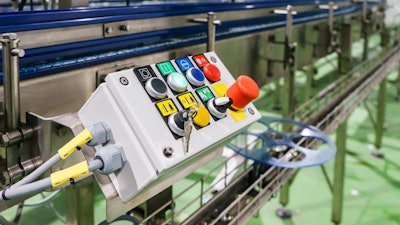
While conveyer belts are integral facets of the distribution process and most warehouses could not function without them, they also pose the potential to cause serious injuries and sometimes even fatalities. In fact, the U.S. Department of Labor, Bureau of Labor Statistics has reported that over 40 workplace fatalities a year are the result of conveyor accidents, along with 9,000 injuries.
While in motion, conveyor systems have inherent and obvious dangers. Belts continuously move at speeds up to 600 feet per minute or 10 feet per second. There are many pinch-points within their machinery, any of which could cause an injury to a worker. Common employee injuries incurred working with conveyors include arm and hand amputations, finger lacerations, burns, scrapes and broken bones. Even when employees are being careful, accidents can happen. It's easy for loose clothing, jewelry or hair to get trapped in conveyor belts and, if workers aren't paying attention, they could get caught in the machine.
Every conveyor belt injury in a warehouse is costly, affecting worker morale, availability of trained labor, lost production, and increased overhead due to insurance premiums, along with mountains of paperwork, lawsuits and possible fines from government regulatory agencies. Conveyor belt injuries account for nearly 25% of all workers’ compensation claims. Safeguarding conveyors protects employees from injuries, and companies from potential financial ruin.
Safeguarding Conveyors
ASME B20.1-2018 applies to the design, construction, installation, maintenance, inspection, and operation of conveyors and conveying systems in relation to hazards. The conveyors covered can be bulk material, package, or unit-handling types installed for permanent, temporary, or portable operation. OSHA has also issued its own standard 1926.555(s)(1), General Conveyor Safety Requirements. In many cases, local municipalities and equipment manufacturers will require standards above and beyond ASME and OSHA be met.
Because conveyor designs vary, each conveyor should be evaluated to determine what primary safeguarding methods and energy control practices are required. For instance, a chain conveyor introduces the hazards of nip points when a chain contacts a sprocket. As a result, the primary safeguarding method would be enclosing the moving chains. If this isn’t possible, barrier guards can be installed around moving points so that nip and shear points can be eliminated by a guard. Secondary guarding options would include safeguarding by distance or the use of awareness devices.
Rather than concentrate on specific details of unique conveyor designs, for the purpose of this article, we are going to look only at three basic requirements of conveyor safeguarding: emergency stops, guards and motor starters.
Emergency Stops: The only conveyors that don’t require emergency stops or “e-stops” are ones mounted more than eight feet above the working surface, since those are guarded by their elevation, a situation called “guarded by location.” Conveyors that are accessible to operators must be equipped with e-stops.
According to both ASME B20.1-2018, remotely and automatically controlled conveyors where operator stations are not manned or beyond contact shall be furnished with emergency stop buttons, pull cords, limit switches or similar emergency stop devices. As a general rule of thumb an operator should be able to stop any conveyor within his or her line of sight by activating the nearest emergency stop. ASME also requires that all emergency stop circuits should fail in the event of a power loss to the emergency stop circuit. Employees must be familiar with the location and function of e-stops to allow them to make fast decisions on using them. E-stop training should be provided to all employees regarding where they are located, when to use them, and how to access them.
As for restart, OSHA requires that “emergency stop switches shall be arranged so that the conveyor cannot be started again until the actuating stop switch has been reset to running or ‘on’ position.” ASME goes further, requiring that the starting device be locked out or tagged before any attempt is made to remove the cause of the stoppage. Besides having the activated emergency stop switch or pull cord reset, an audible warning signal must be sounded immediately before starting up the conveyor.
Depending upon the size of the conveyor, multiple start buttons may need to be activated. Modern conveyors may feature a Human Machine Interface (HMI) that allows operators to remotely identify the location of the tripped emergency stop on a display. Once the local emergency stop has been reset, the system can be remotely restarted via the HMI.
Finally, e-stops should never be modified for any reason by unqualified personnel. Monitor e-stops to ensure employees have not misused, modified, or disconnected them.
Guards: ASME B20.1-2018 requires conveyor with accessible nip points on spools and pulleys be guarded to prevent contact by a worker, and that a conveyor have guards or sideboards to prevent material from falling from the conveyor into areas occupied by workers if the falling material presents a hazard of impact injury or burn. Barriers, enclosures, grating, fences, or other obstructions that prevent physical contact with conveyor components are considered to be guards. When the guard is used as the primary safeguarding method, a guard opening scale can be used to ensure no employee cannot reach under, over, around, or through the guard. Any openings created by the guards must be checked for compliance with ANSI/CSA safety standards. Hand railing is not acceptable to limit access to a pinch point as it can be breached easily.
Most serious accidents and fatalities involving conveyors result from inadequate guarding. Guards are sometimes removed by plant employees for maintenance purposes, or because they obstruct an employee’s access doing work, exposing sharp machinery, gears, chains, and moving parts that are extremely dangerous. To help ensure worker safety, lock out conveyors when in service, and operate equipment only when all approved covers and guards have been reinstalled.
Whenever a conveyor is under repair or maintenance, it must be stopped with power sources locked out and tagged out. Exceptions may be given to conveyors that need power for testing or making minor adjustments. For more about “alternative LOTO measures” consult ANSI/ASSE Z244.1 for expanded guidance beyond OSHA’s regulatory limitation to tasks that are “routine, repetitive and integral to production operations”. Following the Hierarchy of Control model, ANSI/ASSE Z244.1 provides detailed guidance on if, when, and how a range of alternative control methods can be applied to result in equal or improved protection for people performing specific tasks.
When it comes to conveyor service, maintenance work should only be carried out by fully trained, highly qualified professionals. These professionals will ensure proper lockout/tagout procedures are followed, and to block or disengage all power sources to the conveyor — electrical, hydraulic, air and gravity. Keep in mind that even the best trained technicians are occasionally injured by a conveyor. Untrained staff should never attempt a conveyor system repair.
Final Thoughts
As with any industrial equipment, conveyors are capable of causing grave injuries if not safeguarded according to established standards. However, it is equally important that employees working around conveyor systems are trained regarding potential hazards. Constant vigilance and a safeguarded conveyor are vital to keeping your warehouse and facility safe.