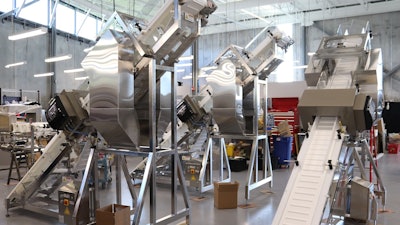
The "Holy Grail" of any food machinery investment is to maximize total cost of ownership in a sustainable way, without compromising performance and consumer safety.
Being able to upgrade to the latest, greatest inspection features is why one of the largest rice cooperatives in North America has remained loyal to Fortress Technology for over 15 years.
Continuing to benefit from Fortress Technology’s contaminant detection "Never Obsolete" pledge, the rice producer has in excess of 50 gravity, bulk, lab unit and groundbreaking incline conveyor metal detectors installed at its dry rice manufacturing plants located in the Southern United States. From a sustainability perspective, it’s the willingness of the engineering team to upcycle and repurpose legacy machine hardware and software and incorporate it into innovative new lines that keeps the rice supplier returning time and again to Fortress.
As with most food enterprises, waste, poor harvests, energy consumption, the pandemic and climbing rice prices have hit the sector hard in recent years. With the global rice shortage this year set to reach a 20-year peak, followed by a slight price easing in 2024, every grain counts.
Being able to offset some of these challenges knowing that machinery investments aren’t adding to these misfortunes can be especially reassuring for rice companies of this size, notes Fortress.
Processing and packaging more than 100 long and medium-grain rice brands - supplying grocers, restaurants, food service companies and exporting globally - Fortress has supported the farmer-owned rice cooperative by issuing a number of technology and machine upgrades. Analog metal detectors more than 10 years old have been converted to digital to improve contaminant detection and add data logging and reporting capabilities. Making them comparable to new Fortress metal detectors. However, in the latest and largest project, Fortress surpassed itself by reconditioning and mounting 13 existing metal detector heads onto new incline conveyor frames robustly designed to transport heavier bags of rice, introducing an innovative bi-directional sweep reject.
Robust inspection staples
Harvesting, milling, grading and packing over 60-million rice bushels annually, the US producer is reliant on robust best-in-class metal detection. Upstream, prior to packing, are a number of Fortress Gravity metal detectors located between product shoots and hoppers. Each rapidly inspects between 40,000 and 75,000 cubic feet of free-falling dried long-grain rice every hour, automatically rejecting metal contaminants from the product flow, along with only a minimal amount of rice.
Compact offline lab units are then deployed to quickly examine any rejected product and separate the metal contaminants from the rice. This enables the rice producer to filter out and rework all good product, helping to minimize waste and identify contaminants for further investigation.
For large bulk bags of rice weighing up to 110lbs (50kg), large bag metal detectors – known widely as the Big Bag King – are, for weight and safety reasons, located at floor level. Featuring a large aperture, a special coil structure, and Vector heavy-duty conveyor to accommodate the heavy bags, this market-leading bulk inspection metal detector can guarantee center of aperture detection of ferrous and non-ferrous metals as small as 1.5mm, and 2.0mm non-magnetic 316 stainless steel contaminants.
Given the limited floor space, to inspect the smaller rice packs weighing up to 20lbs (9kg), Fortress engineered an incline conveyor frame. Measuring 14 feet in length, packs move up a special flighted conveyor belt at a 45° angle. Designed to handle a fast product rate, a Stealth metal detector with a customized head and aperture ensures performance and detection sensitivity is not forfeited. Having ground-level remote access enables staff to safely select the inspection parameters and access data from the metal detector heads if the HMI control panel is beyond reach.
Sustainable and waste reducing
Many Fortress engineers contributed to the design. Yet, a testament to the level of detail and collaboration that goes into each and every Fortress commission, company founder and President Steve Gidman couldn’t restrain himself from getting involved.
Gidman reflects: “Because the conveyor was inclined and as the product had to be rejected perpendicular to the flow, rubber grips were not advisable as they would inhibit reject performance, damage bags and make a mess. Knowing that this would create unnecessary waste, to address this we instead opted for belting with flighted sections. This solution allowed the rice bags to be conveyed uphill at a steep angle, without impacting the lateral rejection.”
Due to the high product rate – on average 150ppm – and the flighted belt, deploying a reject device with a return stroke was not considered ideal. To avoid collisions with the belt features and trailing rice bags, Fortress instead created a bi-directional paddle sweep reject. Rejecting contaminated packs on either side of the conveyor, chutes funnel rejected product safely to ground level, securing it behind lock and key for authorized quality control personnel to remove.
For this customer, like many, the sensitivity of each metal detector combined with the compatibility of components, provides added assurance that investments can be spread out. Knowing that the technology will never be obsolete is especially valued, claims Regional Sales Manager Jake Murray. This processor, for example, is currently upgrading more than 10 Phantom metal detectors to Stealth, on machines purchased over 10 years ago.
“These machines are still fit-for-purpose. However, like many expanding companies, this rice producer now requires data logging capabilities. Because Fortress always sticks to its universal modular design, upgrading to a Stealth is very straightforward. Not only does this save customers a lot of money disposing of and replacing assets that remain perfectly functional, it also prevents industrial assets adding to the environmental costs,” Murray said.
As well as being responsible waste stewardship, upcycling inspection assets where possible is a big tick for food processing stakeholders striving to achieve their sustainability reporting goals.