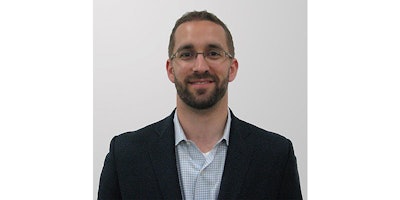
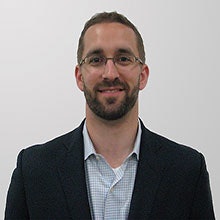
Technological advancements in permeation analysis are capable of providing critical input to food processors so that the best possible packaging materials are used to protect products intended for consumer consumption. With shelf life, as well as economics, principle drivers in today’s packaging material selection, it has become even more critical to understand the structure’s performance attributes and related costs.
Additional trends that are impacting the need for accurate permeation testing include the evolution to transparent structures from foil or metalized-based materials, as well as locally-grown/regionally distributed food items and fresher, healthier options.
The ever-present discussion of environmental impact of packaging components and the desire to reduce natural resource consumption can also dramatically impact permeation.
Permeation dramatically impacts shelf life
Permeation testing is a critical component to successfully pushing the shelf-life envelope. A package can have perfect seals and closures, optimal mechanical properties and modified atmosphere (gas flushed with a mix of nitrogen or carbon dioxide). However, neglecting to measure and manage water vapor transmission rate (WVTR) and oxygen transmission rate (OTR) moving through your packaging materials can be catastrophic to a product’s shelf life.
From a barrier perspective, there is an abundance of over- and under-packaged products in the market today. These performance failures have a significant economic impact on brand owners. A common response to an oxygen-sensitive product is to package it in an expensive foil structure, which is typically perceived as the ultimate barrier. This can result in paying for more barrier performance than a product actually needs. Alternatively, products often end up under-packaged when a common structure or stock package is used for a new product with higher oxygen and water vapor sensitivities.
These quick and simple, but costly, approaches to packaging may be prevalent because measuring WVTR and OTR historically has been incredibly time consuming, complicated, qualitative and expensive. Permeation testing is often a bottleneck in organizations ranging from resin and raw materials suppliers to packaging manufacturers and brand owners.
New permeation capabilities shortens test cycle
The general rule for permeation is “better barrier, longer test.” The more sensitive a product is to oxygen and water vapor, the longer the packaging development efforts will be to ensure the shelf life is safe, known and predictable. In the past, this meant a permeation test required days or weeks to complete. When compared to minutes or seconds that a tensile, puncture, or seal strength test might take, the length of time necessary for permeation testing could be perceived as a process negative.
Food processors want to make sure that their new products get to market as quickly as possible. However, in order to do that, you need testing equipment that gives you results as quickly as possible. Recent advancements in permeation technology have resulted in instruments capable of measuring those same barriers in up to half the time. Testing that used to take three days to complete, now can require as little as a day and a half. This is due to increased sensor capabilities and decreased background leaks and noise in the electronics. The increase in throughput can impact how many options can be evaluated, how many different internal and external customers can be served, and how quickly food processors can get new products or repositioned products to market.
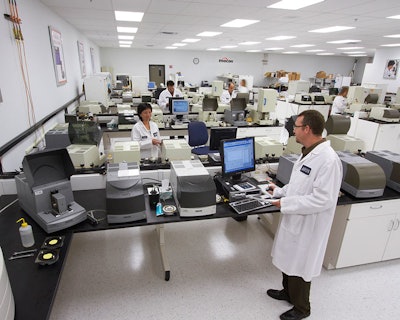
Automation helps simplify complex operating parameters
New permeation technologies also have addressed the barrier testing complexity. Manual methods, such as gravimetric water vapor testing, and even instrumented testing methods, have placed significant training and expertise demands on the shoulders of packaging development labs. Manufacturer resources are strained as they deal with employee turnover and highly-skilled, Baby Boomer packaging pioneers leaving the workforce.
One way that this is being addressed is by permeation instrumentation manufacturers is to increase automation features. This helps shorten the learning curve for operators and reduces the need to rely on employee expertise. Prior generation instruments required mastering complex software, manually adjusting testing conditions, and repeated use to become proficient in running these tests. New technologies incorporate touch screen interfaces and automated control of all testing conditions and variables, only requiring an operator to input their desired parameters into the user-friendly software.
Automation and ease-of-use correlates directly to the labor-associated costs of permeation testing. Permeation testing proficiency, formerly requiring months if not years of experience, can now be achieved in weeks. This opens the door for food processors and packaging manufacturers to adopt these technologies without adding significant labor resources. Operators of new permeation instruments spend less time in front of the instrument and more time performing other tests and tasks.
Need for improved barriers drives testing needs
The need for better barriers is a major driver of new raw materials, coatings and processing development. As the requirement for these new barriers has increased, permeation instruments have been getting more sensitive, precise and repeatable. Today, new oxygen permeation instruments are capable of measuring OTR down to levels of .0005 cc/m^2*day while WVTR instruments can reach .00005 g/m^2*day. Lower leak rates and more sensitive electronics has made them more repeatable and precise at those low levels. These levels of sensitivity and precision allow for more effective differentiation between competitive materials and packages.
Older methods and technologies have been less capable of measuring the very small barrier differences in packages. This supported a qualitative ranking of materials but may not have been sufficient to properly quantify the differences of barrier materials and measure their impact on shelf life. The cost of a wrong answer or qualitative answer in permeation, represented by product shelf life failures, greatly outweighs the expense of ensuring the proper barrier materials are selected for a particular product.
Purchasing permeation equipment or using a lab for testing?
Permeation testing plays a critical role in both R&D and quality control across the supply chain. Resin and chemical companies use permeation instruments to qualify their raw materials and ensure production meets target specifications. Packaging manufacturers and convertors must evaluate the barrier properties of those materials after they have been formed into flexible or rigid packaging. Brand owners regularly test incoming packaging for barrier quality and invest in their own research and development to ensure target shelf lives are achieved.
Companies at every stage of packaging development must decide the most efficient and effective way for them to accomplish their barrier testing needs. Instrument ownership is a must for many companies in the supply chain. Food processors and packaging manufacturers around the world can test anywhere from one sample to many hundreds of samples at once, often with their instruments operating 24/7. Owning instruments allows them to accommodate constantly changing demands. These companies are benefiting significantly from throughput improvements, ease of use, low labor costs and increased precision and sensitivity of the latest generation of technology.
While brand owners may plan years in advance for their growing barrier packaging requirements, permeation instrument ownership might not be enough to support all of their needs. New product launches and new material evaluations can overwhelm internal permeation labs. These projects are often timeline-critical, extremely sensitive to turnaround and can significantly stress internal resources.
Contract analytical laboratories around the world have invested in permeation instruments to support their additional throughput needs. A contract lab with 20 or 100 instruments can turnaround a key project in a fraction of the time a brand owner with five instruments can manage. These labs may even specifically dedicate instruments to a project for an extended period of time.
These contract analytical services also support companies which only need occasional barrier testing or those who are just getting into the barrier packaging. Outsourcing barrier testing to a lab may be a more efficient use of resources than instrument ownership, however turnaround time and agility may be sacrificed with this approach. A history of outsourced testing may help justify a future instrument investment.
Ultimately, resources are available in a variety of forms to help companies of all sizes address and capitalize on the industry trends at play. Further innovation will be driven by the right combination of emerging technology, new industry partnerships and employee expertise.