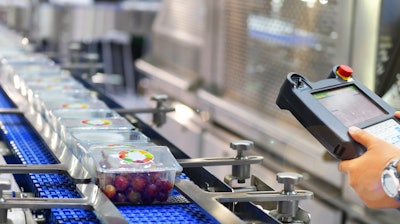
A smooth operating supply chain is necessary to manufacture and launch products on time. By contrast, knowing when, where, and how a disruption in the supply chain can affect your products is also essential to managing your product portfolio. Experienced product managers know they need to map out the component overlap between their product lines as well as clearly organize the dependencies within a given product roadmap. The interdependency between the supply chain and product decisions means that both departments must collaborate regularly.
Choosing the Right Focus
The process of creating new products can often mirror the process of cooking a meal. When planning a dinner for guests, the first step most people take is to ask what type of food their guests enjoy. Do they have any allergies or food restrictions? Knowing what types of food a guest can eat and enjoy helps narrow down the decisions on what to prepare for the meal.
Manufacturers follow a similar procedure for determining what products to improve or develop next. Instead of hosting house guests for beverages, dinner, and entertainment, manufacturing companies have customers to delight. The only way to know what consumers want is to do the research and ask them.
Digging Deeper on Consumer Demand
When hosting guests for a meal, researching what food they like can be as simple as calling them on the phone or texting them to ask. With product development, deciding on the next focus that will make customers happy requires more data. Product managers need to consult with customer success teams to learn the results of their customer feedback studies and market research.
Both qualitative and quantitative studies are necessary to gather insight into what the ideal customer wants. This is typically done by conducting surveys, hosting focus groups, and testing prototypes. Because the demands for products will change from market to market, conducting this research in each intended region is essential. Without this information, manufacturers run the risk of launching a product that flops on the market.
Knowing the demand is only part of the equation for choosing what products to develop next. The other parts of the equation are supply chain availability and financial feasibility.
Supply Chain Availability
Before committing to a menu for a dinner party, it’s necessary to find the grocery items and purchase them first. If a host intends to serve a rare dish and cannot find the necessary ingredients, they will need to adjust their plan. They are required to strike a balance between preparing food according to their ideal menu and finding the right ingredients for their recipes.
With products, securing resources is complex. The right components are vital to the production and must be procured well in advance of product timelines. Any disruption to that supply chain can cause complications, delays, or financial loss.
Disruptions and Challenges in the Supply Chain
Supply chain issues can impact both a grocery shop and a manufacturing procurement strategy. There are many factors that can impact a supply chain, and nearly all of them are beyond the control of individual companies. The globalized nature of manufacturing means that disruptions anywhere around the globe will impact many global companies in every corner of the market.
The following are potential supply chain problems:
- Resource disruptions - short supply of a raw resource or barriers in place to exporting and importing necessary resources.
- Shipping and distribution - disruptions that make it difficult or delayed to transport resources, supplies, and components around the world.
- Labor shortages - parts of the market where there are not enough workers to fill positions, causing delays and slowdowns in different industries.
- Labor disruptions - union disputes and strikes.
- Environmental impacts - environmental barriers, severe weather, or natural disasters that delay supply chain movement.
- Social factors - a global pandemic.
- Political factors - political tension, tariffs and sanctions, political conflict.
Financial Feasibility
Financial feasibility when preparing a meal for guests is fairly simple. Can the host afford the ingredients required for the menu? They have options to shop around at different stores and adjust their menu if a particular cut of meat is beyond their budget. Since the meal is an act of generosity or friendship, there is no need to plan for recuperating the costs of making the food. Profits and margins are not in question.
Product manufacturing focuses on profit because, without profit, there is no business. Product management teams need to work closely with their supply chain managers, customer success teams, and finance departments to ensure the product chosen for development checks all the boxes necessary to succeed. Do customers want it? Are the supplies available? Is it financially feasible? Does it align with the product strategy? If the answer is ‘yes,’ then the product or new feature for a product can be pursued.
Making Collaboration Easier With Software
A dinner party can only happen when the host invites the guests over on a certain day, time, and place. Communication makes that happen, and all the host needs is a cell phone, service, and a number. Collaboration between departments in a manufacturing company requires more than just a phone. Regular meetings help. However, software platforms designed to manage each division make it possible to share information between managers.
Supply chain managers have their choice of software platforms that make it easier to oversee and monitor the entire supply chain, from resource procurement to delivering components to the factory floor to launching finished products. In turn, product managers also have options for managing their product portfolios. Product roadmap management software enables product managers to map out each product with defined features, indicating an overlap in components and highlighting dependencies in a product so that when disruptions in the supply chain occur, they can make decisions faster.
Mitigating Risk With Cross-Functional Teams
The impacts of supply chain disruptions can be mitigated when cross-functional teams work together. The sooner the supply chain manager notifies the product teams about possible delays on components, the faster those teams can adapt their product plans. Gathering insight into how long and how severe a disruption may be will inform the product manager of the action needed to adapt the product plan. This collaboration and open communication creates true agility in product manufacturing across industries.
Maziar Adl is the co-founder and CTO of Gocious.