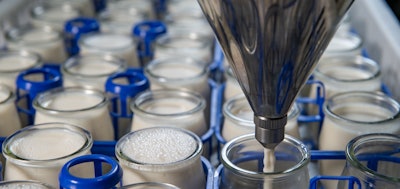
Food and beverage manufacturing is becoming a 24-hour production cycle. Because of this, production lines are now heavily automated. However, this increased reliance on sophisticated automation is making power quality issues more impactful, especially when it comes to food waste.
Food is delicate. Therefore, even slight power disruptions from the grid that interrupt production processes can lead to a lot of food waste. Disruption of machines in food production and refrigeration can mean large quantities of food being burnt, spoiled or contaminated, meaning that, due to stringent health and safety regulations, must be discarded. This can escalate fast in a continuous production system because if even one piece of equipment goes out of sync, and is not caught quickly, large quantity of products will go to waste.
Disruptions from low power quality can cause machinery to shut down in an unsafe manner. Low power quality is when power supplies are disrupted and no longer power machinery properly, such as voltage drops. These are sudden increases in current that cause voltage to drop over the impedance of a supply network, causing the voltage to vary. These voltage drops result in damage to machinery that may require parts to be replaced, or can lead to severe health and safety issues.
For example, if a conveyor was to break down while feeding bread through an oven, it could lead to the loaves igniting, which would not only cause severe damage to the conveyor belt and oven, but the fire could then spread putting the whole plant at risk. Improper shutdowns for smart-machines can also damage internal systems, scrambling the data and leading to faults and loss of precision.
The effects of power disruptions are also financial. The Pan-European Power Quality Survey reports that annual losses from power quality issues may amount to four percent of business turnover. This is set to grow as more processes become automated leading to power disruptions having larger effects on operations.
Food manufacturers understand that reducing food waste is a key method for creating a strong operation. The main way to reduce food waste is to have good control over processes. However, modern methods of increasing control through software and improved monitoring cannot have the desired effect if they are damaged through grid disruptions. As such, plant power quality should be closely monitored to prevent any unexpected interruptions.
Research shows that over 90 percent of power quality issues that lead to industrial equipment malfunctions are voltage sags. These happen when the RMS voltage decreases between 10 and 90 percent of nominal voltage for up to one minute. Voltage sags are generally caused by weather events such as high winds, heavy rain or snow build-up, but can also be triggered by traffic accidents and construction works. These sags can cause short circuits and overloads.
Businesses, sadly, cannot influence the weather or external works and must rely on other methods to protect equipment. Active voltage conditioners, such as ABBβs PCS100 AVC range, can sense power disruptions, such as voltage sags, and perform corrective measure returning the voltage to nominal levels. This will allow for undisrupted production reducing unwanted downtime and eradicating food wastage caused by system faults.
If an unprotected bottling plant for soft drinks were hit by power disruptions this could cause large losses through, for example, misalignment of injector and bottles. Formulas for soft drinks are also very delicate and loss of precision could mean that ingredient amounts could become skewed altering the taste of the product. By installing active voltage conditioners plant managers can rest assured knowing that these delicate processes are protected.
As food and beverage production becomes a 24-hour process, manufacturers need to take greater precautions to ensure both their equipment and staff remain safe while reducing food waste. Working with a provider to protect power quality can minimize issues and ensure your plant remains operational, whatever the weather.