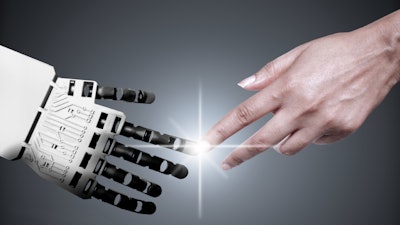
As technology has continued to evolve with each newer and better iteration of automation, many fear less available jobs on the market. On top of that, COVID-19 has disrupted supply chains worldwide. Manufacturers remain mired in increased orders, customer inquiries, shipping delays and remote workforce dynamics.
To overcome these challenges, business leaders continue to search for innovative solutions to keep their operations moving. And, for supply chains, the message is clear: itβs time to automate.
While automation has brought more robots and technology into supply chains, it hasnβt caused the elimination of jobs that many expected. Rather, employees still need to be present to ensure the equipment still runs properly. The introduction of collaborative robots, or cobots, has meant that robots supplement someoneβs job rather than replace them, and employees have been re-trained to complete more skilled labor that machines canβt do.
People Remain the Driving Force
As the old saying goes, βWhatever can go wrong, will go wrong.β That is to say that machines can, and will, breakdown at some point. Automation might be moving employees off the assembly line, but they will still be needed to oversee the equipment, perform safety and quality checks, ensure operations are running smoothly and, most importantly, fix the machines when they break.
Ensuring machine uptime is a vital piece of every manufacturersβ operation. If one part of the assembly line isnβt working right, the downtime for a manufacturer could result in the loss of production, raw materials and time on other tasks - resulting in lost revenue. Plant managers, equipment operators and safety engineers are still needed to perform regular quality and control checks on automated equipment, ensuring equipment operates efficiently and safely.
Robotics in manufacturing has been shaping how plants operate for years now, and cobots have been on the rise due to their flexibility in being adapted for different jobs. Rather than removing people from the assembly line altogether, cobots and line workers work hand-in-hand, making the production process shorter, increasing productivity, reducing the defect rate and boosting employee efficiency.
Besides making the job of employers easier, cobots also benefit companies in other ways. Their ease of deployment and ability to learn tasks on the go, often coming with these out-of-the-box capabilities, enable companies to see ROI quicker. Additionally, cobots can be reprogrammed to complete different jobs relatively easily, enabling manufacturers to deploy them for multiple processes. When a manufacturer can improve the lives of their employees while also reducing the number of tools needed in the plant, itβs a win-win for both sides.
Upskilling Provides More Opportunities
As technology becomes more advanced and the search for increased efficiencies and more output continues, companies will continue to explore digital transformation and automated manufacturing processes as a means to get ahead. People working in manufacturing long thought this meant that more people would be out of jobs. And while, yes, it is true that more people are being moved off the assembly line, there remains a need for employees in other areas of the plant for jobs that automated machinery simply cannot do.
Beyond purely technical skills, companies will increasingly need people who possess complex problem-solving, critical thinking and creativity skills that are needed to analyze facility operations and find solutions that continue to increase efficiencies. An example of upskilling would be training workers who have an aptitude for data and analytics to work in the sales department as industry forecasters or as supply chain managers. This upskilling enables them to contribute to increasingly mission-critical tasks such as predicting when more supplies will be needed or when there might be disruptions that can hurt the bottom line.
With the added restrictions on social distancing and number of people who can be in a workplace due to COVID-19, automation was the only path for some businesses to survive. By speeding up plans to further automate plants, many companies have set themselves up for long-term success.
Not only does automation improve efficiencies, limit mistakes and increase worker safety, but when you upskill employees, companies can fill positions with people who already know their business and are invested in it rather than looking for outside replacements. And while there will be costs associated with training employees for different jobs, companies are saving themselves on time and money by not having to recruit, go through the hiring process, and the longer training process when onboarding new employees from outside the company.
Upskilling internal employees also shows workers that the company is committed to their long-term growth and success. Overall, internal investments foster a more positive work environment. Furthermore, by investing in automated processes and upskilling employees during the pandemic when the supply chain was slowed down, companies were able to better position themselves as things ramp back up.
Brandon Bach is the president of CCT.