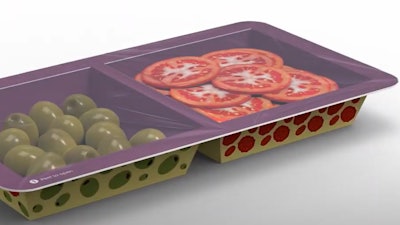
TAUNTON, MA — Harpak-ULMA recently announced the official launch of its innovative PaperSeal packaging technology as part of the company’s initiative to fundamentally rethink packaging systems to promote green packaging alternatives across the food industry.
Public concerns, regulatory actions, and powerful consumer trends such as e-commerce highlight the hefty environmental price of single-use packaging waste. Consumers have strongly embraced ubiquitous, convenient single-use packaging, and proponents point to its role in minimizing food waste and maintaining freshness at low cost. Replacing traditional substrates with plastics better accommodates consumers’ demand for convenience, but much of today’s multi-material packaging cannot be reprocessed with existing recycling systems. The complexity and challenges associated with plastics recovery emphasize the importance of reducing overall plastics volume by substituting innovative, renewable single-use packaging material and methods.
Structural impediments in the current industry supply chain can actually impair the adoption of sustainable packaging materials and methods, explained Jerry Rundle, Vice President of Sales for Harpak-ULMA’s tray packaging lines. “Entrenched producers are using hundreds of millions of plastic trays each year. They’re embedded in long-term supplier contracts and vested in the associated packaging equipment. To say that changing direction is difficult is a bit of an understatement – it’s like turning the proverbial aircraft carrier. There’s just too much industry resistance. On the other hand, new market entrants don’t have those constraints. For example, new plant-based meat companies are adopting sustainable paper-based tray packaging materials and methods out of the gate because they’re not embedded in the status quo.”
Rundle has had his share of experience attempting to overcome such impediments. Harpak-ULMA has promoted G. Mondini’s new line of PaperSeal trays as a sustainable alternative to plastic trays, he explained. This innovative packaging concept is the result of a global collaboration between G. Mondini and Graphic Packaging International, which officially launched the new line in North American markets this past February, and in Europe in May 2019.
“Graphic Packaging has more than ten line placements already producing commercial products for multiple customers throughout Europe and Asia,” said David Devenport, Vice President, consumer products and convenience for EMEA at Graphic Packaging International. “This has been achieved in less than 12 months from launch and the momentum is building.”
Trays are produced with renewable fiber sourced from sustainably-managed forests and can employ a variety of striking, innovative designs for retail presentation. Each tray utilizes 80-90% paperboard and 10-20% film, depending on tray dimensions - dramatically reducing plastic use and limiting base tray waste to just 2% - the lowest in the industry today. In addition, the tray film liner is easily separated from the paperboard after use, allowing for the paperboard portion to be recycled. A unique reinforced, one-piece flange design makes sealing surface strength and consistency equal to traditional plastic trays, as well as facilitating automated paperboard de-nesting – a pain point in other paperboard solutions. Trays can be stacked flat for logistics and inventory. The hermetically sealed tray provides up to 28 days of shelf life depending on the application, making it suitable for a wide range of applications including cheese, fresh or processed meat, ready-made products, frozen foods, snacks, salad and fruit.
Carlo Bergonzi, Harpak-ULMA’s Product Manager for Tray Seal, elaborated on Rundle’s observations regarding efforts to improve producer adoption for paperboard-based packaging solutions, “PaperSeal’s design works easily in existing denesters and conveyors – we know, we’ve tested it. Put a new set of tooling in your Tray sealer and you’re ready to go. It’s extremely adaptable to your existing equipment and no more expensive to produce than plastic trays. Also, PaperSeal trays are formed with pre-cut film - there’s no flop or film hanging over the tray – it’s a very clean look that also reduces film waste.” Bergonzi sees PaperSeal as an attractive alternative to traditional plastic clamshell produce packaging. “Clamshells are typically loaded in the field, and difficult to transport. In addition, consumers appear to prefer a lid seal, while retailers now prefer “tamper” evidence designs. Other major advantages of PaperSeal are its ability to accommodate one-dimensional multi-compartment trays and add header/hanging features to the package. The G. Mondini Trave also incorporates a “Platformer Plus” option that accommodates a PaperSeal stacker unit. When you combine all that functionality, the dramatic reduction in material waste, plus the ability to pop it into your existing line inexpensively – it makes this an extremely pragmatic sustainable solution.”
Rundle agrees and added, “We recognize that the North American market dynamics are different than European markets. We plan to work with some existing customers that already own a Mondini Tray sealer and want to trial sustainable technology on a new product line. It’s a low risk, low-cost scenario. We can re-tool a line in 10-12 weeks and they can be producing a new, sustainable package style at moderate volumes pretty quickly.”
PaperSeal has been available in Europe since September 2019. This year, G. Mondini has been nominated for the annual Best Packaging Award for its PaperSeal Technology. The contest was created by the Italian Packaging Institute and has been held every year since 1957. The 2020 award targets innovations that improve and simplify the user experience, from new materials to the shapes and methods of use. It also recognizes producer needs to communicate brand values, company history, offers, promotions, and implement new ways of engendering customer loyalty.