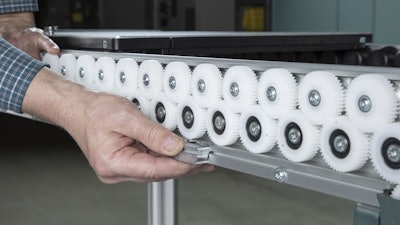
Dorner’s ERT250 is a new, innovative roller technology-driven conveyor system for pallet and tray handling. The rollers are driven by an energy-efficient linear gearbox that provides added flexibility with motor positioning and zoning. It also allows for zone and slip roller operation. Simply removing a lower gear creates independent zones.
Gearmotors & Gears
The motor also can be relocated every 250 mm. This can be done easily in the field. This might be necessary if the conveyor was ordered incorrectly or if the application changes and you need to reconfigure. If you need to create new zones, lower gears can be removed and a gearmotor added.
Drive Shaft Position
An additional option for reconfiguring the system lies within the drive shaft location. Rollers are situation on each side rail. In order to move both sides the drive shaft connects across the conveyor typically between rollers. With this layout there is approximately 10 mm of clearance below the pallet.
By moving the drive shaft to the fame below the roller, the clearance below the pallet is now increased to 45 mm. The only drawback to moving the roller to the frame versus attaching it to the rollers is the drive shaft is no longer moveable in the field. The slot for the drive shaft is machined into the frame.
If an application calls for complete clearance, say bars poking through the bottom of the pallet, and 6” of clearance is required, there is the option to remove the drive shaft completely and add a second gearmotor. Each side rail and motor would run independently. As noted, one of the benefits of the controller is that it can drive two gearmotors, so the two motors will be electronically synced. It’s not completely synced but well within what’s required for a roller conveyor system.