ergonomics, which is the relationship between an employee and their work station or working environment. It goes beyond merely being ‘comfortable’ in the way you sit or do your work, whether manual or sedentary labor. Poor ergonomics can be stressful to the body and mind alike.
Ergonomic work design needs to ensure that workers have an optimal working environment, regardless of their job function or the machinery or equipment with which they work.
Noise, which can be constant, intermittent or sudden, can also be disruptive to a worker’s concentration and can be stress-inducing. Besides either acute or chronic hearing loss, high or persistent levels of noise can result in a host of other physical ailments, from insomnia and nausea, to heart arrhythmia and hormonal disruptions.
Other occupational or industrial hygiene factors that need to be considered at all times include ventilation, illumination (lighting), thermal/temperature levels, and hazardous biological agents (HBAs), as well as internal air quality (IAQ), which incorporates factors such as oxygen, carbon dioxide, and humidity levels in the air.
Managers need to facilitate how workers can get their work done, including the ‘tools of their trade’. Different trades or types of work require different tools or equipment, whether it’s a bench grinder or a laptop. Work tools can be categorized as either those that are physical devices that allow work to get done or those that expedite work processes, such as software programs.
Whatever the tool or equipment, management needs to ensure that it is of the quality and working condition needed to get work done properly.
The focus cannot only be on the physical or technical attributes of what people do in their work. Work environments may differ, but managers must always ensure that management systems that facilitate and ease work are in place. Systems have many aspects to them that can assist workers in being more efficient and productive, yet valued, in their work.
One example is documentation, which comes in various guises, whether for the sake of worker safety and health or the quality of their work. Well-written documentation such as standard operating procedures (SOPs) should offer workers guidance, consistency and security.
Focus on Respect
Respect = valuing the knowledge and expertise of workers by listening to what they have to say. This helps prevent breakdowns in the workplace, such as having a disconnected workforce in a manufacturing setting.
Respect = being flexible with how work is done and how workers achieve their production targets. This is especially relevant in a post-COVID-19 reality, which has changed perceptions of the hours and where people should work.
Respect = creating a positive work culture, which actively values the role of all workers in the success of the organization. This is especially important as work has dramatically evolved to become “more cognitively complex, more dependent on social skills and technological competence, and more time pressured”.
The balance between high levels of production and worker satisfaction is a very fine one, but any organization that values its workers as much as it does its production outputs can achieve just that.
Bryan Christiansen is the founder and CEO of Limble CMMS.