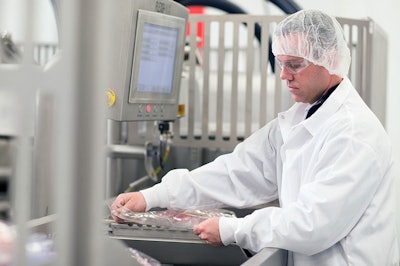
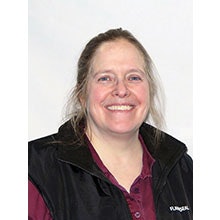
Editor's note: This article originally appeared in the January/February 2016 issue of Food Manufacturing.
In the food industry, maintaining packaging quality and integrity is a top priority. While packaging manufacturers take every precautionary step to ensure that high quality standards are met, it is important for all food processors to prepare for any packaging challenges that might threaten food plant operations and product safety. Issues with packaging seals, leakers, labeling issues, and other packaging hazards present possible concerns that must be quickly and efficiently addressed.
When packaging performance issues occur, it is critical to follow appropriate steps to identify the root cause of the problem, isolate the issue, and develop solutions to safeguard against future packaging issues.
Step One: Identify and Document
Even the smallest issues can greatly impact a food product. Once an issue is identified, food processors must work quickly to isolate the problem and begin the documentation process to properly diagnose the cause of the packaging performance issue.
Photos should be taken as reference through the diagnosis, noting the packaging manufacturer’s lot number and other identifying numbers.
Processors need to note the frequency of the issue, and the number of affected pieces to help determine if it is an isolated incident or something more. This information can also help the processor determine if production can continue running, or if it needs to be temporarily stopped until the issue is resolved.
Step Two: Review the Packaging Equipment
While processors regularly evaluate equipment performance, production line malfunctions can be the cause of packaging issues. A review of the packaging equipment may identify the cause of the packaging problem.
Often, the type of packaging failure will be a clear indication of where the packaging equipment should be checked. For example, higher leaker rates may indicate faulty seal wires, or machine settings that are not set to the correct specifications for that particular packaging.
Another way to evaluate the equipment is for processors to run a new lot from the packaging manufacturer. If the problem is not seen while running the new lot, the issue is likely with the single lot from the packaging manufacturer and not the processor’s equipment.
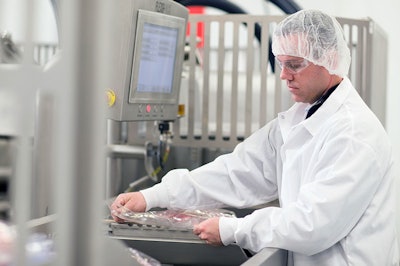
Step Three: Contact Packaging Manufacturer
Whenever a packaging issue arises, it is essential that the processor contact the packaging manufacturer. While the processor is completing its internal review, the packaging company can begin its own investigation. This way, the problem can be resolved as quickly as possible.
As a first step, the packaging company will likely request samples of the affected product be sent back to the packaging manufacturer so the actual product can be reviewed by the packaging quality and production teams. The packaging manufacturer’s quality team will review all production documentation, including any in-plant product retains from that lot. If this evaluation determines that it is likely an issue did occur during manufacturing of the packaging, the packaging manufacturer’s quality team will work with their internal teams to determine the root cause.
As part of this process, the packaging manufacturer’s quality team may send a technical representative to a customer’s location to conduct an in-plant inspection. The purpose of an in-plant inspection is to give the packaging manufacturer an opportunity to identify a pattern in the packaging failures, observe the packaging running on the line to see if they can spot the problem, and inspect the equipment or the equipment settings (like temperature) to help pinpoint the cause. This in-plant inspection can be crucial in narrowing down the root cause quickly and getting the plant back to full production.
Step Four: Pinpoint, Correct, Prevent
Once the root cause is determined, a corrective action plan should be immediately developed to identify the actions needed to prevent the issue from reoccurring. For example, if the cause of the packaging failure is that the product has changed size and the current packaging no longer fits, then the corrective action plan could include working with the packaging manufacturer to identify and recommend an updated food packaging solution. The final step would be to document that this corrective action plan was implemented.
Documentation is valuable for both the processor and packaging manufacturer as a way to ensure the highest quality final product. Diligent reporting helps processors quickly troubleshoot issues by referencing past issues and solutions.
In addition to serving as a learning tool, quality reporting is often mandated by regulatory certification programs. For example, the Safe Quality Food (SQF) certification program, developed by the Food Marketing Institute, requires packaging manufacturers to provide impartial and verifiable proof to retailers and food manufacturers that a rigorous food safety management system is in place. SQF certification is a voluntary process consisting of facility inspections and detailed reviews of record keeping and safety procedures. Achieving SQF Level 3 certification means that a packaging organization has developed a food safety quality-control program.
Quality assurance is an ongoing and evolving process for everyone involved in the packaging of food. With quality issues cropping up nearly every week in the food industry, it is more critical than ever for everyone to have a quality system in place.