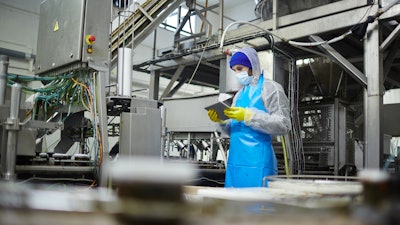
While most manufacturers in the food industry are accustomed to the variability in supply and demand that’s driven by multiple factors – including seasonality, droughts, tariffs, promotions and consumer fads – this year makes those variables seem trivial. Many food service providers have had to deal with almost zero demand. Other manufacturers have been forced to close due to employee illness. Others have had surges in demand based on changing consumption behavior, pushing their plant capacity to the max. This came on fast – and determining the new normal demand patterns is perplexing to many food and beverage executives, while they struggle with the near-term challenge of how to remain operational while overcoming supply chain and worker safety challenges.
iStock
The issues of speed and visibility in the supply chain are obviously of critical importance to F&B manufacturers. Many initiatives were implemented as an immediate response to the pandemic but are just a temporary stopgap. To meet these challenges long-term, many have had to take a closer look at ways in which technology can be used to not only optimize their processes, but also increase overall efficiencies. They recognize that the issues they address will continue to have a heightened importance.
Safety has also taken on a new or expanded meaning. While consumers and regulators continue to expect that manufacturers will only deliver products that are safe, the importance of worker safety has also increased. Those which prioritize investment and innovation in all areas of safety will likely see a competitive advantage.
iStock
Productivity & Efficiency
Productivity and efficiency are a main focal point for nearly every food company – whether such productivity is weighed amongst staff or the technology being used by staff.
As with all businesses that remained operational during the pandemic, keeping staff safe has been a primary priority for F&B manufacturers. However, quickly implementing flexible working arrangements isn’t as simple as it may be in other industries. The need to have fewer employees physically present in facilities has forced many manufacturers to accelerate their digital transformation plans. For many, in order to remain running at full capacity, this has meant an accelerated adoption of technological advancements, such as Artificial Intelligence (AI) and Robotic Process Automation (RPA).
In fact, the investment in AI helps address an issue which remains of key importance for the sector: supply chain visibility. According to a survey conducted by Sage and IDC, prior to March 2020, digital transformation in the F&B industry had focused mostly on improving operations (including supply chain and distribution) – which inherently had the biggest impact on productivity and cost efficiencies across the board.
Of course, this has become increasingly important recently, wherein supply chain optimization is paramount. F&B distributors have had to ramp up production in certain areas while dialing down production in others – all while maintaining productivity from staff and technological applications implemented previously.
Moving forward, to avoid manual calculations and shorten response times, manufacturers are likely to increase utilization of predictive analytic solutions as part of their supply chain management, particularly to predict and respond to any potential anomalies. Fortunately, this isn’t the only way such technology can help – the same AI will be able to reduce unplanned downtime, capital expenditure and asset maintenance costs, as well as improve safety and workforce effectiveness.
In addition, and in order to be prepared should another similar event occur again, many food manufacturers will need to upgrade or renovate their facilities to enhance production and incorporate employee safety best practices, as well as meet Food Safety Modernization Act compliance standards. These renovations will likely make room for automation around packaging and distribution operations, which will allow for repeatability and less human error. In general, and particularly post-COVID-19, the use of automated storage and retrieval systems (ASRS) will increase in popularity as processors look to reduce labor costs across their supply-chain networks.
iStock
Worker Safety
With outbreaks of e-coli and listeria popping up frequently in the past, food quality has always been a cause for concern amongst manufacturers and the public alike. Companies have taken great measures to ensure their products are processed, packaged and delivered safely to consumers.
However, employee safety is a bigger challenge lately than food safety. Companies are having to re-evaluate their floor plan to provide a safer work environment that accommodates social distances. Additionally, they have hired third-party cleaning crews to sanitize locations and machinery on a near round-the-clock basis. In addition, many are experimenting with UV sterilization, new ways to sterilize air flow (which is particularly important in meatpacking plants, where stagnant air is the enemy), and the inclusion of robotics to help clean while workers are off duty.
Many of these advancements are likely to stick around for the long haul, as scrutiny around internal corporate practices and their effects on public health and safety rises. However, it should be noted that while F&B manufacturers must comply with food safety regulations, they are still under incredible market pressure to operate efficiently and increase profits. This often presents manufacturers with a dilemma around how to drive down costs of sanitation (e.g., staffing sanitation processes and oversight), while still meeting necessary criteria and tests before go-to-market – hence the incorporation of AI and other technologies to complete tasks. However, even these physical technologies need to be sanitized regularly. This will be a key function and hurdle for manufacturers of the future to optimize and overcome.
Traceability
Traceability has long been of critical importance. However, it is becoming an increasingly important buying consideration for consumers, especially amongst younger generations who are demanding more information on where their food comes from, how it’s processed and packaged and when it’s arriving at their local grocer (or doorstep).
In fact, according to the same survey conducted by Sage and IDC, manufacturing executives said a key goal of theirs is to achieve 100% traceability over production and supply chain – which serves as a large part of their holistic digital mission.
Modern software will allow both manufacturer and consumer to maintain continued awareness of how products are stored, their status at all times, what quality control measures have been implemented and overall consumer satisfaction. From an internal standpoint, this will encourage perfected process management, increased plant floor production visibility, connectivity during all parts of distribution and insight into whether or not regulatory standards have been met.
While nearly every industry in the United States (and across the world) has been altered in some way shape or form, F&B manufacturing is a staple sector that every individual needs on some level; with new technological advancements around productivity, safety implementations and the incorporation of predictive analytics and increased traceability, it’s sure to grow in both efficiency and in regard to the way it protects the health of the public.
Edgett