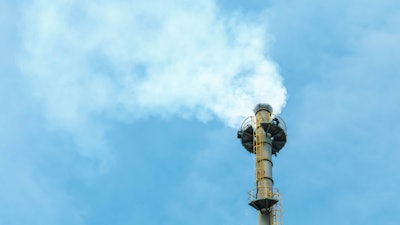
Make no mistake, the target is aggressive.
The food industry is an integral component of the U.S. economy, making up between 10.5 percent and 19 percent of nation’s annual energy consumption. From a global perspective, food processing alone accounts for an estimated 4.4 percent of total greenhouse gas emissions. And, demand is rising fast, leaving food manufacturers with a seemingly impossible task of reaching net-zero emissions without reducing their production capacity.
One identifiable reason the food industry is among the highest contributors of greenhouse gas emissions is that many factories in production today were built more than 50 years ago. Over time, these buildings have been mostly retrofitted rather than updated with the latest technology. In addition, safe food production requires energy 24/7 for heating and cooling for a variety of reasons, including sterilization and cold storage. And simply looking to renewable energy sources may not be the answer, at least not yet.
The cost of renewable electricity is still high and not a viable solution if food manufacturers must act now to meet their sustainability goals. An entire industry switch to electric would overburden the current energy supply and grid infrastructure and drive costs even further in the wrong direction.
Electricity generation from solar and wind is intermittent, hard to store and relies on the development of hydrogen for storage and usage — through combustion or conversion back to electricity, using fuel cells. And while biomass, an agriculture byproduct, seems like a logical solution for the food industry, these feedstocks are not commodities, and access to biomass energy depends on factories having the byproduct onsite or nearby.
Furthermore, biofuels are in growing demand in transportation and other parts of the economy, resulting in higher prices. Therefore, there is no likelihood of having all of these green resources available to the industry and to simply continue business as is, hoping that the future will be green. Perhaps the best way to address these issues head on is to identify and reduce waste heat and optimize efficiencies within a plant’s current processes.
Another Approach
As the CEO of Armstrong International, a leading thermal utilities solution provider, I see an opportunity that is uniquely fitted for food manufacturers. In our more than a century of experience, we have compiled massive amounts of data that reveal food manufacturers are well-positioned to decarbonize their facilities without hindering their ability to serve the nation’s growing food demand.
We ran a detailed assessment of the energy profile of hundreds of global food processing sites, revealing more than 60 percent of total energy consumption is committed to thermal utilities (heating and cooling). Furthermore, detailed field site assessments of food industry thermal utilities identify a massive opportunity for energy savings.
In fact, plants can achieve up to 80 percent total carbon reduction from implementing an internal process heat exchanger network and industrial high-temperature heat pumps to recover waste heat and displace fossil-generated heat in a “Circular Thermal” strategy. This consists of a three-step process that includes de-steaming (conversion to pressurized hot water) all applications below 250°F; recovering direct heat when a positive differential temperature is available; and using industrial heat pumps for raising the temperature of low-grade heat to the temperature that is useful for the process.
Unlike other sectors, such as heavy industry, food plants produce a significant amount of waste heat from cooling and process while simultaneously needing heat at relatively low temperatures (below 250 degrees Fahrenheit). This combination makes the food industry a perfect candidate to optimize energy efficiency by capturing its wasted heat and using it as a replacement for purchased fuel. This is a very viable “Circular Thermal” strategy available to nearly all food processors.
Mapping the thermal energy lifecycle within a plant can provide direct visibility into the efficiency and productivity of its energy consumption, especially with the availability of today’s AI- and IoT-powered technologies that can remotely monitor performance and flag any telltale sign of failure. This approach provides critical information on energy consumption levels of various production facilities, allowing management to make better, real-time automated decisions that reduce overall energy usage.
Thermal mapping also informs experienced engineers as they model the plant’s thermal energy process through what is called a pinch point analysis, or a methodology for analyzing heat flow to define the best theoretical thermal integration for a more efficient process.
The Potential Impact
Incredibly, manufacturers could knock off more than 50 percent of their primary energy demand just by applying “Circular Thermal”. The remaining heat generation is electrified (through heat pumps compressors), thus making it possible to benefit from existing renewable power purchase agreements. This minimizes the capital investment needed to complete the net-zero journey without significant increase in operational expenses, while improving productivity and the quality of work-life for machine operators. “Circular Thermal” could also improve workplace safety by addressing the organic expansion risks plaguing the infrastructure, enabling confident dialogue with stakeholders, and helping to make the planet better.
Optimizing a plant’s energy efficiency not only is an important step towards reaching net-zero emissions for manufacturers, but also a vital part of protecting the world’s energy resources. Contrary to misconceptions, when done correctly, decarbonization improves efficiency and reduces production costs with an added benefit of being good for employees and the planet.
Even if companies could afford the outright switch to renewables without considering optimization, and bite the increase in operating expenses, half of that energy will still be wasted as waste heat—resulting in wasted renewable energy that the rest of the society will need.
So, the question is not whether we can hope for a renewable silver bullet solution. That’s off the table. It’s up to the industry leaders of this generation to work within our current means to improve efficiency, optimize our facilities and eventually decarbonize our world.
Douglas Bloss is President & CEO of Armstrong International and a member of Armstrong’s Board of Directors.