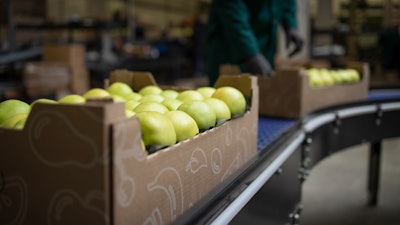
A warehouse execution system's (WES) sole purpose isn't exclusively machine control. From inventory management to product forecasting, to intelligent inventory management, a WES provides the brains behind the beauty of steel racks and automation. With the recent shift in the demand for certain types of food because of COVID (see AFFI’s report that frozen foods are 22.6 percent higher than 2019’s pre-pandemic baseline), manufacturers have been forced to adapt and find a solutions like robust WES that conforms to their specific business.
In the modern food manufacturing warehouse that employs automation, software is a key component to the operation. But not all solutions are built the same. Warehouses that employ basic automation have at least a control system, but a good WES incorporates both warehouse control and warehouse management system functionality, harmonizing the two types of systems together as one.
With a vast array of robust software applications available, taking advantage of them takes more than desire. Properly implementing an effective WES will not only bring benefits to the automation process, but it will also ultimately help increase the bottom line.
Benefit #1: Total Traceability
Appropriate food control can always be linked back to having good system-wide traceability and quality control. From the time the product is defined in the system to when it is actually removed from the distribution center, it is vital to have visibility and proper record keeping of all inventory.
One major measure of this is the number of manual touches. Food can easily be contaminated, even from something as basic as the pallet it is being held on, so the less human touch, the better. A complete WES is able to see when inventory arrives, where it was stored, if it was adjusted, where it has been taken, and whether the product is on the food distribution center floor. In short: the life of inventory can be tracked through shipment, reducing the risk for all parties involved.
Benefit #2: Increased Speed
Having a clear understanding of how the warehouse is operating will lead to an increase in speed and flexibility. This is helpful, especially in an event like a recall where time is of the essence. If there are delays, be it from routing or manufacturing, you are storing raw goods in your automated system and they need to be managed so that the product can be replaced as soon as possible. Quick access to log files and data allows the manufacturer to know exactly what happened and act with agility, ultimately making sure that tainted products are replaced and don’t make it anywhere near the end customer.
And while the customer may not know how much you have done to keep them safe, on the order fulfillment side, it’s also easier to appease the desire to want their product as soon as possible. The need for manual data input is reduced, lessening the chance of human error, order accuracy is increased, and naturally, throughput and labor activity is improved. A WES not only assists in making sure the product reaches end customers, it makes sure it gets to them quickly.
Benefit #3: A Better User Experience
Even with a WES in place, it would still lack impact if the user cannot take advantage of it. Gone are the days of spreadsheets filled with rows of nothing but numbers. Good WES software uses the latest tech (like Microsoft C# and .NET), is compatible with a variety of ERP systems, and will be able to deal with sophisticated storage and retrieval algorithms while presenting all the information in a configurable, easy-to-use interface.
Visualization alone can increase productivity. With today’s technology, being able to monitor and operate a warehouse in real-time using colorized arrows and 3D models is not out of the realm of possibility. Isolate inventory on the screen or zoom in on specific areas to check on the detail of a selected container. This level of increased exposure and control will save the time needed to identify operational issues and improve fault recovery.
Benefit #4: Savings
With all the above benefits, the payback of utilizing a proper WES with an automated system can stack from a variety of angles and grow over time. This includes saving time and resources in the following ways:
- Optimize warehouse space and equipment, saving you from having to expand or buy more automated machinery.
- Reduce loss from damaged, misrouted, or even stolen product because of better traceability.
- Lower unit cost per unit shipped.
- Improve customer service, gaining return customers and retaining loyalty.
Human error or natural disaster, with the prospect of a delay, can come from any direction. It’s imperative to be able to recover quickly and with accuracy. Utilizing an integrated WES gives food manufacturers the flexibility to keep their automated businesses running and allows the WES to grow with them.