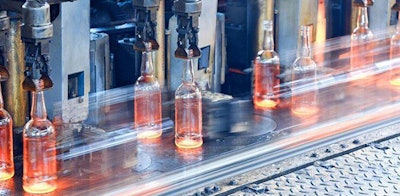
InnovaMass iSeries
240i
INLINE
241i
INSERTION
with Probe Retractor
(easily adjusts
up and down
with standard drill)
5 Harris Court, Building L, Monterey, CA 93940, USA / 800.866.0200 / 831.373.0200 / fax 831.373.4402 / sierrainstruments.com
InnovaMass. Reinvented.
In 1997, Sierra was the first to introduce a combination volumetric vortex and multi-
variable mass flow meter. Today, Sierra’s completely redesigned InnovaMass®
iSeries™ 240i/241i builds on two decades of success measuring five process variables
for gas, liquid and steam with one connection.
Now, with the latest hyper-fast microprocessors, robust software applications, field
diagnostic and adjustment capability, and a new state-of-the-art flow calibration
facility, Sierra’s vortex iSeries delivers precision, performance, and application
flexibility never before possible.
It has Apps!
Experience innovative flow energy management tools driven by our new Raptor II OS
that will empower your process and save you time and money
● FloPro™ vastly improves low flow measurement calculation
● Dial-A-Pipe™ allows you to quickly change pipe sizes in the field
● Dial-A-Fluid™ measures a variety of fluids whenever you choose
● qMix™ makes/measures custom gas mixtures
â—Ź Many more apps to come
Field Independence
With Sierra’s advanced Smart Interface Portal (SIP),
tap into your InnovaMass and bring up a variety of
powerful software interfaces to enhance your
meter’s performance.
● Meter Tuning™ cancels environmental noise,
greatly improving accuracy
● ValidCal™ Diagnostics closely monitors meter
performance and validates output
â—Ź Make fast firmware upgrades in the field
â—Ź Expect a mobile app for your cell phone in 2016
World-Class Flow Calibration Facility
Every flow meter is only as good as its calibration. Each InnovaMass is calibrated by
Sierra’s new calibration facility in Monterey, California, to assure the best possible
performance. Flow standards with accuracies better than 0.2% of reading are used to
assure the highest accuracy possible.
Next Day Shipping
Go to Sierra’s online store to custom configure and buy InnovaMass. We stock select
models for next day shipment. Sierra is the only company in the industry where you
can buy vortex meters factory direct. Visit sierrainstruments.com/shop
Learn More
See the back of this data sheet for technical details or visit sierrainstruments.com
for more information on the Innovamass iSeries.
(InnovaMass specs on back)
Application Tech Notes
Brewery/Bev rage Processes
Mass Flow Controllers Provide Precise Carbon Di xide
(CO2) Injection
In beverage production process, precise mass fl ow control of Carbon Dioxide
(CO2) is a crucial part of creating high quality brews and beverages. It is pivotal
that beverage manufacturers have the ability control the exact amount of carbon
dioxide (CO2) being injected into their beverages during the bottling process.
Mass fl ow controllers (MFCs) are used to regulate and control the amount of
CO2 injected into the bottles during fi lling and capping to assure uniformity of the
product (See Figure 1).
Too much CO2 in the beverage will result in an overly carbonated beverage, and
could possibly break bottles causing a plant safety issue and loss of product.
While an inadequate CO2 injection will cause the beverage to be “fl at”. In either
situation, the batch would need to be tossed out resulting in a loss of product
which costs the company countless dollars in revenue and ultimately hurts profi t
margins.
Many companies use volumetric fl ow and di erential pressure for gas fl ow
control for their CO2 injection process. However, volumetric fl owmeters are not
suitable for this application because of the widely varying mass fl ow requirements
encountered in start-up and low production periods. Direct mass fl ow with thermal
mass fl ow controllers like the MaxTrak 180, part of the SmartTrak family, provides
smooth, stable, accurate, and repeatable CO2 gas mass fl ow control you can rely
on, every time. In essence, counting and controlling every gas molecule fl owing
through the instrument to achieve unmatched precision. Una ected by upstream
gas temperature and pressure fl uctu tions, gas mass fl ow control is direct and
unequivocal.
MaxTrak meets industrial MFC requirem nts with NEMA 6 & IP7 ratings and
provides the robust, smooth mass fl ow control required for the brew and b verage
process industry.
Figure 2: MaxTrak™ 180 Mass Flow Controller
for CO2 injection for beverage industry
• High accuracy: +/- 0.5% of reading
• Accuracy: +/- 1% of reading
• Repeatability: +/- 0.2% of full scale
• Meet industrial MFC requirements with
NEMA 6 & IP67 ratings
• Increase effi ciency with true, digital
high-performance
• Make adjustments in the fi eld for time
savings
• Confi gure up to 10 gasses with one
instrument
Learn More at:
sierrainstruments.com/co2injection
Figure 1: CO
2
Injection for Beverage Industry