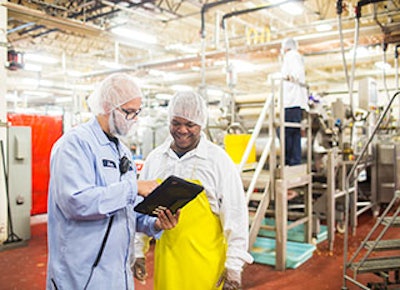
Editor's note: This article originally appeared in the November/December 2015 issue of Food Manufacturing
The food industry has made great strides in food and workplace safety over the past several years through capital investments and process improvements. Getting to the next level of safety requires a better understanding of frontline worker attitudes and behaviors and adjusting the training and communications to create a sustainable safety culture.
Recently, the Center for Research and Public Policy conducted a survey of more than 1,200 frontline workers and supervisors, spanning the entire food production cycle – from farm to fork. The Mind of the Food Worker study was sponsored by Alchemy Systems, which works with leading food companies to build safety cultures.
The study reported that 93 percent of workers would stop work if they found a food or work safety issue. Only 7 percent of food workers were uncomfortable stopping work when they spotted unsafe food or work conditions. While this is not a high percentage, when applied to the 20 million workers at food companies, restaurants and grocery stores in North America, there are still a lot of frontline workers who are simply not clear on what actions to take in case of a safety risk.
The study also indicates that 24 percent of workers surveyed reported that they had been injured at work; 17 percent within the first year on the job. Almost 21% of workers said they received too little job safety training.
Improving Safety Training and Coaching
Onboarding training is the first time that new employees are exposed to the company’s safety cultures and practices. Provide too much detail and information, and the employees will be drinking from the proverbial “fire hose” and will have limited recollection. Provide too little, and new employees will be unsure how to identify and react to safety conditions or risks.
The onboarding and ongoing training also needs to strike the right balance between sufficient depth and simplicity. According to the survey, 39 percent of workers and 43 percent of supervisors said “training is sometimes too complex or difficult to understand.”
The onboarding training is simply not sufficient to keep safety issues “top of mind” with frontline workers. The research indicates that safety messaging needs to be metered out in absorbable, bite-sized chunks using multiple vehicles like digital signage and short-burst e-learning.
The good news is that both younger and older workers are more and more comfortable with using digital devices at home and work. The study indicates that food worker usage/ownership of devices as follows:
- 74% have or use a laptop
- 69% have or use a computer
- 51% have or use a tablet
- 67% have or use a smartphone
These usage rates are only 10-15% lower than the general population. The surprisingly higher than expected technology adoption enables companies to introduce new ways to train and coach the frontline. Tablets have been especially helpful due to their portability and affordability. Tablets also enable supervisors to observe and document worker safety behaviors and provide on-the-floor reinforcement training and coaching if needed.
Attention spans have been shrinking for the past decade. To reinforce safety training in light of shrinking attention spans, leading companies are using short-burst messages using digital and printed signage that really stand out. The content is rotated regularly so that it is always fresh and grabs the viewer’s attention.
Another important way to communicate safety messages is through structured and consistent shift level discussions between supervisors and the shift workers. These huddles can be greatly enhanced when the supervisors – who may not all be great communicators – have pre-built visual guides to communicate and lead discussions on safety topics like lockout/tagout.
Smart companies are leveraging new technologies and learning advances to rethink their training and coaching programs. They recognize the power of incorporating frontline workers in building a safety culture.