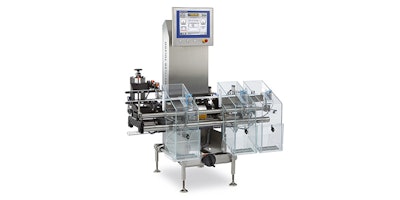
A key requirement to ensuring conformity of packaged food is that all products are as accurate in weight as possible to advertised values. In this blog, we look at weight compliance requirements, how manufacturers can consistently meet these and the business benefits of precision weighing.
Compliance Requirements
Overall, weight regulations aim to protect consumers against short weight or measures. In the United Sates, different regulatory agencies apply their rules by those given in NIST Handbook 133. There are two general rules:
- The average weight of a lot of inspected products must not be below the label weight on the package.
- No individual package can have a weight that is outside the maximum allowable variation (MAV), given in HB 133.
Ensuring Precision Weighing
Manufacturers are obligated by law to ensure packages are not underweight, and are also interested in ensuring they are not overweight thereby losing profits. The solution to achieve both is using a checkweigher. This type of product inspection system works by weighing each packaged product in real time, classifying all items by pre-defined weight parameters and rejecting any non-conforming goods for further investigation.
The checkweigher is initially calibrated during installation. To function at its optimum, the system should be verified with test samples at locally pre-defined intervals. It is also vital that all products are stable when presented to the checkweigher, as any vibrations or movements will affect weighing accuracy. Specialty conveyors, such as sidegrips and top-bottom conveyors are used to transfer packages smoothly, when the package is difficult to transfer. To make sure packages are presented individually, starwheels, timing conveyors, and timing wheels can be applied to regulate packages one at a time. To provide the packages at a correct, consistent pitch for weighing, spacing belts and timing screws are applied. These “tools” are used for individual lines, dedicated to single products, or for multilane systems for multiple package sizes on the same machine.
Benefiting from Verifying Product Weight
Other than meeting regulatory requirements, precision weighing brings an abundance of business benefits:
- Avoids product recalls and associated costs and repercussions.
- Helps ensure customer satisfaction and protect brand reputation from underfill product.
- Identifies overfilled product offering the opportunity to adjust fill levels
- Enhances productivity and saves costs by measuring and reporting production line performance. For example: an optional feedback feature on checkweighers detects deviations away from the target content weight and automatically adjusts filling machines located further up the line.
- Proves due diligence to authorities through real time monitoring and reporting of all product inspection activity including production counts, batch tracking and weight.
- Facilitates lot quantity checking by regulators. An Action Counter software option can reject a pre-defined number of accepted products for further scrutiny. This is achieved without stopping or slowing down the production process.
To help manufacturers achieve further product conformity requirements, such as inspecting for contaminants and product/packaging integrity checks, checkweighing technology can combine with another product inspection technology, such as metal detection, in one machine. Combination inspection systems will also improve production line efficiencies and overcome production space constraints.
To discover how packaged food manufacturers can achieve conformity, please read our white paper ‘Ensuring Conformity of Packaged Food'. For more information about checkweighers, simply download ‘The Checkweighing Guide’.