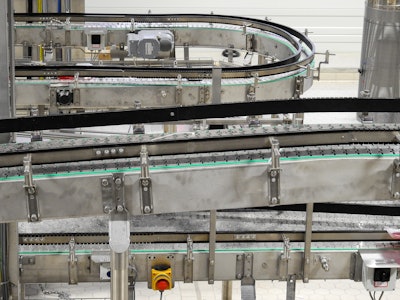
Introducing modern motors in food and beverage businesses can help them achieve up to 50 percent energy savings, considerably reducing running costs in existing applications. However, replacing motors is not always a possibility. Many food and beverage applications are bespoke, meaning that changing a motor could alter the end product as the exact conditions may be hard to replicate. At the same time, industrial motors are generally expected to have a life-span of up to 15 years and as such manufacturers won’t want to replace motors early on in their life-cycle.
Currently, businesses face a unique problem. Modern motors now have smart capabilities that vastly improve their running efficiency. With built-in smart sensor capabilities that allow for manufacturers to extract detailed information, smart motors can now analyze, give accurate health readings, optimize running performance and extend the lifespan of the machinery.
For example, using condition monitoring smart motors can reduce their unplanned downtime by up to 70 percent. These capabilities radically cut the costs of running a motor, freeing up resources to develop other areas of production. In fact, using the data from smart motor sensors can lower operation costs by 30 percent. This shows the jump in value that smart capable motors have compared to traditional motors.
Manufacturers, until recently, had to decide between losing return on investment by immediately replacing motors or risk falling behind by continuing to use traditional motors. Luckily, there is now another path. It is now possible to install smart sensors on traditional motors to make them smart capable. Thereby letting manufacturers achieve higher levels of efficiency without the need to prematurely replace motors.
These flexible new smart sensors are simple and easy to install. For example, certain smart sensors come in three small pieces meaning manufacturers don’t have to risk long periods of downtime to install the sensors as they can easily be attached to the outside of the motor.
Smart sensors can measure a variety of outputs, including vibration, speed, motor load and other variables. This means that a lot of information is being generated and must be stored on the device before being uploaded to cloud devices, in case regular uploads are not achievable. At ABB we understand that constant uploads to the cloud are not always feasible, which is why our smart sensors can store up to four weeks of data.
Enabling condition monitoring of motors through smart sensors can allow plant managers to remotely view the overall health of a plant — even from a mobile device. Using these tools means that maintenance and operation decisions can be made without delay, reducing maintenance costs by 15 percent.
A reduction in running costs are not the only benefit that smart sensors can bring to production operations. Design engineers can also benefit from the widespread use of smart sensors. Recording and analyzing the data from motors can aid design processes such as virtual commissioning. Data can be fed into commissioning software allowing for virtual trials of plant designs before the development begins.
Designing plants is a delicate task, especially for the food and beverage industry. Constant production means that the design must be compact and efficient, but at the same time, every part must be easily accessible to allow for maintenance to be carried out. In-depth information means that designers can make better design choices faster. In fact, data analysis of smart sensor data can lower commissioning time by up to 50 percent.
Enabling smart capabilities in motors is a sure method of increasing value in production systems. Especially food and beverage, this is because the increase in monitoring will allow businesses to more accurately understand the health of the machine. This deeper understanding is seen not only through less downtime, but also through longer asset life-spans which can be extended by up to three years.
Smart motors may be in a league of their own compared to traditional motors, however, this does not mean that traditional motors cannot keep up with a little help. Retrofitting motors with smart sensors is a simple and effective method to extract extra value from traditional motors without the need for wholesale replacements.