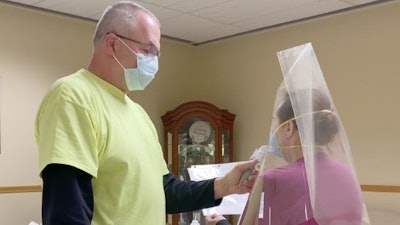
When COVID-19 hit, Massachusetts-based FLEXcon, a provider of films and adhesive labels, realized it might be well-positioned to pivot operations to create PPE products for healthcare and other frontline workers. In a matter of weeks the company had shifted much of its operations to create face shields and test hoods. The first batch of face shields was donated to a number of Massachusetts hospitals.
The company then began producing single-use test hoods, which are plastic head and face coverings that can be used to test the effectiveness of masks. Unlike reusable test hoods, these fully recyclable options could be purchased independent of mask kits, allowing workers to minimize contamination and ensure their masks are tight against their face.
The company's initial response and current actions offer a number of positive takeaways related to supply chain management, operational flexibility, and growing a strong and reliable workforce. I recently sat down with Lavon R. Winkler, the CEO of FLEXcon North America to discuss the company's COVID journey.
Jeff Reinke, editorial director: What were the timelines for both recognizing the initial need, and ability to produce the face shields, to actually beginning production of them?
Lavon R. Winkler, CEO, FLEXcon North America: In March, we received multiple calls from our local EMS and two local hospitals asking if we might be able to provide any sort of PPE. Along with making donations of materials we had on-hand, we brought the idea to our team for consideration. Our innovative team was eager to help.
We developed a prototype face shield and delivered the first 2,000 to one of the hospitals for sampling within 36 hours. To date we have donated to over 350 organizations, and we continue to manufacture and sell face shields at just above our cost. Our reach has extended past our local community and we are now distributing across the country.
At the end of April, we received another call from a local hospital. They had received a shipment of N95 face masks and needed to fit employees with them. Fit Testing is traditionally performed with the use of a reusable test hood. However, one physician was uncomfortable participating in testing which involved using a hood that had been worn by others, albeit sanitized between participants.
The hospital reached out to FLEXcon to ask if we might be able to develop a single-use test hood to be used for mask fit testing. Our team assembled, and within 24 hours were able to create a prototype to bring to the hospital for testing. Thereafter, we worked with hospital representatives to tweak the design to their specifications.
Finally, production and product development collaborated to create the standard work and process flow, which took one day, and we immediately ramped up production on our day shift to make the hoods. We are holding what is necessary in inventory and running replenishment orders on a weekly basis.
JR: What have been some of the changes or adjustments associated with this shift to PPE?
LW: Fortunately, we had enough material on-hand to begin production immediately. We’re also very fortunate to have established relationships with vendors that could supply the raw materials we needed, most of which are located in the U.S., which meant that we had a reliable supply chain.
Our relationships proved to be valuable from a purchasing perspective as well. We are in constant contact with our key suppliers and were able to source additional materials moving forward to support the increase in demand of certain components.
We also quickly established an inventorying system within our Spencer, MA facility. We set minimum and maximum levels of finished inventory to ensure we were stocking the product to meet demand.
To streamline the production process, we re-configured an area in one of our manufacturing plants so as to co-locate equipment for expedited production of test hoods and face shields. Our engineering department also crafted special tooling for an adhesive coater to accurately zone-coat where sealing was required on the fit test hoods.
JR: What were some of the things you learned about your people during this process?
LW: A company is its people, and our company is comprised of an incredible team of problem-solvers who are concerned for their community. Through a strong desire to make a difference in a crisis situation, they exemplified effective collaboration, along with a heavy dose of ingenuity, to achieve the goals set out before them in record time. This opportunity to help gave meaning to the risk they were taking every day just by coming to work. Their efforts were nothing less than heroic, and we couldn’t be prouder of their accomplishments during a very difficult time.
JR: Are these PPE offerings something you'll continue to offer into the extended future?
LW: The FDA relaxed its restrictions regarding testing and approval of PPE devices during the pandemic. This allowed FLEXcon the opportunity to step up and respond to the needs of medical professionals and EMS workers. Once the pandemic is in our rearview mirror, it’s likely that the FDA will reinstate those restrictions, at which time we’ll assess whether FLEXcon should continue producing PPE.
JR: What is the state of your core business?
LW: We continue to operate within multiple manufacturing locations with redundant capacity, geographically disbursed. All of our locations are open and operating at full capacity.
Our core business is down slightly, and the mix of products has changed as well. However, there’s been an increase in demand for materials for social distancing graphics on floors. We’re also seeing high demand for labeling materials for medical, food, beverage and personal hygiene products.
JR: Were there any best practices picked up from this experience that can be utilized going forward?
LW: Cross-functional collaboration has been the key to success regarding the PPE we’re producing - from rapid prototyping and establishment of inventory systems, to co-location of equipment and development of standard processes - and we will apply these practices moving forward as new challenges present themselves.
More information about FLEXcon and its offerings is available at www.flexcon.com.