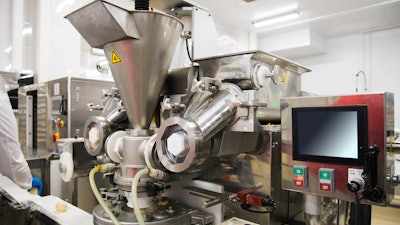
Food manufacturers must ensure that foreign materials are not present in products that reach the consumer. Metal detectors are commonly used for food safety inspection, but the use of metal in food packaging can affect their sensitivity and ability to identify metal contaminants. X-ray systems offer many benefits over traditional metal detectors, as they are not impeded by metal packaging, can identify non-metal fragments – such as glass and bone – and, in some cases, are more sensitive. This article highlights 10 reasons to complement existing QC protocols with X-ray inspection systems.
1. ‘See through’ metalized film or foil packages
Metallized film, foil and induction sealed packaging create large ‘product effects’ for metal detectors, which requires these devices to operate with degraded sensitivity. In contrast, X-ray systems can see through these thin packaging materials to detect very small contaminants. X-ray can also avoid false contaminant detection due to small amounts of metal embedded in recycled paperboard, whereas a metal detector would reject the package, potentially affecting profitability.
2. Detect many types of metal and other foreign objects
In X-ray imaging, darkness represents density. Automatic image analysis uses this characteristic to identify contaminants that are dense, have sharp edges, or are a particular shape or size – such as glass fragments, stones, and pieces of plastic and bone. Unlike metal detectors, there is no trade-off in detection capability based on metal type, as most metals – ferrous, non-ferrous and stainless steel – have similar densities and react in the same way. Even aluminum is usually detectable, as are very small diameter wires just a few millimeters in length. Advanced image generation and detection software mean that X-ray systems are also often more sensitive than a metal detector.
3. Setup and test in minutes
Metal detector setup often requires specialized knowledge to understand and adjust parameters to accommodate variable product effects or environment ‘noise’. In contrast , state-of-the-art X-ray systems employ setup wizards that simply require the user to input the package size and line rate, and the device chooses the appropriate settings. The resulting product images deliver immediate and easy to understand feedback, helping to optimize detection. Images of contaminated products – tagged with the product name, date, time and reason for rejection – can also be saved and exported for off-line review.
4. Unaffected by product effects
Unlike metal detectors, X-ray systems are not affected by products that are wet, salty or conductive, or by their temperature. Avoiding these sources of error removes the need to constantly track and adjust for product effects, or to reduce the sensitivity settings. Users can view images of rejected products and make adjustments on the fly. Some systems can even adjust, evaluate and change detection levels automatically, while inspection continues in the background.
5. Installation in hours
X-ray systems can be supplied as a complete package – including inspection, material handling and rejection – allowing them to be unpacked, powered up and installed in just a few hours. In many cases, their small size makes fitting them into a production line easy, and they can be customized for individual factory needs or placed on casters to simplify cleaning and line configuration.
6. Detailed production statistics and image storage
Production environments require detailed record keeping, which can be daunting with metal detectors. Users may be locked into a vendor’s proprietary networking solution, some protocols may require custom programming and setup, and manual, paper-based systems are less than ideal. In contrast, advanced X-ray devices can store complete production statistics – including operators, changes made, system errors or alarms – for many months, offering easy viewing and transfer to a PC or network. Unlike metal detectors, rejected product images can also be saved for root cause analysis and recordkeeping.
7. As safe as metal detectors
X-ray systems must meet exacting standards set by organizations such as the U.S. Food and Drug Administration (FDA) before they can be brought to market, ensuring that they do not present a health hazard when in use. X-rays are generated electrically, so there are no radioactive sources to manage and dispose of, nor is there any long-lasting impact on the food products being inspected.
8. Attractive total cost of ownership
Today’s entry-level X-ray systems are comparable in price to a metal detector on a high quality conveyor, with some devices able to run for 10,000 hours or more without major servicing. Extended warranties and service contracts – including preventative maintenance, priority response and safety certifications – are also available for cost-effective operation. With remanufactured sources and detectors often available at significantly reduced costs, the total cost of X-ray ownership has never been more attractive.
9. Detect more for less
X-ray images can capture more than just contaminants. For example, they can be used to highlight – and reject – underfilled bags and missing or misshapen products. Vision algorithms are available that use the total density of the image to estimate weight and identify gross content errors, as well as to measure objects or look for product variations.
10. Environmental interference is not a problem
The working environment can cause installation and operational issues with metal detectors, resulting in a previously stable device delivering spurious false rejections. X-ray inspection devices are based on a totally different technique, and can operate reliably for weeks, unaffected by external influences such as vibration, electromagnetic fields and power variations. They can be used at temperatures ranging from near freezing to extremely hot, are usually IP65 rated to allow washdown in production settings, and can even be designed to survive caustic sanitation chemicals and high pressure spray cleaning.
Conclusion
X-ray inspection has never been more attractive than it is today. There are many compelling reasons to make the switch to X-ray devices, so speak to an established supplier with expertise in the field, to see how X-ray contaminant detection and product verification can help to improve food safety and quality while protecting your brand.
Read the white paper, "Ten Reasons to Step Up from Metal Detection to X-ray Inspection to learn more. https://assets.thermofisher.com/TFS-Assets/CAD/Reference-Materials/White-Paper-Step-Up-to-Xray-WEB.pdf."
Kimberly Durkot is a field marketing manager at Thermo Fisher Scientific.