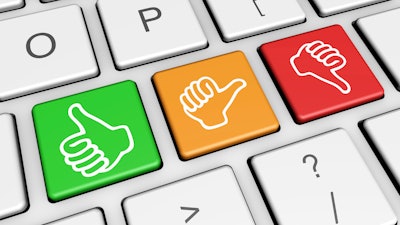
The plant floor is the beating heart of any manufacturing business. And success of any kind in the manufacturing business depends heavily on three things – product quality, consistency, and cost savings.
Balancing all three targets on the plant floor is not an easy task. To achieve it, you need quality management. This article will explore the basics of quality management, and how it contributes to effectiveness and efficiency on the plant floor.
What is Quality Management?
Quality management in manufacturing is all about the pursuit of excellence. In manufacturing, excellence is considered creating a superior product that satisfies the needs of customers, while at the same time creating value (revenues) for your business. Its origins can be traced back to medieval craft guilds. They stressed strict adherence to certain manufacturing processes and principles of the shop floor, to maintain product excellence, or “fine craftsmanship” at all times.
With the evolution of modern industrial manufacturing, the basic principles of craftsmanship also evolved into the discipline of quality management. The modern Quality Management System (QMS) has three main components:
- Quality Control (QC): maintaining a certain level of quality in all factors of production.
- Quality Assurance (QA): preventing defects in products and ensuring high levels of customer satisfaction.
- Quality Improvement (QI): focusing on the continuous improvement of all aspects of production, and preventing waste.
In QMS, there is a heavy emphasis on the need to look at every facet of a manufacturing business – from the shop floor to the top floor, and from vendors/suppliers to the final customer. But when you array all these facets on a matrix, you will invariably find the plant floor at the center. This is why the positive effects of QMS will most keenly be felt on the plant floor, even though it has a wide focus.
Here are the main ways in which Quality Management can benefit effectiveness on the plant floor:
- Focus On Hiring/Training: Despite tremendous progress in robotics and automation, humans continue to play a central role on the plant floor in modern manufacturing. According to Gartner, this will continue well into the future, as we design robots to augment human workers, instead of replacing them. And you cannot have product excellence with shoddy, untrained workers. QMS recognizes the importance of hiring qualified workers and providing adequate training to improve their skills. Employee training is vital for the future of manufacturing in the age of Industry 4.0.
- Process Review. The plant floor is a hub of activity, with workers involved in numerous complex and interconnected processes. Any flaw or defect in one stage can delay the chain and reduce the overall efficiency and speed of the production cycle. A key component of QMS in manufacturing is frequent performance audits and reviews of plant floor systems, equipment, and processes. The results are matched against industry excellence standards and/or organizational goals. This helps detect flaws and nip them in the bud.
- Workplace Safety. Plant floors and other manufacturing zones are workplaces with a high risk of accidents and injury. In the U.S., companies that don't follow OSHA guidelines on workplace safety run the risk of civil penalties and lawsuits. QMS puts employee safety and compliance as top priorities of an organization. According to Harvard Business Review, an accident-free plant floor is a more effective and productive area. Employees cannot function at the top of their skills when they are worried about personal safety. Personal safety has a great impact on employee turnover as well. High attrition can have a long-term impact on your operational efficiency and finances, as training and onboarding of new workers is slow and expensive. Finding new talent can be difficult, as the skill gap in manufacturing will exceed 2.1 million by 2030.
- Total Productive Maintenance. Machine malfunctions and breakdowns can cripple your productivity stats and affect the on-time delivery of products. Improper maintenance is often the culprit. To achieve perfect and uninterrupted production on the plant floor, you need total productive maintenance (TPM). As part of Lean management principles, TPM focuses on using advanced analytics, predictive maintenance, training, and increased collaboration between plant floor teams and maintenance teams. The aim is to create a safe, well-organized plant floor with minimal disruption or breakdowns.
Manufacturing is at a historic threshold of the Industry 4.0 paradigm. It promises better automation, 360-degree visibility, and penetrating new insights from data analytics. Together, these have the potential to improve the effectiveness and efficiency of the plant floor like never before.
At the same time, challenges remain, with an increasing skill gap, signs of economic recession, global instability, and sustainability concerns. To keep the plant floor humming along at peak optimization in these conditions, you need the holistic vision provided by Quality Management.
Bryan Christiansen is the founder and CEO of Limble CMMS.