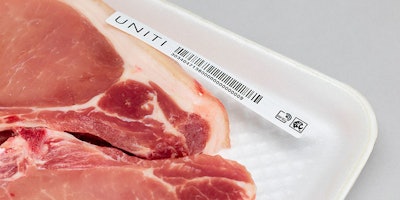
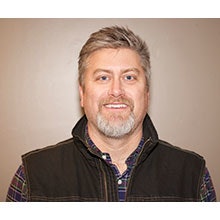
The same technology that’s used by apparel companies for inventory accuracy and visibility, and by airlines to track baggage, could hold the answers for food manufacturers looking to accurately manage inventory, reduce theft and improve use-by date visibility to increase food safety.
Radio-Frequency Identification (RFID) is a proven technology that uses radio-frequency waves to transfer data between a tag/label with an embedded chip, or integrated circuit, and a reader to identify, track and trace an item. Unlike barcodes, every tag is unique, and does not require line-of-sight. It is also relatively low-cost when purchased in volume. RFID offers the ability for multiple tags, or a single tag, to be read at a short or near distance, as well as longer ranges depending on the tag design. It can be applied at the pallet level, tray or carton level and/or to individual packaging.
Tracking and Tracing
RFID at the manufacturing level provides a manufacturer with the ability to easily track materials and finished goods that have been palletized for storage by manufacturing date and/or lot number.
Consider, for example, finished goods being moved into refrigeration via a lift truck. An RFID-reader may be affixed to the doorframe of the refrigeration unit, or a “tunnel” may be employed prior to the refrigeration unit, enabling the labels on each item — individual packaging, tray, carton and/or to pallet level — to communicate unique information such as date and assigned storage location, thus confirming “pack or build” information and improving inventory efficiencies.
Why is track and trace so important? The globalization of the food supply chain means more stakeholders. And while that’s a good thing, it also means more chances for confusion or disarray. Date-expired food means waste and lost profits in an industry that already faces razor-thin margins. A 2013 report from the United Nations Food and Agriculture Organization (FAO) estimates that nearly 200 million tons of food produced for human consumption is wasted each year at the distribution level alone (which accounts for everything after processing but prior to consumption). That adds up to waste worth well over $100 billion. As such, early pilots of RFID have typically been in the refrigerated, perishable food arena.
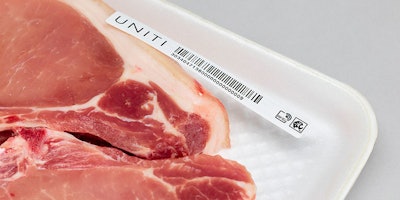
Shining a Light
RFID technology allows users to readily and conveniently focus on items throughout the supply chain, providing a more accurate data picture at each stage. Collaboration and information sharing between partners will help drive efficiencies, as well as provide more control over processes that increase availability and reduce waste. Delivery accuracy to the distributor or via direct drop shipments to retailers can also be enhanced. The data obtained through the use of RFID can increase overall process efficiency — improving inventory accuracy to 99 percent-plus, and reducing waste by up to 20 percent.
Time and resources spent on inventory management can also be decreased through the use of RFID technology at all supply chain levels. That means employees can spend less time tracking inventory and more time focusing on servicing the customer. At the retail level, RFID allows products to be read quickly and accurately at checkout. RFID also provides an added level of lost inventory exposure as retailers can see how many items left the store without being scanned, thus making it more apparent if they have a theft issue.
The Technology
RFID inlays utilize antennas that are specifically designed to work with a chip for end-use applications. The chip or integrated circuit is capable of storing product data and the antenna allows the data to be transmitted to a reader some distance away. The RFID inlay can then be integrated or converted into a tag or label and applied at crate, pallet or item level. RFID technology essentially serves the same purpose as a barcode, and additionally has five distinct advantages:
- It can carry a greater amount of unique information
- It can be read at greater distances
- It’s fast — multiple reads per second may be made
- It doesn’t require line-of-sight to be utilized or scanned
- It can be programmed to be copy proof hence good for authenticity purposes
RFID can provide a clear view of product information and its remaining shelf life. Because it transmits data to the reader, employees no longer need to read individual items, cases or pallets by hand. Tags can be read from six to 10 feet away through either hand held units or fixed readers, and provide an accurate reading of what is on the pallet. In addition, food-friendly tags are capable of providing accurate readings even in different environmental settings.
The Potential
RFID is currently being used at the retail level in select markets in the United Kingdom and has provided enhanced visibility into inventory and shelf life information.
Applied at item level to food manufacturing inventory processes and shipping, RFID can provide an innovative, manageable solution that provides complete visibility across the supply chain.