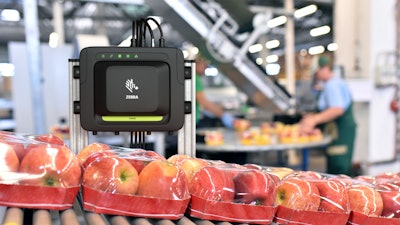
When it comes to safety, food and beverage manufacturers face strict regulatory requirements.
To protect consumers, the FDA’s Food Safety Modernization Act (FSMA) requires companies to keep detailed traceability records with the aim of quickly identifying and removing potentially contaminated foods from distribution and reducing foodborne illnesses. Manufacturers must therefore implement systems that accurately track food products and ingredients throughout the production process in real time.
Easier said than done, however. The wide range of products, ingredients, tools and processes creates a high level of complexity, making it difficult to effectively track and manage works in process (WIP). Amplifying these challenges, many operations fall under fast-moving consumer goods (FMCG) applications, which are characterized by quick product turnover and a need for greater production speed and accuracy.
Radio-frequency identification (RFID) technologies address these challenges by providing food and beverage manufacturers with real-time visibility into the status and location of in-progress goods and materials. These devices also empower manufacturers to identify and locate food safety issues, minimizing the risk that contaminated food products leave the factory floor and make it to grocery store shelves.
RFID systems are therefore a key ingredient in the success of a modern food and beverage plant, improving not only traceability, but efficiency and product quality. In addition to meeting FSMA requirements, these outcomes can help manufacturers boost consumer satisfaction and reduce food waste, enabling them to stay competitive in a highly dynamic industry.
Addressing Food Industry Challenges
Real-time visibility into the status and location of products is essential for seamless production. Many manufacturers, however, struggle with outdated or manual-based tracking systems. In the pursuit to improve traceability and maintain FSMA compliance, food manufacturers also face several challenges unique to their industry. These include:
- Product perishability and shelf life. Because products have limited shelf lives, manufacturers need precise inventory control and tracking systems to maintain optimal stock levels, reduce waste (see sidebar) and ensure food freshness. Unfortunately, many traditional inventory management methods fail to provide real-time visibility into stock levels.
- Demand variability. Food manufacturers must be able to adapt to fluctuating seasons and changing consumer demands. Without real-time visibility into inventory and production processes, such adaptability is impossible.
- Integration with existing systems. While they can help manufacturers manage and control their inventory, enterprise resource planning (ERP) and manufacturing execution systems (MES) still drive time by relying on humans to perform certain tasks. At the same time, it can be difficult to integrate WIP tracking solutions with existing ERP/MES platforms. Proper integration between the two is necessary to ensure information flows seamlessly between different systems.
- Data accuracy. To be effective, food traceability solutions require accurate, consistent data. It’s important for manufacturers to therefore invest in technologies that capture data with a high degree of accuracy, even at high speeds and volumes.
The Need For Greater Transparency
In addition to demanding more food options, consumers around the world are demanding more transparency. They increasingly want to know how and where their food was grown, harvested, processed, distributed and sold before it even reaches their kitchen tables.
According to Zebra’s Food Safety Supply Chain Vision Study, 70 percent of consumers want to understand how their food is manufactured, prepared and handled, while 69 percent want to know the locations from which their food is sourced.
Monitorization of line.Zebra Technologies
How RFID Can Help Minimize Food Waste
Roughly 1.3 billion tons of food end up in landfills — or enough to feed three billion people for a year. While there are many reasons to explain this waste, many have to do with poor inventory management, improperly documented product locations and a lack of production agility.
For example:
- There is an overproduction of food and not enough people to buy it prior to expiration.
- Due to poor stock rotation in warehouses and distribution centers, many businesses wait until food expires to pull inventory. At that point, however, it’s difficult to redistribute the food to discount sellers or food banks.
- Due to natural human error, workers unintentionally lose or mishandle products. They may also move food items without properly documenting their new location.
- Changing consumer expectations or the need to make space for new stock can quickly affect inventory, leading to edible food being discarded.
- Quality issues, such as listeria, salmonella or other contaminants, are identified and must be quickly addressed to minimize consumer risk.
