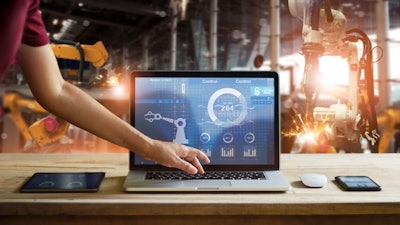
Manufacturers continuously strive to improve their operations, yet outdated tools for process monitoring and quality control are all too common on plant floors. This is largely because when it comes to adopting new digital technology, those in the manufacturing industry face a myriad of unique roadblocks.
For instance, some organizations operate aging equipment from an older era, and they cannot easily incorporate new technology without a significant investment. Of course, the shift to digital has long been on the agenda for many—but as a vision for the distant future, with no solid roadmap for implementation.
But then came COVID-19.
After facing unprecedented challenges brought on by the pandemic, manufacturers have pinpointed where their legacy systems and processes impeded their response to the crisis—and where technology investments in these areas can enable strong growth as the pandemic recedes. So now we’re seeing an accelerated interest among manufacturers in creating digitally-enabled production environments, ready and able to overcome anything that lies ahead. In fact, a recent InfinityQS survey of manufacturers around the globe found that more than half of respondents are prioritizing digital transformation initiatives, with 52 percent exploring or adopting new technologies to enhance performance in the wake of COVID-19.
Building a digital foundation
More specifically, manufacturers are looking for technology solutions that will enable their organizations to:
- Streamline operator efficiency, so productivity won’t be hindered by workforce limitations.
- Solve production problems in real time to produce safe, consistent, high-quality products.
- Keep employees connected and productive, even when working remotely.
- Leverage data to continuously optimize operations, reduce costs and make agile decisions.
Together, these capabilities form the foundation for flexible, agile, and resilient manufacturing. But in order to get started, manufacturers need:
1. Automated Data Collection and Analysis.
In many plants, operators tend to get bogged down with time-consuming tasks, on top of running their production lines. This could include manually recording quality checks, jotting data down on paper forms, and sifting through pages of control charts—all while keeping a constant eye on the clock so they don’t miss their next scheduled task.
This was only magnified during the pandemic, as illnesses and social distancing measures left plants operating with increasingly limited on-site workforces. Operators were stretched thin trying to handle the responsibilities on their own plate, while also taking on additional roles to fill the gaps.
But it’s possible to alleviate the burden on plant-floor teams while making data collection and analysis faster, easier, and far more accurate. Next-generation statistical process control (SPC) software can automatically collect measurement values from a variety of data sources—including gauges and digital devices, flat files, XML files, databases, OPC servers and more—and store them in a centralized repository for analysis.
From there, the software monitors processes in real time, sending instant alerts to necessary personnel when a specification limit or statistical violation occurs. The operator or quality manager can then take immediate action to correct the issue and prevent defects.
2. Workflows.
In traditional manufacturing environments, responses are based on individual operator knowledge and judgment. And through years of first-hand experience, employees often cultivate a wealth of “tribal knowledge" not formally recorded, but locked in the heads of those with all that experience. This could include everything from understanding the personalities of individual machines to knowing the fastest tricks to correct specific issues.
But what happens if those employees are away from the plant floor, out sick, or otherwise unavailable? All that valuable knowledge would be lost, seriously impacting efficiency and productivity. That’s where workflows come in.
These are essentially tribal knowledge converted into prescriptive guides for responding to process and quality issues, captured and predefined in a quality management software solution. They enable operators, quality personnel, supervisors, and other employees to respond consistently and effectively to specific problems, as well as prevent similar events in the future. Even during staffing shortages, they can keep their lines running, shift employees to where they are most needed, and never miss a beat.
3. The Cloud.
Most of us wouldn’t necessarily associate manufacturing with remote work, but during the height of the pandemic many organizations shifted their supervisors and quality teams away from the plant floor in an effort to enable social distancing and keep employees safe. Unfortunately, those that still relied on paper checklists or even on-premises systems for quality management found that they couldn’t access plant-floor data while working offsite.
Cloud-based, Software-as-a-Service (SaaS) quality systems can standardize and aggregate real-time data from all products, lines, and even multiple production sites in a secure, centralized repository. The system can be accessed and operated from anywhere, at any time, empowering remote and on-site users with the same information and insights.
4. Data Visualization.
The very same data used to detect issues can also be used to improve every aspect of production across processes, lines and facilities. But uncovering these insights requires having all the data in a standardized format, and stored in a unified repository — like the kind offered by cloud-based SaaS solutions mentioned above.
Cloud-based quality systems can translate data from all sources into a common “language,” and from there, data can be aggregated, rolled up, and sliced and diced in many useful ways. It’s here that data visualization tools can be extremely useful. Modern quality management software offers innovative tools for summarizing and visualizing the sheer volume of data generated across an enterprise. Manufacturers can thereby gain faster insights into concerning trends, best practices, and opportunities for improvement.
The long history of manufacturing is filled with periods of disruption and innovation. Now we’re in the midst of the latest massive shift, and it’s time for manufacturers large and small to make the investments necessary to thrive in the future. Ultimately, investments in digital transformation should come down to putting real-time data and insights into the hands of those who can leverage them for effective decision making. Organizations that do so will be able to solve (and even prevent) problems, reduce costs, best utilize resources, optimize operations, and keep producing top-quality products—even during times of crisis.