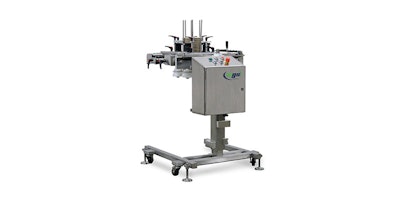
The Vortex separates trays, clamshells, flanged lids, tubs and buckets from a nested stack and accurately places them, ready for filling, on a flighted or flat-belt conveyor at speeds up to 300 per minute. Featuring a single-sided cantilevered design, four-axis stepper motor system and full washdown capability, this cost-effective screw denester offers easy installation, five-minute changeovers and superior sanitation.
The Vortex is ideal for a wide range trays for products that include foods such as bakery products, ready-meals, meat, poultry, seafood and fresh produce as well as cosmetics, pharmaceuticals, medical devices and other products. It handles square, rectangular oval, round and pie-shaped trays, clamshells, lids, tubs and buckets made of plastic, polystyrene, paperboard and molded-fiber, which are 2 by 2 inches (51 by 51 mm) to 12 by 16 inches (304 by 406 mm) in size when the flange is rigid and there is a minimum gap between flanges.
The four-axis stepper motor system offers smooth indexing motion for reliable separation and consistent placement of trays at high speeds. With no belts, gear boxes or other wear parts, the Vortex reduces maintenance while speeding product changeovers. Featuring quick-change timing screws, the Vortex can change from one size and shape to another in less than five minutes with no tools required. The optional screw height adjustable stand further speeds product changeovers as well as installation.
Unlike deneters that straddle the production line, the Vortex’s cantilevered design allows it to be pushed into place over an existing conveyor with virtually no interference to ease installation. Optional locking caster wheels improve mobility within the plant. Short hopper rails enhance ergonomics and push-button controls ease use.
With stainless steel construction and a NEMA 4X / IP68 rated electrical enclosure, the Vortex is designed to withstand high-pressure caustic washdowns to achieve the highest level of sanitation and maintain food safety. This denester is ideal for all food products and wet environments.
The Vortex comes with a standard 30-inch (76-cm) magazine to hold nested stacks. For additional run time, an extended-capacity magazine is available as an option. The extended magazine is modular and comes in various lengths – operators place nested stacks on a powered conveyor, which feeds the denester. An optional low hopper sensor and optional stack light with audible alarm alerts an operator if materials in the magazine are running low.
MGS Machine www.mgsmachine.com
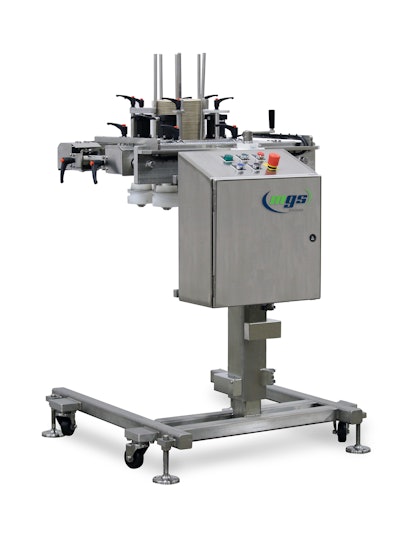