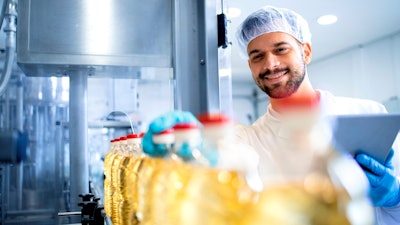
When it comes to laboratory testing, data is mission-critical for food and beverage laboratories. It gives lab managers the information they need to evaluate samples, identify patterns and make decisions, ensuring successful experiments and results. And yet, it is not uncommon for labs to find themselves buried under the weight of inefficient workflows, numerous testing processes, and a deluge of mismanaged data — and many labs are still operating on pen and paper.
Laboratory Information Management Systems (LIMS) provide a comprehensive solution for managing lab operations, including sample and data management, quality control, workflow automation, inventory management and reporting. Still, many organizations operate across multiple disparate LIMS, leading to inefficiency and the expenditure of precious resources.
With quality control and manufacturing departments dealing with hiring challenges and increasing throughput expectations, food and beverage companies consolidating their LIMS are using that as a catalyst for streamlining QC operations, increasing efficiency and accelerating the time it takes to release products to market.
Streamlining and simplifying testing operations is possible, and it offers several benefits that help maximize the true potential for driving deeper insights, improving processes, and gaining a holistic view of your laboratory operations.
Improve Data Quality
With millions of data points flowing in and out of labs, a commitment to data quality is the first step for food and beverage companies looking to achieve a successful digital transformation. Back in 2006, British mathematician Clive Humby declared that data is "the new oil" of the digital economy. In the 17 years since that statement, companies have embraced digital transformation to varying degrees.
The massive volume of data and the sheer velocity at which it needs to be collected from various sources requires the proper infrastructure to extract value and derive meaningful insights. LIMS supports this by digitizing lab operations, automating processes and workflows, and standardizing data collection procedures.
According to Gartner, poor data quality costs organizations an average of $12.9 million annually. Aside from the immediate hit to revenue, inefficient and unsystematic data maintenance results in regulatory and compliance risks and, over time, increases complexity that harms enterprise decision-making. By consolidating LIMS across food and beverage labs, you can establish standards for proper data handling and support integrity and accuracy in your valuable data.
Enhance Data Security
In today's interconnected world, data security is of utmost importance. The most common data security issues in the lab include:
- Unchecked password sharing
- Leniently controlled user privileges
- Poorly defined access controls
- Inadequate data backup and recovery mechanisms
- Vulnerabilities in software and systems due to outdated technology
- Improper disposal of physical records and digital files
Each of these areas creates potential vulnerabilities for hackers to access sensitive information. By consolidating your LIMS, you can implement robust security measures to protect your intellectual property and sensitive information. A centralized LIMS enables better control of information access rights and minimizes the risk of a data breach through encryption.
Simplify Compliance & Reduce Business Risk
In the food and beverage industry, the safety and quality of your products are vital to the world's food supply chain. Implementing a solid informatics platform helps you simplify the process of confirming that all current regulations are met at each point in the workflow and facilitates automation and integration with instruments.
A lack of data integrity can lead to facility shutdown, import bans and recalls, as well as a drop in brand value and market share. A consolidated informatics system provides the opportunity to gain full traceability of your products and monitor your food production all the way to the kitchen table.
It is well understood that a LIMS can help with regulatory compliance, but there are other compliance initiatives that brand owners and organizations must contend with.
Oftentimes, internal compliance objectives or compliance with customer objectives are much tougher to meet, as they can vary greatly from product to product, site to site, and customer to customer. Having one solution that manages all your compliance objectives can drive significant productivity, simplify your lab and quality operations, and provide a differentiated experience for your customers.
Ultimately, whether it's for regulatory, customer, or corporate compliance, it's important to capture, automate, track, and report on correct data, processes, and evidence to help you reach your compliance goals. By consolidating your food and beverage lab testing, you'll get a unified, holistic view of your data that sets you up for success in simplifying compliance.
Foster Knowledge Sharing & Collaboration on Experiments
Collaboration is a potent means to enhance the development of new products by empowering multiple teams with various perspectives to work together toward a solution that can be tested at once. Yet, a lack of transparency across LIMS vendors and decentralized systems and processes slows market growth and expansion.
Consistent LIMS across your labs enables teams to collaborate seamlessly on experiments, share findings, and easily exchange knowledge.
By breaking down organizational silos and enabling real-time access and visibility, food and beverage lab and QC technicians can rely on each other's expertise, validate findings, and make more informed decisions no matter where they are located. Through collaboration, scientists improve the quality of research, maximize their efforts through collective intelligence, and avoid duplication of effort.
At the enterprise level, a consolidated LIMS provides comprehensive access to company-wide lab work, helping executive teams make more informed decisions based on insights generated across all their labs.
Reduce Experiment Redundancy & Improve Productivity
With rapidly changing consumer expectations and technology, teams need flexibility and agility to adapt to quickly evolving processes and tests. However, when organizations use a variety of informatics solutions and LIMS, data and insights become fragmented and disjointed, leading to complex operations that are difficult to scale. Having a consolidated LIMS as a centralized, single version of the truth enables food and beverage organizations to have all staff working off the same information at the same time, in turn eliminating silos, miscommunication and duplication of efforts.
Consolidation also releases IT resources from needing to support a complex infrastructure of solutions. Multiple systems oftentimes mean more money, time, and resources are wasted managing each system separately. With one system and one provider, IT can have a single view into the organization's environment and infrastructure.
Paper-based data management processes belong in the recycling bin. A singular, consistent, yet flexible system that addresses user and site-specific needs is crucial to reaching and maintaining a manageable cost base and staying ahead of the competition.
By consolidating your food and beverage testing processes and implementing a unified LIMS solution, you can enhance data quality, enable data security and collaboration, foster collaboration and improve productivity.
Brandon Henning is the chief product officer and chief marketing officer of STARLIMS. Henning is responsible for driving the company's product and go-to-market strategies. He comes to STARLIMS with more than 20 years of product management, marketing and IT experience, with a focus on building and delivering solutions for regulated industries, including pharmaceuticals, medical devices, food and beverage and Automotive.