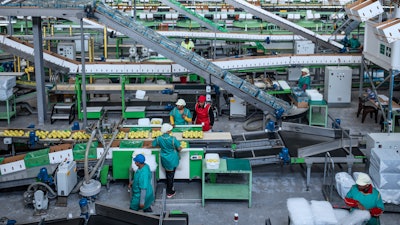
The food and beverage industry operates under stringent safety regulations, with compliance requirements continually evolving to meet consumer and regulatory demands. Industrial professionals – like engineers, purchasing managers and other decision-makers in manufacturing – must ensure that every aspect of their environment upholds hygiene and safety standards. One of the most effective ways to achieve this is through strategic selection and application of high-performance coatings.
Facility issues – such as cracked floors, rusting surfaces, roof leaks and condensation buildup – can quickly become breeding grounds for bacteria, posing risks to both product integrity and worker safety. To maintain compliance with FDA and other federal regulations, food and beverage processing facilities must implement coatings that not only enhance sanitation but also contribute to long-term cost savings and operational efficiency.
The Role of Coatings in Food and Beverage Facility Efficiency
With increasing regulatory oversight and the need for contamination prevention, coatings can serve as a risk mitigation strategy. Investing in durable, high-performance coatings across critical facility surfaces can significantly reduce maintenance costs, enhance sanitation and improve overall facility longevity. Below are key attributes to consider when selecting coatings for your food or beverage processing facility.
Seamless, Non-Porous Protection
High-performance coatings should provide a smooth, seamless barrier that eliminates cracks and crevices where bacteria can thrive. This applies to all surfaces – floors, walls, ceilings, roofs and manufacturing equipment. Moisture-resistant coatings further support sanitation efforts, reducing the risk of bacterial buildup and ensuring compliance with food safety regulations.
Heavy-Duty, Slip-Resistant Flooring
Food and beverage processing environments are often wet and exposed to grease and other residues, increasing the risk of slips and falls. Slip-resistant coatings with a textured surface enhance worker safety while meeting OSHA requirements. Additionally, these coatings should be formulated to withstand heavy machinery traffic, such as forklifts and carts, or new technology like automated guided vehicles (AGVs), to prevent premature wear and reduce the need for frequent repairs.
Long-Lasting and Durable Roof Solutions
Fluid-applied roofing systems provide seamless, waterproof protection that prevents leaks – one of the most common causes of facility contamination. These coatings extend roof life, resist blistering, chalking, checking, cracking and flaking, and eliminate the need for costly tear-offs. White roofing solutions further enhance efficiency by reflecting heat, reducing utility costs and supporting sustainability goals.
Resistance to Rigorous Cleaning Protocols
Facilities must endure frequent high-temperature and chemical-intensive sanitation processes. Choosing coatings that resist harsh cleaning chemicals, thermal shock and abrasion extends the lifespan of facility surfaces. Impact-resistant coatings also help mitigate damage from dropped tools or heavy equipment, reducing the need for costly repairs and downtime.
Cost-Effective, Long-Term Maintenance Strategies
Applying high-performance coatings is an investment that pays off through reduced maintenance and extended facility lifespan. Regular site surveys by protective coating experts help decision-makers identify vulnerabilities and determine the best coatings to enhance durability and cleanability. These surveys can pinpoint specific areas needing additional protection, allowing for targeted applications that optimize maintenance budgets and operational efficiency.
Ensuring Compliance While Reducing Costs
Facility integrity is crucial for both regulatory compliance and consumer trust. High-performance coatings not only safeguard hygiene and sanitation but also contribute to operational efficiency by reducing downtime, minimizing maintenance needs and extending the lifecycle of facility surfaces.
By regularly assessing facility conditions and investing in coatings engineered for food and beverage environments, companies can stay ahead of compliance challenges while improving overall cost effectiveness. Rather than waiting for an inspection to reveal vulnerabilities or issues, industrial professionals should take a proactive approach – implementing coatings that stand up to the rigorous demands of food and beverage manufacturing while supporting long-term operational goals.
Feraas Alameh is the market segment manager – food & beverage for Sherwin-Williams Protective & Marine.