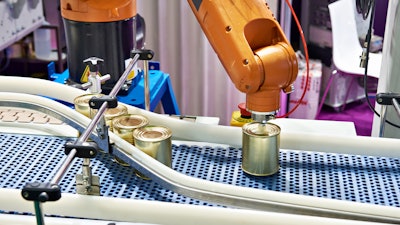
Robots have the potential to drastically improve the food and beverage manufacturing industry by increasing productivity. They are able to perform a wide variety of tasks, including palletizing, picking and placing, and boxing. They can also help combat the biggest concern food and beverage manufacturers have: contamination. Just like humans, who bring their own health risks to food and beverage manufacturing by spreading germs, robots have their own contamination considerations. But they can be greatly reduced by taking the right steps.
If the product is wrapped in some way, nothing can happen to it short of piercing. However, if a robot is handling something like a muffin, manufacturers have to take precautions for how the robot handles the food like they would if a person were doing it manually. It’s particularly important to make sure that robots installed overhead cannot contaminate the product. To avoid this, robots can be equipped with a small extension or gripper so that the robot never operates above the product where it can shed or leak. Sometimes, the manufacturer will use a bag or cover over the robot to alleviate the risk, but they have to think about a cleaning regiment and inspections for wear and tear when doing so. With these preventions, the risk of contamination decreases, improving the overall health standards of food and beverage manufacturing.
Before implementing robots, manufacturers need to think through how they want to move forward with an automation solution. First, they have to be clear about what their expectations are. It’s vital for the manufacturer to tell the integrator or robot provider what is critical and what scenarios need to be thought through, like distance and spacing. Let’s say a manufacturer is trying to replicate what six to eight people are doing in close proximity to one another, operating with two hands and working at Whitton
Simon Whitton is senior vice president at KUKA, a manufacturer of robotics and solutions for factory automation.