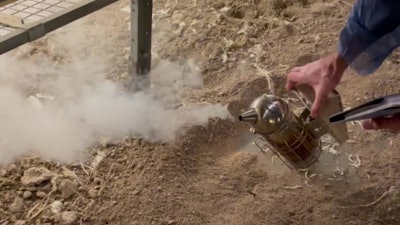
In recent years, several large fires have occurred at U.S. egg producer facilities, causing significant damage and loss of birds. In fact, the risk of catastrophic fires at egg layer facilities has increased in the past decade, as illustrated by dramatically rising insurance rates.
Several factors can heighten the fire risk in layer houses including size, remoteness, high airflow, prevalence of dust and in cage-free environments, the ability of birds to move more freely.
Despite these challenges, many layer houses are built with little to no fire protection, according to Tim Gess, senior product development engineer at Poultry Management Systems, Inc. (PMSI), a company that provides advanced monitoring and control systems for poultry houses.
“Egg layer structures are like industrial plants, given the level of equipment and automation required to carry feed, provide water, convey eggs, remove manure, furnish light and provide sufficient air flow,” said Gess. “Today, a layer house can cost 20 million dollars and a fire can destroy it in a matter of minutes. Insurance companies have sought to cover the losses by rapidly raising premiums to the extent that, over ten years, insurance deductibles have risen dramatically, up to a hundred-fold.”
The larger the layer house, the greater the danger that the combination of feed dust, chicken feathers, and high airflow may provide combustible conditions that can fuel a fast-moving fire.Honeywell Building Technologies
The trend toward cage-free operations has increased the potential of fires, due to dustier air than in-cage housing, combined with more accumulated manure, feathers and other litter.
Cage-free chickens are also known to pick at conveying equipment and electrical wires, potentially causing damage that can additionally increase the risk of fire.
As a result, the industry is seeking fire detection solutions that provide very early warning but can also survive the challenging conditions of the dirty, dusty environment found in layer houses. In traditional detection systems, dust is often misidentified as smoke and can cause nuisance alarms.
“When smoke is detected, the patented logic in PMSI’s ThERM system immediately shuts down equipment such as fans and conveyors that contribute to a fire’s rapid spread. This preemptive action reduces the damage and gives responders time to arrive,” said Gess.
Smoke Detection Challenges
The larger the layer house, the greater the danger that the combination of feed dust, chicken feathers and high airflow may provide combustible conditions that can fuel a fast-moving fire.
The leading causes of layer house fires are typically electrical malfunctions, exacerbated by fans and conveyors that move the fire to new areas.
If a fire occurs, the volume of air moving through the structure exacerbates the situation due to high airflow conditions that can dilute smoke, a situation that can make fire detection more challenging with traditional smoke detection systems. The result can be an extremely fast conflagration that consumes a facility in minutes.
After researching available technologies at a conference a few years ago, Gess learned about the VESDA Laser Industrial (VLI) aspirating smoke detector from Honeywell. The ASD system draws air samples through holes in long runs of durable industrial pipe mounted along the walls and ceiling.
Advanced technology like the Honeywell VESDA Laser Industrial aspirating system detects smoke at the earliest possible stage, while reducing false alarms and maintenance in the egg layer industry’s complex structures.Honeywell Building Technologies
According to Khaleel Rehman, director of development for Honeywell’s advanced detection fire team, VLI is well suited for environments with high background pollution levels and variable particulate sizes and can manage potential challenges such as nuisance alarms created by the environment, reduced detector life and smoke sensitivity degradation.
Clean Air Zero is a user initiated VLI feature which complements absolute detection and safeguards against nuisance alarms. This is achieved by introducing clean air into the detection chamber and taking a reference reading of the chamber background.
This reading is then offset against the actual environmental background to maintain consistent absolute smoke detection over time. The user initiates the Clean Air Zero process using Xtralis VSC. It takes up to 60 seconds to complete, during which time the detector is offline. The Clean Air Zero function is activated during every routine maintenance site visit.
With more detailed information to analyze, the unit can differentiate smoke from other factors that could cause false alarms such as dust and chicken dander. The detector’s high sensitivity chambers and cumulative sampling can deliver the earliest possible warning of fires even with high airflow conditions.
Pre-engineered sampling holes are positioned in the pipe network for faster, more efficient commissioning and installation. The unit is also designed with a patented intelligent filter that significantly reduces the contaminants entering the detector and dramatically extends operational life.
After initial testing and observation of the system, PMSI arranged to install and definitively test the VESDA VLI with the assistance of Wiss, Janney, Elstner Associates, Inc., (WJE) a third-party laboratory and field test consulting group.
The system was installed within a three-level layer house in Iowa. The layer house is 468 feet long, 87 feet wide and 41 feet high with fresh air vents, 63 cooling fans and 54 fans that keep air circulating.
The initial installation included two VESDA VLI detectors with air sampling holes positioned near exhaust fans located along the side wall of the layer house. In dusty environments, frequent maintenance is required to ensure the desired sensibility is maintained.
As sampling holes get cluttered by accumulated dust, the airflow gets reduced, which will then affect the sampling hole sensitivity. This may also result in frequent and costly maintenance visits.
To deal with the high dust levels, an automatic air purge system was installed on the sampling pipes to clear out dust on a regular schedule, minimizing both potential false alarms and maintenance.
The air purge system operates autonomously to remove dirt from the sampling holes by using pulsated compressed air. An integrated controller starts a cleaning cycle with selectable interval programs, cleaning up to four independent sampling channels.
Gess notes that one of the benefits of the system is the ability to install and configure the piping wherever desired. “We can place the air sampling holes exactly where we want and the pipes can be routed over, under and through existing building elements,” he said.
To provide reliability and longevity in the dusty egg layer environment, the unit comes in an Ingress Protection Marking IP66 enclosure that provides protection against the ingress of dust and ammonia vapor.
“The VESDA VLI comes in a case that does not need special handling or protection. Even though the unit has sensitive electronics inside, we were able to put it right in with the birds,” said Gess.
The first full test of the system was conducted in the summer with the fans constantly running on high to cool the birds. The next test was in the winter when ventilation and cooling requirements were lower. With less fresh air coming in, more dust and condensation were present.
The results of the testing have been very positive.
“The system is quite stable and did not false alarm. Also, the unit’s self-diagnostics tell us if there is an open or blocked line and with the purge system it can resolve some blockages on its own,” said Gess.
Due to the success of the smoke detection system in testing, PMSI and the customer decided to implement the technology in additional layer houses under construction at a nearby farm.
For the layer industry, early fire detection technology like the VESDA VLI combined with automated systems can quickly shut off equipment and dramatically slow the rate of fire. This approach can protect multi-million-dollar investment in structures, animals, equipment and automation system components.