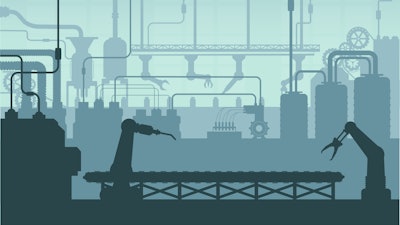
Companies across every industry have felt the impact of the COVID-19 pandemic. Worldwide shutdowns and stay-at-home orders have disrupted the global supply chain, and businesses have scrambled to adjust.
Manufacturing companies have been among the most heavily affected by COVID-19. Employee health and safety is, of course, the No. 1 priority, so those of us in the industry must now determine how to continue production safely and effectively, while adhering to social distancing guidelines.
If you're struggling with this challenge right now, here are five tips to help you pivot your strategy and set yourself up for success in the post-pandemic world.
1. Over-communicate
Communication plays an important role in manufacturing even under normal circumstances. Employees need to be kept in the loop about product changes, volume expectations, and quality control. With so much uncertainty in the news and employees asking questions, manufacturers must communicate frequently, clearly and with intent. Hold daily huddles with teams to share new information that may impact your operations, identify potential roadblocks early and map strategies to mitigate.
It’s equally beneficial during uncertain times to remind your team that you are available for them personally and will listen to concerns they raise about the health and safety of them as individuals and as part of a team. This keeps a two-way dialogue going and demonstrates to employees that you care about them. It is best to build these support and communication networks always, during challenging times it is downright essential.
2. Be flexible and adaptable
During production, you may have to improvise or find solutions quickly if something doesn’t go as planned. After all, glitches in production can happen. Take that same improvisational mindset when adjusting your operations for COVID-19. This is an unexpected and unprecedented situation; how can we adapt to this, too?
A good place to start is looking at your floorplan. Be flexible as you're thinking about your space and get creative as you map out how to give workers right amount of space to encourage social distancing on the floor.
You may also consider changing up your workflow and schedules to reduce person-to-person contact. A few things you can do on the personnel level:
- Have a 30-minute transition period between shifts to allow one group to leave the building before the second arrives.
- Stagger breaks to minimize any unnecessary interactions.
- Prohibit employees from crossing into areas outside of their immediate work area.
- Invest in additional cleaning services or rotations
3. Establish processes for quarantining and sanitizing common use items
In a manufacturing facility, employees are likely to come into close contact with lots of materials and equipment. It is paramount to have a plan for isolating and sanitizing these items and stations for employees to wash their hands or use anti-bacterial gels and wipes. For instance, at ProGlove, we implemented a dedicated area where objects are quarantined for three days. If the objects are needed sooner, we have mechanisms for cleaning and sterilization. Otherwise, frequently used tools and gear are washed three times a day.
4. Train employees on new procedures
It may seem very unnatural at first, but as a team, you must commit to building new social distancing habits. Go over the procedures carefully and explain them in detail. Hold short training sessions on rigorous hand washing, dressing and doffing practices with masks and disposable gloves, and extra equipment sanitizing – and be sure to reinforce these practices regularly with your employees.
5. Reward and recognize good behaviors
When you see your teams honoring the new protocols and adjusting to these new requirements, remind them what an outstanding job they're doing. Appreciation and recognition can go a long way in keeping people motivated – a difficult task when there's so much uncertainty. Remember, the better you can take care of your employees today, during a crisis, the more likely they'll be to stick with your company in the future.
ProGlove’s plug & play wearable barcode scanner.
We’re hopeful for a future where more technologies are designed with the needs of frontline workers are front and center.
Hansen