Fortunately, RFID technology can help address these issues to reduce food waste. For example, RFID tags can confirm which items are currently on shelves and what their expiration dates are, ensuring inventory is properly rotated for first in, first out (FIFO) or first expired, first out (FEFO). RFID readers can also account for food and beverage stock during inbound and outbound operations, sending the information to digital ledgers that aren’t prone to human error.
In addition to RFID devices, many other technologies can help minimize food waste, including barcode scanners, machine vision systems, sensors, and planning and inventory management software, which can help manufacturers make better production, distribution and stocking decisions.
A majority of consumers cite the fear of foodborne illness and disease as the reason they want to know where their food comes from, while others are curious about the source, quality and safety certifications because of their organic preferences or concerns about genetically modified organisms.
RFID Technologies: A Recipe For Success
RFID solutions can help food and beverage manufacturers address these challenges while taking food safety, compliance and traceability to the next level. Using electromagnetic fields, this technology identifies and tracks objects that have a unique tag. This tag contains relevant information about the item on a chip and exchanges that information with the RFID reader.
Each RFID reader can capture data from thousands of tags per second without needing anyone to aim a barcode scanner in the direction of the tagged item. This automation lets companies know exactly which batch or lot is sent to each specific distribution center, restaurant or store location. The precise product visibility also improves supply and demand planning, forecasting and other efforts to ensure customers get the right product at the right time and place. It’s no surprise, then, that 41 percent of food and beverage industry decision-makers believe RFID technology improves traceability more than any other technology.
Other advantages of RFID systems, especially compared to manual or semi-automated traceability solutions, include the following:
- Better inventory visibility. RFID technologies provide food and beverage manufacturers with real-time visibility into their inventory levels, enabling them to make better, more informed decisions regarding stock replenishment and distribution. This visibility also ensures they properly rotate products and manage expiration dates, minimizing food waste.
- Automated data capture and accuracy. RFID technology automatically collects data on product movement and status, reducing human error and improving the accuracy of inventory records. This automation is particularly beneficial in high-volume environments and FMCG applications, where manual data entry can be time-consuming and prone to mistakes.
- Food safety compliance. RFID tags serve as a unique product identifier, allowing operators to precisely track and trace food products throughout the production process. Tags attached to items or packaging provide detailed information like origin, batch number and expiration date. This information is crucial for compliance with food safety regulations, ensuring greater accountability and transparency.
- Greater efficiency and product quality. By providing real-time data on the status and location of goods, RFID systems make it possible to monitor aspects of the manufacturing process. This capability can help manufacturers identify bottlenecks and inefficiencies, maintaining smoother production. By tracking products at each stage of production, RFID systems also ensure only the correct ingredients and processes are being used, improving food product quality.
- Scalability and interoperability. RFID technologies are scalable and can integrate with existing ERP/MES systems, providing a holistic view of production operations. This integration allows manufacturers of all sizes to synchronize production schedules with inventory levels and improve their overall operational efficiency.
Types of RFID Technologies to Choose From
Here’s an overview of RFID hardware and software that can help food and beverage manufacturers better manage inventory and the flow of goods:
- Handheld RFID readers. These portable devices provide the flexibility to track and trace food products in real time. They include mobile computers, wearable Android devices and hybrid units that offer both handheld and hands-free scanning. Another example is the Zebra RFD40 RFID sled, which can read over 1,300 reads per second for high-speed cycle counting.
- Fixed RFID readers. These readers offer speed and simplicity for managing high volumes of food goods. These devices are typically installed at a specific location — such as a conveyor — where they scan moving objects or wide zones. Featuring high bandwidth and computing power, fixed readers can even read whole pallets of goods, all while reducing labor requirements, improving accuracy, and minimizing time and cost.
- Inventory management software. Food and beverage manufacturers can further improve the way they manage, track and locate goods in real time by implementing a robust inventory management software to centralize their RFID efforts.
Zebra's technology on an additional packaging line.Zebra Technologies
Enrique Herrera is the Industry Principal of Manufacturing at Zebra Technologies Corporation.