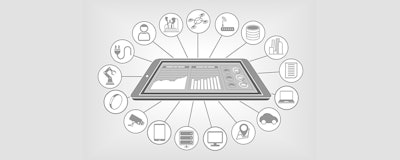
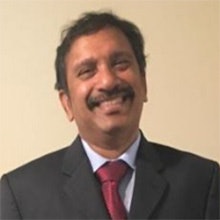
By now, we’ve all realized the reality of today’s internet-connected world: Smart devices aren’t just in our pockets and in our homes. The Industrial Internet of Things (IIoT) is revolutionizing the food and beverage industry.
We’re seeing more connected sensors, motors and controllers on the plant floor than ever before, and they’re being used in innovative new ways to optimize processing and inform operations decisions.
There are four main areas of a food plant where IIoT technology is having a major impact:
- Food safety
- Product quality
- Packaging
- Personnel
Let’s look at how internet-connected tools are influencing these aspects of food manufacturing and how they could benefit your facility.
1. Food Safety
At a time when food product recalls aren’t exactly slowing down, preventing recalls is crucial for the health of your consumer, your reputation and your bottom line. Today’s IIoT technology can nip food recalls in the bud by preventing bad product from even leaving the facility in the first place. This can be done simply if your system is set up correctly with the right sensors and data collection points.
Let’s say your facility is producing sauce, and that sauce needs to be heated to 192 degrees for five minutes to ensure that all HACCP and regulatory requirements are met. In the past, if a batch is only cooked for four minutes, you may not realize you have a bad batch until it is packaged because of how long it would take for a manual report to be delivered to the quality control department.
However, internet-connected sensors can now measure those time and temperature set points in real time and immediately send a notification if they are not met. Now that bad batch can be disposed of right away, saving time and money while reducing the risk of that product leaving the facility. Thanks to real-time IIoT technology, potential food safety issues can be detected quickly and dealt with internally before getting to the point of a recall.
2. Product Quality
A well-connected plant also benefits production by improving consistency and accuracy in product quality. Today, product recipes and procedures can be stored on a single server and pushed to all of a company’s processing facilities, ensuring product consistency regardless of where the product is produced.
Companies can also send quality benchmarks and metrics, such as cook time and temperature, to internet-connected equipment. The machine knows, based on its programmed instructions, to run a certain recipe at a certain time by adding certain ingredients and then processing in a certain way. All the steps are built in and come from a single, controlled source.
Rather than inconsistencies that would otherwise occur if an operator at one facility decides to tweak a recipe or cut a corner, a plant utilizing IIoT technology can be monitored and controlled remotely, improving recipe accuracy and product consistency across the board.
3. Packaging
When it comes to packaging, changeovers and downtime are the biggest factors today. Of course, the goal is always to maximize revenue by running the most amount of product with the least amount of assets as quickly as possible. A well-connected plant can help achieve this goal by making packaging more efficient.
Sensors on packaging equipment can be programmed to understand what SKUs to expect from the processing side at a given time. The sensors can then verify that the correct packaging is being used for various products and immediately halt the process if there is a discrepancy. Traditionally, if an operator ran the wrong product in the wrong packaging film, it may not be detected until much later, resulting in wasted product and packaging that has to be thrown away. Today, these discrepancies can be virtually eliminated by catching packaging mistakes in real time.
In an IIoT-based plant, labeling parameters are downloaded from a server as well. Instead of an operator manually typing in the date, time stamp and plant code, that information can be pushed directly to internet-connected equipment. This reduces operator error on the plant floor and operators can focus on verifying that the computer is running the labeling correctly.
4. Personnel
Contrary to what some might assume, IIoT technology is actually making plant personnel more connected to their work, not squeezing them out. Thanks to the unprecedented access to data provided by sensors and software, employees understand their facility’s processing more than ever before.
Today’s facilities can actually “talk back” to employees and notify them when something is wrong, enabling plant personnel to do their jobs better. At the end of the day, employees are still needed to change film, perform certain aspects of the processing and conduct maintenance. IIoT technology just makes communication between plant personnel and equipment a two-way street.
Example: IIoT in a Real-World Plant
Stellar is currently working on an expansion of a plant, and we are installing a fully integrated network where all equipment in the facility is connected to the Internet. WiFi repeaters have also been specified throughout the facility, allowing personnel to access information via tablets at any given time.
The facility has an overarching manufacturing execution system (MES) that sends recipes to equipment and receives feedback from the equipment in real time to verify that the right SKUs are running at the right time. This is especially critical at this plant because they are running various SKUs throughout the day and each SKU has various packaging formats.
Not only does internet connectivity allow the processing to run faster, but the MES allows for open communication so that the company’s headquarters can see what is happening in the plant in real time from three time zones away. There’s no delay in waiting on reports from the plant. The company’s top leaders know exactly what’s being produced minute by minute and can make decisions instantly based on this data.
The Future of Internet-Connected Food Plants
IIoT technology has empowered food processing facilities with unprecedented access to real-time data, but many food manufacturers are still learning about these capabilities and what they can do with all of this new data. Stellar often advises clients on what is possible and how to best harness that data to meet their goals. For example, these sensors can be used to send push notifications to mobile devices, thresholds can be set to alert quality control when extra verification is needed, and the data can be aggregated over time so that companies can analyze long-term trends.
Several of the clients we’ve worked with have committed to going “full steam ahead” when it comes to IIoT technology. They’ve installed WiFi repeaters across the plant, are utilizing sensors across all of their processing, and are using smartphones and tablets to receive alerts and operate the plant. Meanwhile, others are taking a phased approach. They may have a few tablets to provide maintenances with drawings and equipment history, but they haven’t committed to full-scale connectivity across all of the plant’s operations.
The adoption of IIoT technology is starting, but there is still a long way to go before it is ubiquitous. There is a lot of potential for how this technology will impact the food manufacturing industry, but widespread adoption will take time.
About Stellar
Stellar is a fully integrated firm focused on planning, design, pre-construction, construction, refrigeration, mechanical & utility, building envelope, and total operations & maintenance services worldwide. Visit the company's blog at www.stellarfoodforthought.net or learn about its projects at stellar.net