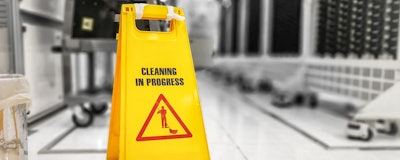

With increased pressure to keep production up, reduce costs and avoid dangerous and costly recalls, food and beverage facilities have turned to bundling contract labor with plant sanitation chemicals as a way to solve these challenges. However, there are major risks to bundling these services that many are not aware of.
Moody’s Analytics Chief Economist Mark Zandi in July 2018 told CNBC, “Business’ number one problem is finding qualified workers.” This is an issue clouding the minds of many food and beverage manufacturers. So, when a company comes along amid the labor shortage and offers a solution like bundling food safety labor and chemicals, it seems too good to be true. And, it usually is.
The idea of bundled pricing for services and products isn’t a foreign concept. For example, cell phone companies have offered bundled pricing for years. Users pay one monthly fee for a variety of products and services: a phone loan, a data package, minutes for phone calls and texting.
Unfortunately, through its history, this marketing concept rarely benefits the consumer as it promises to.
Anthony Tjan, CEO and manager partner and founder of the venture capital firm Cue Ball, wrote an article earlier this decade about the concept of bundling in the Harvard Business Review. Tjan notes, “When a seller unbundles options, it opens up the transaction negotiation to line-by-line scrutiny.”
Bundling services and products, like contract labor and sanitation chemicals, removes the transparency that processors need to ensure they’re getting what they’ve paid for and that their plant is being cleaned properly and safely.
Here are three ways food and beverage processors can responsibly outsource sanitation without sacrificing Food Safety Modernization Act (FSMA) compliance practices or losing transparency.
1. Separate Contract Labor And Sanitation Chemicals
Outsourcing sanitation labor may be the best option for a food processing facility, especially since in many cases these positions are overnight shifts and can involve hard labor. If you must outsource labor, do not make the mistake of bundling it with sanitation chemicals.
With full labor contract transparency, you can ensure you’re getting what you’ve paid for. Ask for a full technical background of the employees, monitor the number of workers clocking in and out each night and, if you can, have one of your own food safety experts monitor their performance.
Unbundling labor and sanitation, or not bundling to begin with, will also paint a clearer picture of sanitation chemical usage: How much chemistry is your facility using? And how much does it actually need to ensure food safety?
When you bundle, your facility is paying for a set amount of chemicals each month, whether you actually use those chemicals or not. You’re also in the dark when it comes to which chemicals are being used where. For example, some areas of a plant require a specific blend of chemicals to be properly cleaned, and crews may not be following that directive.
2. Automate Tedious Tasks
Before deciding to hire labor crews, take a step back and evaluate the tasks that need to be completed. There are many plant sanitation duties that require repetitive actions and little thought. A crewmember may need to stand over a piece of equipment and spray chemicals back and forth for hours on end.
Not only does monotonous work potentially waste water and chemicals, it can also cause a worker to get fatigued and unfocused, leading to human error. This puts your plant at risk for accidents and injuries, as well as inadequate cleaning.
Instead of outsourcing labor for these particular tasks, consider sanitation automation. Automating tedious work will remove human error and provide peace of mind that your facility is being cleaned properly. In addition, while every situation can vary, processors can experience up to 50 percent water reduction and 30 percent reduction in chemical costs when automating these processes.
A clear understanding of the jobs that need boots on the ground will allow you to hire the right size crew for the right tasks while minimizing the risk of poor sanitation and wasted resources.
3. Implement Reporting Automation
Trusting an outside labor company with your facility’s sanitation can be difficult, especially considering the costs of a food safety recall — both indirect and direct — as well as the long-term financial and environmental effects of excess chemical and water usage.
Choosing to unbundle contract labor with sanitation chemistry is the first step in taking control. Second, is implementing reporting automation software.
Reporting automation software allows processors to keep track of the resources outsourced crews are utilizing. Not only will this knowledge help eliminate waste, it will ensure that enough chemicals are being used to effectively sanitize the plant.
FSMA regulations also require access to documented sanitation data, which automated reporting technology provides. If your plant is audited for FSMA compliance, having this data at hand is key for a successful inspection.
Follow A Responsible Outsourcing Model
Anything but absolute transparency when it comes to plant sanitation puts your brand’s reputation at risk. A recall not only causes a devastating financial burden, it can lead to litigation, a decline in stock value or government fines.
While employing an in-house sanitation crew is the ideal scenario, that’s not always a viable solution. Outsourcing sanitation labor in a way that mitigates food safety risks is possible with the right amount of communication and collaboration between all parties.
Bundling contract labor with sanitation chemicals puts the power into the hands of the labor company and leaves you in the dark. Are you willing to put your brand’s reputation at risk?
Dave Premo is Vice President of Business Development at Birko.