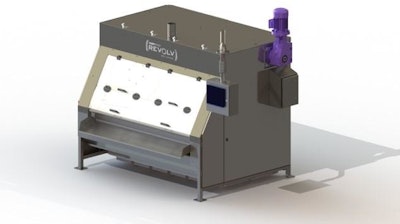
Most of us would agree: everything’s better when smothered in chocolate. Or yogurt. Or maybe peanut butter. AD Process Equipment, a Gray company, knows this, which is why the Naperville, Illinois-based custom equipment and process engineering solutions provider offers the REVOLV™ line of belt coating systems.
They turned to long-time supplier NORD DRIVESYSTEMS in Waunakee, Wisconsin, for assistance with a critical component of the redesign.
A Century of Confectionery
Belt coating systems are nothing new. In fact, the first “enrobing” machines came online in Europe more than a century ago and soon made their way to the United States. History lesson aside, AD Process Equipment manufactures a wide range of machinery for use by confectionery, chocolate, coffee, and cannabis producers, with subject matter expertise to integrate the equipment into efficient process systems. These include demolders and depositors, cookers, cooling wheels, polishing pans, and more. The REVOLV belt coater, which, as its name suggests, applies uniform coatings such as chocolate and yogurt to nuts, dried fruit, pretzels, coffee beans, cannabis products, and more.
The heart of the system is a rotating tank that keeps these products in continuous motion during processing. An atomizing spray nozzle sits overhead, delivering precise amounts of glaze or sugar according to recipes contained within an onboard PLC equipped with a user-friendly interface. When ready, a pulsating discharge mechanism drops coated goods into a conveyor system that carries them to a series of self-stacking trays. The entire system is fully automatic, and thanks to its CIP (Clean-In-Place) design, is both sanitary and easy to maintain.
Good to Great
When the REVOLV coating line was acquired from another machinery manufacturer, the team saw an opportunity to update the design to add features and cost effectiveness to the already high-quality system. For example, the catch pans sitting at the bottom of the machine were once custom-made but have been changed to standard, off-the-shelf components to reduce material costs and allow for easier replacement. A set of polycarbonate access doors now have stronger magnets to prevent accidental opening during operation and are equipped with locking mechanisms for additional security. The new user-friendly control interface simplifies programming while providing greater flexibility and the ability to add different recipes on the fly. There was also the elimination of the belt drive that once powered the coating belt in favor of a NORD gear motor. This makes the unit far easier to assemble and saves customers a lot of time during routine maintenance.
Aaron Hansen, the district sales manager for NORD, explained that there were some excellent reasons to use the company’s SK 9012.1 UNICASE helical-bevel gear motor. Boasting a premium NEMA-certified, high-efficiency 3 hp motor with stainless steel hollow shaft, food-grade lubrication, and an IP66-rated washdown enclosure, the unit’s right-angle design gave AD Process Equipment a space-saving, integrated, and dependable alternative to legacy belt drive solutions.
Hansen noted that the 90-series bevel unit is a great performer, but thanks to the custom paint selection, it is also quite attractive. “They requested a blue lilac color, which we supplied using NORD’s four-step Severe Food Duty 3+ (NSDF3+) with clear coat paint option,” he said. "It's just one of our many surface treatment options, which range from basic protection for general-purpose applications to those designed for extremely caustic or contaminated atmospheres. The NSDF3+ sits right in the middle and is ideal for food packaging areas.”
Each of these surface treatments is available in a range of standard colors, he added, or can be color-matched to the customer's specific requirements. "It really stands out," said Hansen.
A Long Partnership
The REVOLV belt coater redesign is the latest example of AD Process Equipment and NORD collaborating on custom equipment. The companies have been working together for many years, not only on this piece of machinery. The product offerings, along with service and support, have been key throughout the partnership.
From her perspective, Brook Harter, technical sales at AD Process Equipment, is similarly pleased with the revamped REVOLV unit and is more than happy to show it off to potential buyers. “This unit has a nice compact footprint, which is a main benefit compared to some other conveyance lines I’ve seen out there,” she said. “I’ve heard from many customers that the REVOLV’s tumbling motion produces an extremely consistent coating no matter what they put into it. The changeover is both fast and easy, and the REVOLV is ideal for integrating into their total process needs.”
Another advantage of the system is the “dual valving” to create separate coating zones for processing smaller batches. The machine saves multiple recipes, so customers can easily switch between product runs to meet market demand. With various recipes comes the need for additional cleaning. The REVOLV unit has accessible components from the side and rear doors, and the belt is easy to remove, which helps increase throughput and avoid the hassle that normally comes with changeover.
For companies not yet ready for these high throughput capabilities, AD Process Equipment also offers a tabletop version—the Mini REVOLV—designed for small batch sizes, retail stores, and product testing and development efforts. The Mini REVOLV and its larger cousin are each made in the USA.
AD Process Equipment and NORD will continue to work together to bring the latest tools, equipment, and drive technology to their customers – a testament to the cooperation between the two companies and their commitment to serve the Food and Beverage industry now and into the future.