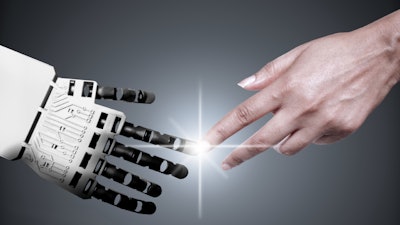
It’s no secret that there’s an escalating workforce shortage in the food manufacturing industry.
It’s also no secret that this shortage threatens manufacturers’ ability to meet consumer demand - which is itself continuously rising - both in terms of quantity, as well as quality. As the food industry becomes increasingly competitive and demanding, with ever-more SKUs and more alternatives than ever before to consumers’ favorite brands, this workforce crisis couldn’t have come at a worse time.
Much of the talk about Artificial Intelligence in the context of the workforce tends to revolve around AI taking jobs away from humans. But that “solution” to the workforce shortage isn’t anywhere on the horizon.
“Lights out” manufacturing is still a long way off, especially for complex, process manufacturing like baked goods and many other food products. In fact, it might not ever happen, for the simple reason that these dynamic, complex processes depend heavily on human expertise and decisions. Looking at the problem from this perspective, the challenge is all the more daunting. How is it possible to run an excellent factory and beat the competition when it’s so difficult to recruit and maintain a world-class workforce ?
Ordinary Teams - Extraordinary Results
- AI can provide the right knowledge, to the right people, at the right time. One of the main limitations of human beings is our ability to process and analyze data. On any given production line there can be hundreds or thousands of data tags, many of them interrelated in complex, dynamic ways. There’s also a lot of noise, and missing data. As a result, any human-driven analysis will always be limited, and many important insights will inevitably be missed. This is particularly true when the cause of a production loss isn’t immediately visible to the human eye. The oven and conveyor may be within their permitted ranges, but if they both operate at a certain level at the same time, with a particular variance in the raw ingredients, that could cause a spike in losses. Machine Learning algorithms can spot those trends, and alert the right people, in real-time, so they can take corrective action before that inefficiency translates into significant production losses.
- Using AI, factories can build and maintain knowledge and expertise - regardless of staff turnover. Another way in which humans are limited is in our ability to store knowledge and learn. Training a new team member takes a long time and a lot of effort. AI algorithms, by contrast, can “learn” many times faster - and then store those learnings in an easily-accessible format for teams to use and build on in the future.
- Your teams spend less time figuring out why problems occur, and more time fixing them - with the correct insights. AI can take over tasks that humans aren’t suited to - and perform those tasks faster, more efficiently and more effectively. That’s particularly true of data-related tasks. With the heavy lifting of the “figuring out” aspect of work largely done by Artificial Intelligence, your teams can apply their abilities and expertise where they truly excel. Equipped with these capabilities, manufacturing teams are freed from much of the arduous, time- and resource-consuming work that weighs them down. This formula of AI + human talent thereby alleviates the workforce shortage - because your existing teams can simply do a better job by focusing on what they do best.
Barilla Cut Waste by 37 Percent with AI
Many food manufacturers feel ill-prepared for Artificial Intelligence, as they lack data. Indeed, before deploying Artificial Intelligence to a line there must be a data infrastructure. This is a worthwhile investment that will pay off.
One recent example was at baked goods production giant Barilla, where a high-demand production line was experiencing significant waste losses. Their plant leadership knew they needed to enlist technology to cut those losses, but were initially skeptical about AI, as they had no data.
Four months later, the initial skepticism was a distant memory. Not only had they built a robust data infrastructure, but in that short timeframe they’d implemented Seebo’s advanced Artificial Intelligence solution and saw a 37 percent reduction in waste losses.
In conclusion, Artificial Intelligence offers a way out of the workforce shortage for food manufacturers. By adopting AI, manufacturers can excel with their existing teams, and hire more strategically by attracting top talent with the promise of the latest technology - which will in turn enable them to excel at their jobs, and in their careers.
Perhaps most importantly: Artificial Intelligence is not a mystical technology only meant for the most “advanced” production lines. Even manufacturers with little to no data can adopt advanced AI in relatively little time, and with less effort than many fear. And the results speak for themselves. Little wonder then that the world’s leading food manufacturers are all investing in Industrial AI.
Liran Akavia is the COO and co-founder of Seebo.