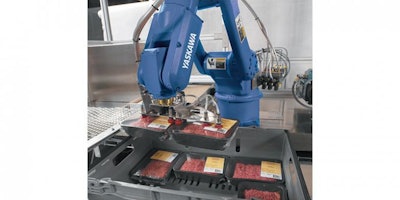
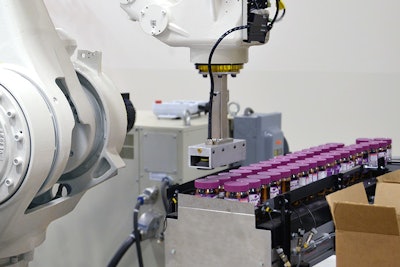
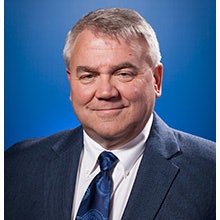
Over the past decade, factory automation has been a key area of focus for the majority of manufacturing sectors. The concept of creating “smart” factories, capable of producing superior products to meet complex demands with greater safety and efficiency to gain competitive position, has infiltrated industrial culture for various reasons. Those factors, however, have evolved over time, leading the way for a modernized and exciting era within the global packaging industry.
Historic Reasons For Strong Market Growth
Initially, labor and legacy costs — associated with maintaining a high level of manual labor — necessitated the drive towards facility automation. The importance of human safety within production environments, coupled with the need to eliminate repetitive motion injuries via sound ergonomic practices, soon followed, catapulting automation spending.
Fierce competition, brand recognition and customer loyalty continued the trend toward the application of automation solutions, significantly impacting the corporate profitability of many early adopters. Financial gains, combined with increased production capacity and flexibility, have maintained the need for automation utilization; so much so, capital expenditures for plant automation in the packaging sector are projected to grow at a stout 9.5 percent compound annual growth rate (CAGR) over the next five years, reaching nearly $60 billion globally by 2023.
While the growth of industrial automation throughout the consumer packaged goods (CPG) industry remains steady, the influencing factors advancing that growth have changed, necessitating the consideration for plant automation from many companies that have yet to adjust production methods.
Key Factors Giving New Relevance
Food Safety Modernization Act (FSMA)
Perhaps the most recent factor is the Food Safety Modernization Act (FSMA), which is now fully implemented after a three-year phase-in plan. In general, the FSMA requires any manufacturer within the food supply chain to implement improved processes, new protocols, additional inspections and overall safety to help eliminate the risk of contamination.
The focus is on preventative measures to avoid food safety problems before they develop — as the fiscal costs and lack of consumer trusts associated with product contamination or recall can be devastating to a manufacturer. Food and beverage companies are feeling the pressure to meet requirements, looking for solutions to address the challenges at hand, especially where open or unpackaged food is present.
Manufacturers are realizing the intelligent automation of many packaging functions can make managing a food safety plan easier and manufacturing a wide variety of product combinations possible, greatly reducing risks and accelerating business in the process.
Labor Unavailability
While the issue of cost control — specifically labor expenditures — is nothing new, the importance of labor costs is gaining new significance with the escalation of minimum hourly rates. Likewise, the condition of labor availability is now a reality, leaving many manufacturers frustrated with not being able to find or hire enough workers to adequately staff operations. In cities and rural areas alike, the search for qualified temp-to-hire or direct employees is difficult, and the situation is prevalent in both large and small companies. For these businesses, considering automation is a logical next-step to help alleviate dilemmas of this nature.
Operational Equipment Effectiveness (OEE)
As with any manufacturing process, speed is a vital facet that can drive production rates higher, helping to improve profitability. A direct correlation to this is the demand to maintain operational efficiencies, or Overall Equipment Effectiveness (OEE), as efficiency in manufacturing is greatly influenced by the correct use of manufacturing equipment running at peak performance. Utilizing OEE as a strategic management tool for continuous improvement is generating a wealth of production information for manufacturers today. The knowledge gained is allowing company leaders to better understand manufacturing processes on the shop floor, and it is causing manufacturers, both large and small, to realize the proper utilization of automation solutions can be a valuable tool for improving changeover times, assisting with rapid information diagnostics for troubleshooting, and maintaining product consistency and integrity.
Safety Standards For Collaborative Robots
From a robotics perspective, the evolution of safety technologies has permitted robots to work in collaboration with humans in a shared work space. Collaborative robots (CoBots) offer an ideal balance of strength, flexibility and efficiency to manufacturing operations for companies of all sizes in diverse industries; likewise, CoBots can accomplish tasks previously performed by humans, permit portability to different work zones and provide a simple method of “teaching” motions, versus conventional programming.
These easy-to-use robots, with industrial pedigrees, offer an intuitive method of programming, where the robot can be hand-guided within a workspace to learn the required precise waypoints and task path. When a teach pendant is used, the interface consists of simple instruction blocks rather than complex robot code, keeping the overall premise of simplicity in every aspect of a collaborative robot application. Removing the complexity of programming, usually associated with industrial robots, allows the user to increase efficiency through faster deployment.
Emerging Technologies
Emerging technologies in the robotics industry are paving the way for new automation methods. Powerful 3D vision is more easily applied to previously difficult applications, and mobility of robots for picking tasks, via autonomous vehicles, now emulates what has been a totally manual function.
Similarly, common controls platforms are now available, providing end users with a more efficient programming process. These unique interface options give operators the power to have a single source of control over in-house robotic applications without having to manage multiple processors or devices. It is also a method of automation control that enables operators to oversee robots and their components in a well-known programming environment, where knowledge of specialized robotic programming language is not required. This simplification of an innovative control scheme applies tangible cost reductions in several areas and increases the depth of personnel capable to program or maintain robotic systems.
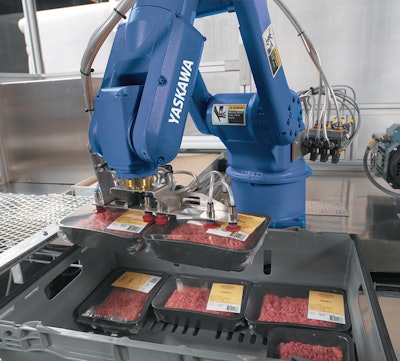
A New Era of Productivity
The dawn of a new and exciting era within the global packaging industry is here. For a company to be poised for productivity in today’s competitive landscape, it must have a clear understanding of market knowledge, cost control and equipment capability, along with the successful implementation of automation solutions. A natural benefit of eliminating the human touch to food and beverage products during the manufacturing and packaging process is the higher assurance of accuracy, consistency and lack of damage. Whether it is through incremental upgrades or ground-up automation, production facilities are yielding improved manufacturing flexibility, performance and reliability in the most cost-effective way.
Domestically, there are over 20,000 food and beverage companies generating $700 billion dollars in annual revenue. Much is at stake financially, as well as competitively. Those companies that respond quickly and effectively to regulation reform and market influences, via plant automation, stand to profit in more ways than one. Manufacturers that overlook the relevance of industry-leading innovations and wait to implement them into daily operations risk the chance of slowing operations and losing customers.
Jack Uhl is Sales Manager, Consumer Products Group, for Yaskawa America, Inc.’s Motoman Robotics Division.