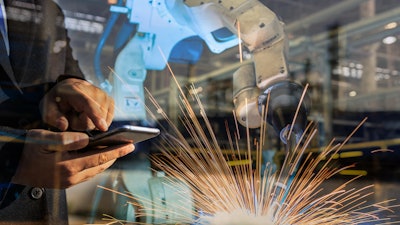
In considering a transition to a Model Based Enterprise (MBE), today’s manufacturers must make strides to achieve digital continuity within their build process. The more complex the assembly, the greater degree of information and continuity is needed to meet standards and retain efficiency at the beginning and throughout the changes that may occur during a build cycle.
Consider an engine casing held together by 72 identical bolts. During assembly, it is determined that two bolts must be changed. To ensure quality it may not be enough to simply add two new parts to the process. Instead, the manufacturer will need to know exactly which bolts, where in the instruction they were installed, see where in the process current work-in-progress models are, and more.
This is the core obstacle to overcome in pursuing a Model Based Enterprise. When developing a path forward a manufacturer must first understand the goals of the Model Based Enterprise, the importance of the Cyber Asset in achieving those goals, and what currently prevents them from achieving the continuity needed to establish the foundation of the MBE itself.
The Goals of the Model Based Enterprise
MBE offers an opportunity for a high return on investment, and one that delivers tangible change on the shop floor. That said, today’s complex manufacturers often make the mistake in believing that by simply designing models in leading edge CAD programs that they are well-suited to transition to an MBE. Instead, manufactures should consider the following goals as a benchmark in developing a Model Based Enterprise:
- Quality: Manufacturers should have access to the information that builds to the expected and necessary quality, and does so the first time. To do so they must incorporate Product Manufacturing Information (PMI) such as tolerance, features, inspection criteria, etc. and integrate this information throughout the process.
- Velocity: During a normal manufacturing cycle our current customer base may oversee idle time reaching upwards of 95 percent. Manufacturers should digitally integrate process planning, execution, and quality control in a single digital layer to rapidly decrease this idle time.
- Efficiency: Manual efforts are currently needed to overcome changes and challenges mid-build. Digital continuity can help to minimize those efforts and allow manufacturers to do only what needs to be done.
At the root of these goals sits the Cyber Asset, an essential part in today’s Model Based Enterprise and an asset that will only become more important in the next generation of manufacturing. Before understanding the importance of the Cyber Asset, we must first define it as part of the manufacturing process.
Defining the Cyber Asset
The Cyber Asset can perhaps be best understood in comparison to another similar term: the Digital Twin. While the definition of the Digital Twin has changed over time, we have come to understand it as an exact virtual copy of an object, product, piece of equipment, person, process, supply chain, or even a complete business ecosystem. This may include model data, PMI data, visuals, sequences, etc.
In contrast, the Cyber Asset defines everything that was built and how it was built. This will include every failure, every repair, every waiver, every component replacement, and so on. The cyber asset is both an asset for the manufacturer, but also a deliverable to the purchaser.
The Cyber Asset is made of two essential parts: The Item and the CAD ID. The Item connects the unique item key of a part, and that part’s PMI. In a cyber asset this data is stored throughout the process and records the changes a part undergoes during the build. The CAD ID defines how each part in a bill of material will go together and what role a part plays during assembly. When an engineering change is made to a part, the CAD ID will define what was once there in the complete assembly and how it was changed.
The Cyber Asset is integral to the value of the manufacturer and is also important post-production to the recipient of the product. With a cyber asset the manufacturer will have access to the information they need in real time, creating a more seamless transition throughout the build cycle. By integrating changes and revisions through CAD ID, the manufacturer can increase velocity by being able to react agilely to necessary changes, and efficiency by reducing the number of manual tasks necessary to revise and complete assembly.
We are likely to see more and more industries come to expect the Cyber Asset as a deliverable product alongside the product itself. With this trend continuing, the Cyber Asset may become an essential part, not just for the Model Based Enterprise, but for manufacturing overall.
What's the Hold Up?
We estimate that today’s complex manufacturing enterprises spend three percent of their company’s revenue on manually mending systems due to a lack of digital continuity. With this amount of revenue sitting out there, why are manufacturers missing out on the opportunity digital continuity can provide?
One reason is that today’s manufacturers are mistaking this waste as a “cost of doing business.” Manufacturers have instituted procedures in their build cycle and quantify those procedures as necessary costs, as opposed to waste to be overcome.
For instance, one obstacle we often see comes during day-to-day design changes. It is common procedure when a functional/interoperability change is made that the manufacturer will manually make the change through copy and paste, and then roll the part number in for the affected parts. This manual change contributes to the wasted time instead of being handled seamlessly as it would be in an MBE. More importantly, the manual copy and paste removes the critical PMI and CAD ID information to the impacted parts, and in doing so, eliminates the possibility of maintaining the digital continuity needed for an MBE.
To implement an MBE and achieve the returns that come with it, the manufacturer must take a finer look at the true costs associated with their current manual processes, and what roadblocks they are causing for digital continuity. They must then phase out legacy procedures from their build cycle. Finally, by replacing these procedures with ones that better align with the goals of the MBE they can reap the rewards of digital continuity.
Michel Gadbois is the Senior VP & Chief Enterprise Architect at iBase-t.