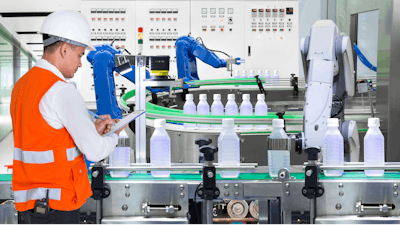
Isaac Asimov’s first Law of Robotics states that “A robot may not injure a human being or, through inaction, allow a human being to come to harm.” The issue of inaction is especially relevant right now, as the coronavirus pandemic highlights the need for manufacturers to use automation and robots to reduce the number of workers on the factory floor, and protect the safety of those who remain. Here, Claudia Jarrett, US country manager of EU Automation, argues that manufacturers aren’t going far enough.
A good example of an industry that’s been particularly affected by COVID-19 is meatpacking. Recent figures by the Centers for Disease Control and Prevention (CDC) counted 16,233 positive cases of coronavirus among US meat processing plant workers, across 23 states.
This widespread problem demands a wide-reaching solution — but what, exactly? The answer lies in automation. As recommended by Pricewaterhouse Coopers (PwC) in its report, COVID-19: What it means for industrial manufacturing, plants should turn to automation to reduce the number of workers on the factory floor.
Surely enough, meat processing companies are developing robotic processing systems. A white paper by PMMI Business Intelligence, Automation Timeline: The Drive Toward 4.0 Connectivity in Packaging and Processing, cites one leading company that has invested $500 million in robots during 2017 alone. So far, so good.
But what do I mean when I say some manufacturers aren’t going far enough? The same report also states that many manufacturers are stuck in an “end-of-line” box. It says: “They are hard-pressed to envision robotics applications outside of traditional roles in secondary packaging and palletizing.”
In its own survey of consumer packaged goods (CPG) manufacturers, PMMI Business Intelligence identified several stages in the production line where cobots and robots are underused. It found that only 13 per cent of CPGs used them in depalletizing processes. 20 per cent used robots in product handling, seven per cent in product processing, and 20 per cent in filling, dosing and pick-and-place applications. This underuse was also apparent in manufacturers’ planned future projects.
Robots are mostly used in just a handful of areas on the production line, like secondary packaging and palletizing. Yet the designs and capabilities of robots have evolved beyond these end-of-line applications. So, how can managers think outside of the box in how they deploy robots and cobots?
EU Automation
Broader horizons
It isn’t only that manufacturers don’t realize the potential of robots beyond the end-of-the-line processes. Robots or cobots can also seem like a daunting financial investment — although they needn’t be! Plant managers might also worry about having to deal with unfamiliar programming languages, or the added cost and disruption of needing the help of third-party integrators.
In other words, can robots fit into their existing ways of doing things? This is where original equipment manufacturers (OEMs), suppliers and integrators — or a automation parts suppliers — can offer valuable guidance.
Manufacturers may not be aware that today’s robots offer new levels of flexibility and bespoke capabilities. They will be integral to realizing the industrial demands for smart factories, flexible and modular interconnectivity, with more powerful and reliable wireless connectivity on the factory floor.
Large, cumbersome robots — as seen on General Motors’ automotive production lines in the 1960s — are a thing of the past. There are delta robots — with three arms connected to universal joints at the base — upside-down robots and vision systems used for palletizing and boxing, small assembly and cutting in food and beverage applications. Equipped with components like high-speed valves or grippers that can handle more precise, even delicate, applications, these robots can support continuous manufacturing with high levels of throughput.
These robots also offer Industrial Internet of Things (IIoT) connectivity with fewer inputs/outputs (I/Os) or wireless capabilities. They offer productivity benefits in smaller production systems, or in areas of the production line where robots have been underused.
This connectivity to also help manufacturers better integrate their production lines — crucial to the operation and overall efficiency of any production line. For instance, an unnamed manufacturer in PMMI Business Intelligence’s report, describes itself as having ten lines “that are about 70 percent automated but not yet integrated.”
Smaller, more flexible and connectible robots can help manufacturers get beyond their integration shortcomings, and consider the many factors that should be taken into account when integrating a packaging line. Some of the most important ones are: available floor space, required throughput speeds, proper spacing between machines, future expansion and workflow of the packaging line.
Seeing the light
As robots and smart sensors increasingly prove their worth, the support of an industrial parts supplier can be vital in helping manufacturers choose the right sensor for their packaging application. Parts suppliers can source sensors for packagers, ensuring the transition can be achieved without requiring a complete overhaul.
With several advancements in automated technology, packagers can learn to integrate their existing processes in order to implement robotics across their enterprise.
PwC’s report puts it best: “Expect a learning curve as companies devise new ways of working that involve more remote workers and automation on the factory floors.” But, going forward — in reference to Isaac Asimov’s first Law of Robotics — inaction shouldn’t be as much of an issue, as manufacturers become more aware that they can add automation and robotics in general across their lines.