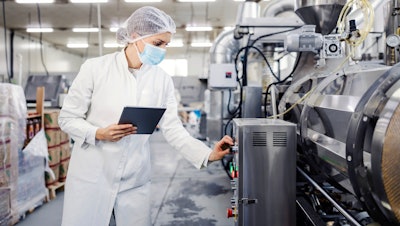
Early this year, food recalls hit a five-year quarterly high. As food manufacturers are all too aware, some recalls are beyond anyone’s control—but many others can be preempted through quality control, product safety, and operational efficiency. In 2026, the FDA’s Food Safety Modernization Act (FSMA) will issue new recordkeeping requirements to more easily identify and remove contaminated foods from the market. As the industry faces tightening regulations on top of constant consumer demand and greater competition, food manufacturers may be looking for a leg up. A solid data management strategy, which can optimize every facet of a manufacturing plant, is a great place to start.
Why it Matters
Food manufacturing involves a great deal of data generation and collection, from receipt of raw materials to delivery of finished goods. This includes information on ingredient sourcing, quality control measurements, production line performance, supply chain logistics, and regulatory compliance records. Manufacturers must synthesize and contextualize all this data to maintain consistent product quality, ensure food safety and traceability, optimize the production processes, meet a slew of regulatory requirements, and make informed business decisions.
How it’s Done
The foundation of effective data management is accurate and comprehensive data collection. Today’s modern manufacturing facilities capture data using advanced technology like smart sensors and Industrial Internet of Things (IIoT) monitoring devices. Many other facilities, though, have yet to embrace this digitalized, data-forward approach. Even among manufacturers who say they’ve completed their digital transformation, 61% still collect data using non-digital processes. Not only does analog data collection introduce the possibility for human error, but it represents an opportunity cost in terms of overall optimization. By implementing standardized and digitalized data collection protocols, manufacturers can mitigate risk and ensure greater consistency and reliability – even across different production lines and facilities.
Of course, any data being generated and captured must also be stored. Secure and accessible data storage is crucial. Fortunately, with options like cloud storage, on-prem, and hybrid configurations, businesses can safely store their data in the way that best aligns with their needs and capabilities.
In order to be actionable, data must be contextualized. Advanced analytics tools help transform raw data into actionable insights by offering real-time context, retrieving historical patterns, and extrapolating trends. Software solutions like manufacturing execution systems (MES) use this data to provide predictive maintenance models, quality trend analyses, and production efficiency dashboards.
Establishing clear policies and procedures for data management ensures data quality, security, and compliance. Manufacturers should set guidelines for data ownership and access, implement data validation procedures, ensure data privacy and security, and establish data retention and archival policies. Creating a data-driven culture within the organization is essential for success. This means employers should be upskilling and training workers of all levels to appreciate the importance of data, correctly input and interpret it, and use insights to make informed decisions.
Making it Work
Data management is an important factor in consistent product quality. By tracking and analyzing production, manufacturers can easily identify and address quality issues, optimize processes based on precedent, and ensure compliance with quality standards and regulations.
In the event of a food safety issue or recall, proper data management facilitates rapid data retrieval. A strong data management system allows for quick identification of affected products and batches, ingredient traceability, thorough record-keeping, and regulatory compliance. Data management goes beyond the factory floor, rippling out to fortify and clarify a facility’s entire supply chain. This allows manufacturers to optimize inventory levels, increase demand forecasting accuracy, and reduce waste while improving sustainability.
As demonstrated by FSMA’s forthcoming update, the American food industry faces stricter standards and regulations than other industries—and for good reason. Proper data management practices can help manufacturers maintain required documentation, meet compliance during audits, quickly respond to any inquiries, and adapt to ever-evolving regulatory requirements.
A Process that Evolves With You
A solid data management strategy can bring comprehensive benefits to food manufacturers’ productivity, efficiency, and visibility. But implementing and maintaining it can come with challenges. On an ongoing basis, manufacturers must ensure that data is accurate and complete, which may be a big lift for those still relying on non-digital data collection. Advanced software solutions are designed to streamline this process. Manufacturing leaders who are, understandably, concerned about the short-term cost of digitalization should also consider the long-term costs of falling behind competitors. Starting small is not only a good way to curb expenses but is also a responsible way to oversee the change management process. As operations grow and data volumes increase, an organization’s data management system should be able to scale as well.
Sound data management is a necessity for modern food manufacturers on the road to Industry 4.0. By implementing comprehensive data collection, storage, and analysis, manufacturers can enhance product quality, ensure food safety, improve operational efficiency, and maintain regulatory compliance. As the industry continues to evolve, manufacturers that embrace data-driven decision-making have greater odds of thriving in an increasingly competitive and regulated environment.
Bill Rokos is the chief technology officer of Parsec Automation.