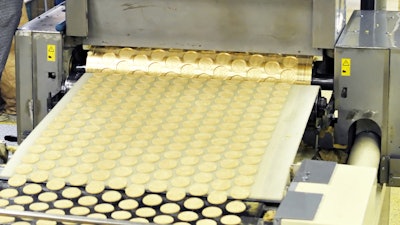
Quality assurance and quality control are vital for food manufacturers. While quality assurance requires a product to be produced a certain way and match the product label, food quality control is more rigorous in its demands. Food quality control requires manufacturers to meet both safety and consistency demands.
Manufacturers must ensure they source ingredients from approved suppliers, meet specific recipe composition percentages, and maintain product standards. It is imperative that government regulations are met and that the food products on the shelves are safe to eat. This develops trusting, loyal consumers that make repeat purchases from brands that deliver on their quality promises.
Advanced technologies, including the Industrial Internet of Things (IIoT), can immensely improve food quality control measures and outcomes. Leveraging IIoT can help food manufacturers optimize production processes in reducing costs and waste, all while meeting—or exceeding—quality standards.
Automate When Possible
Let’s note that automation does not mean replacing every human in your factory with a machine. In fact, most Industry 4.0 technologies are designed to empower factory employees. These tools can give employees time and energy back to solve bigger, more complex problems.
Live monitoring enables teams to catch quality issues faster. Live alerting can notify teams about a machine or production issue early, giving them the ability to react quickly and minimize the impact on quality. Over time, Machine Learning (ML) can identify the conditions under which these issues occur. This makes it easier for teams to reduce product and equipment variability.
Comprehensive, easy-to-read dashboards displaying machine uptimes and statuses enable employees to have a pulse on their production, whether they are working from a control room or remotely. These tools save both time and money while making it easier for teams to improve uptime and reliability.
In addition to improving food quality control efforts, Industry 4.0 tools can also retain employees, boost morale, and improve worker safety. When considering a smart factory, companies often want to automate as many processes as possible. In fact, automated tools can be very beneficial for your teams and take tedious or dangerous tasks from your human workforce. While cost will always be a factor with technology it’s worth considering the monumental value it can have on your organization.
AI Recommendations and Insights
Saving time and energy aren’t the only benefits of Artificial Intelligence (AI). AI can help employees learn more about their process by presenting new complex and counterintuitive insights that may otherwise go undetected. For example, AI may discover that a company could save energy by running a fryer at a higher, consistent temperature instead of varying between a wide range of temperatures.
AI can also help employees (especially process experts) validate their instincts. Pairing implicit knowledge with AI discoveries enables employees to investigate their intuition with data. The technology handles the heavy-lifting of wrangling data and complex calculations while employees focus on using their unique process insights.
Augmented Computer Vision
Computer vision (a type of Machine Vision System, or MVS) has been used to improve food quality control for quite some time. Many manufacturers are likely familiar with some fundamental uses of computer vision, including detecting product uniformity (e.g., size and shape), though computer vision has also been used to ensure proper package filling amounts, sorting different products post-production, and more.
Automated computer vision is more accurate and less labor-intensive than human quality control. It should also go without saying that computer vision is drastically faster than using humans for visual food quality control.
According to the Food Marketing Institute and the Consumer Brand Association, product recalls cost food companies an average of $10M in direct costs, “in addition to brand damage and lost sales.” Identifying and minimizing quality defects, particularly those that pose health issues to consumers, can save food manufacturers excessive losses.
Computer vision has advanced to the point where it can detect color changes or physical properties of foods. There are even some European companies that are using computer vision to detect black spots, blisters, and dangerous by-product chemicals in potato chips.
Research is also examining how computer vision can detect the microbiological qualities of food products. This is a huge step forward in reducing product recalls related to dangerous microbes. In 2016, microbiological contamination accounted for 47 percent of all recalls in the United States. Imagine if these recalls could be stopped at the source before causing disastrous outbreaks?
In the case of packaged foods, computer vision can be used to detect the “freshness” of a product using a Time Temperature Indicator (TTI). The use of computer vision technology means that poorer quality products never need to leave the factory; quality issues can be detected before they ever make their way to customers.
Used on its own, it’s hard to imagine computer vision doing much more than identifying straightforward product defects or sorting different end products. This is where IIoT technologies start to shine.
Improved Root Cause Analysis
Food manufacturing is complex: many food production processes generate hundreds, if not thousands, of different process parameters. The massive amounts of data can make it difficult to uncover root causes when problems arise.
With so much data, it’s not always clear where to look for the cause of a quality issue. For example, let’s say a food company receives an alert about an abnormal rise in quality rejects. The process engineer can’t determine the root cause as no noticeable settings were changed.
By automating data crunching and analysis, teams save valuable time. They can narrow in their efforts quickly, guided by the AI, and start finding solutions quicker than if they had to perform the same tasks manually. As the adage goes, time is money. Every minute saved in this part of the process saves you countless dollars down the road trying to continuously put band-aids on recurring quality issues.
From live monitoring with triggered alerting to AI-augmented computer vision, there is a wide range of IIoT tools available to food manufacturers for improving food quality control. These tools come at a variety of price points. They also deliver a range of cost, scrap, and time savings.
Many of these IIoT technologies are enhanced, if not driven by, Digital Twins. Digital Twins are at the core of many Industry 4.0 tools and digital transformation as a whole.
Automating different parts of the food manufacturing process can have a significant impact on quality control across a variety of food products. Even though these tools are an automated part of the production process, these tools are designed to help your employees, not replace them.
Laurent Laporte is the president and CEO of Braincube.