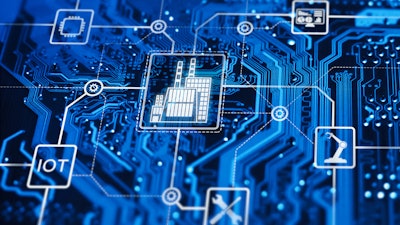
A majority of manufacturers – 68 percent – are planning to increase their investments in digital transformation and smart factory initiatives over the next few years. That ratio will undoubtedly increase as existing digital transformation projects scale up and new cutting-edge enterprise technology solutions emerge. To ensure the best business outcomes, it is important manufacturers move beyond traditional siloed data approaches with a digital thread strategy.
For manufacturers, data siloes typically build up in systems used for day-to-day planning and operations, including enterprise resource planning (ERP), electronic manufacturing services (EMS), manufacturing execution systems (MES), manufacturing operations management (MOM), or other software systems and tools.
When these systems are not integrated, manufacturers may miss critical insights that could improve factory operations. Further, end-to-end visibility provided by integrated systems enables trend spotting, which is the capability that provides the highest ROI from digital transformation initiatives.
Manufacturers pursuing new (or scaling existing) digital transformation projects may want to take a step back and ensure they include digital thread in their approach. They should ask themselves:
- What do they see as their organization’s full digital potential?
- What are the benefits and competitive advantages that their organization ultimately hopes to gain from digitization?
- Perhaps product design would like to collaborate with their OEM in real time.
- Maybe the product engineering team wants to increase line configurability.
- Does the plant operations manager feel pressured to meet OEE goals?
- Is the supply chain team desperate for future supply chain insights to anticipate needs ahead of time?
Tying Enterprises Together
Digital thread is a strategic framework that optimizes the lifecycle of a product, asset, system, or process by connecting critical business functions. Connecting ERP, EMS, MES, and MOM systems via a digital thread allows information to flow between systems to inform and optimize business-driving processes ranging from design, to supply chain, to production.
This approach provides the entire value chain with access to unified digital data captured during design, virtual simulation, and physical operations. A holistic digital strategy, powered by digital thread, helps manufacturers move faster by removing friction between disparate teams and systems.
Think of a digital thread as a record of the evolution of your manufacturing operations. From physical machines, to manufacturing processes, to automation code and maintenance steps, digital thread provides visibility into their past, present, and future states. This increased visibility into the evolution lifecycle helps to prevent digital transformation disruptions and upsets – ultimately enabling accelerated innovation, maximized workforce productivity, and optimized operations.
Accelerated innovation, maximized workforce productivity, optimized operations – all sound great. But how exactly does a simple record of operational evolution enable these competitive benefits?
- Digital thread enables accelerated innovation through real-time collaboration. Manufacturers no longer need to email design files across their organization, accepting that there will inevitably be version control issues. Machine builder engineers, who are designing the machine, and field engineers on site establish a single source of truth by exchanging information in real-time.
- Digital thread can be used to commission new production lines virtually – enabling manufacturers to decrease time to market and protect investments. Rather than waiting to commission manufacturing lines until the machinery is bolted to the plant floor, manufacturers can ensure that operations will run smoothly by validating manufacturing processes and debugging PLC code via a digital twin.
- Digital thread maximizes the potential productivity of the manufacturing workforce by equipping employees with the tools they need. From veterans to new hires, digital thread connects business systems together to enable the creation of a historical record of all trainings and on-the-job instructions needed to keep production running smoothly. Virtual reality and augmented reality can shorten training time by as much as 75 percent by enabling low-risk, high-fidelity environment training and real-time equipment instruction for new or retrained employees.
All of this information regarding machine performance, employee training, and real-time collaboration are stored within the digital thread – maintaining the context of data and enabling rapid operations insights to bring manufacturers to peak performance in record time. This contextualization of information drastically reduces: the time and effort needed to integrate production lines into existing business processes, the time to develop high-value software applications, and the risk associated with changes to the production line.
Manufacturers seeking to realize their full digital potential and reap highest ROI when it comes to digital transformation must futureproof their digitization investments and re-think the way they manage operations by leveraging digital thread. In the end, this will enable manufacturers to monitor operations and apply learnings from their production lines safer and faster than ever before.
Keith Higgins is Vice President of Digital Transformation at Rockwell Automation.