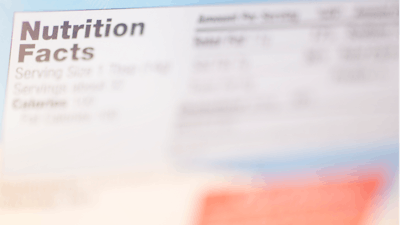
As food and beverage suppliers and producers look to help retailers keep pace with the demands of a sequestered populous, the U.S. Food and Drug Administration has responded by relaxing labeling restrictions to help get products to market more quickly. However, these actions raise questions about whether avoiding potential bottlenecks is simultaneously sacrificing consumer safety, and the inherent benefits of proper labeling strategies.
To help offer some perspective on the topic, and to offer some guidance relating to ongoing labeling strategies, we recently sat down with Ken Moir, vice president of marketing a NiceLabel.
Jeff Reinke, editorial director: What is the most common cause of labeling errors?
Ken Moir, NiceLabel: There are many causes for labeling errors, but one of the most common reasons is the use of legacy label design and print solutions that are either out of date or disparate across an organization or supply chain. This offers little central oversight or control.
Often, these legacy solutions rely on manual data entry, paper-based record keeping and QA practices, or physically transferring data via a USB drive or other removable media on the factory floor. An assemblage of unharmonious processes also leads to a lack of visibility into the labeling process, as there is no central repository to track changes and system events. These issues quickly lead to errors, duplicated efforts and lost time.
Every product category is unique. Compliance for certain products may be a challenge as regulation is constantly shifting, and companies may need to localize labels to meet regional requirements.
JR: The expense and embarrassment of a product recall is probably the most prominent ramification of a mislabeled product, but what are some of the other "costs" of inaccurate labels?
KM: Of course, a product recall can be devastating for a brand’s image and reputation, but problems from inaccurate labeling can be much more severe. While a brand may incur significant losses following a recall, a consumer with allergies may be less fortunate. In this case, a mislabeled product could result in anything from mild irritation to a life-threatening reaction. Labeling practices must go beyond meeting compliance or avoiding expenses - consumer safety must always come first.
JR: In addition to the legal requirements, labels can do a lot to help sell the product. What do you feel food manufacturers should currently be working to include on their labels?
KM: With constantly changing regulations, it’s important for food and beverage manufacturers to be agile in their labeling, so they can quickly adapt without delaying shipments.
Take for example the FDA’s recent changes to the Nutrition Facts panel. Food companies needed to update existing label templates to incorporate new nutritional information without causing delays. Agility and the ability to quickly respond to changing market conditions will serve companies well outside of the regulatory landscape. Aligning labeling with marketing to appeal to customers can help boost sales.
JR: In light of the pandemic, some labeling requirements have been eased in an effort to help reduce costs and get products to market faster. Do you see any of these measures staying in place long-term?
KM: While it’s hard to predict the future, it’s probably safe to say that we won’t return to business as usual anytime soon. The pandemic has forced flexibility in supply chain practices. Those that prove to drive efficiency and help food manufacturers better compete will likely be maintained as we emerge from the pandemic.
JR: How do you feel these steps have helped or harmed the food processing sector?
KM: The temporary policy of relaxing certain food requirements has certainly helped food manufacturers, retailers and restaurants to prevent bottlenecks in the supply chain and meet consumers’ food needs during the crisis. It’s hard to estimate if any harm has been made with temporarily less stringent nutrition labeling rules, however, proper nutrition facts labels are the best way to protect customer health in terms of food safety.
JR: What investments in labeling equipment, software or design do you think will be most important for food manufacturers to make in the near future?
KM: Many companies today are digitally transforming their labeling processes, which can provide a range of unique and pertinent benefits across entire operations. The goal is to implement a standardized and controlled method for producing labels or marking packaging throughout the entire organization.
For example, a modern solution for label management should be able to centralize and automate the entire label design and printing process, so any user can adjust and print labels remotely, ensuring supply keeps moving without interruptions. Similarly, a modern solution should easily integrate with any new or existing business system or printer, regardless of manufacturer.
Businesses are increasingly moving systems and processes to the cloud, and labeling is not an exception, especially in the current COVID-19 climate. Cloud-based labeling systems enable critical data to be made available on demand and accessible from any location. More specifically, cloud-based label management systems allow organizations to adjust and print labels remotely and ensure supply keeps moving through the warehouse without delays.
All of this can reduce time and costs when creating new labels, streamline operations, and significantly improve accuracy and transparency throughout the entire supply chain.
JR: Looking to the future, what do you think will be some of the leading technologies or strategies that will drive food and beverage labeling?
KM: With so many challenges to overcome, there has never been a greater need to adopt the most efficient processes to ensure labels are accurate, available and compliant. And simply put, the benefits of a digitized labeling solution are too great to ignore.
To future-proof supply chains, it is important that labeling falls in line with greater trends of digitization and modernization. Therefore, label management should integrate with and scale alongside business systems like ERP, MES and WMS. Labeling should also prepare for an increased use of mobile devices and IoT-enabled hardware and provide a central, interoperable platform for handling a range of label and direct marking printers.