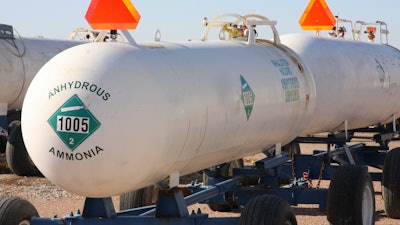
Ammonia is widely used for refrigeration and flash freezing throughout the food and beverage industry. Ammonia provides exceptional cooling properties at an affordable price.
However, ammonia is also toxic. So, if it is mishandled or leaks out of equipment, it can pose a significant risk to human health, the environment, and overall business operations. Therefore, to protect employees and prevent hazardous incidents, it is critical that food and beverage organizations implement effective preventive measures to minimize ammonia risks.
In this article, we’ll explore the risks and dangers of ammonia leaks in the food and beverage industry, as well as discuss best practices for preventing incidents. Additionally, we’ll discuss how an effective predictive maintenance strategy paired with a robust computerized maintenance management system (CMMS) can play a critical role in helping your organization mitigate potential ammonia risks before they become true hazards – or worse. Today’s wireless vibration sensors can integrate with user-friendly data analysis and work order software, automating condition monitoring as well as connecting it to action.
Understanding the Risks and Dangers of Ammonia
Ammonia, specifically anhydrous ammonia, or NH3, is a colorless compound with a strong, pungent odor. It is commonly used in the food and beverage industry for refrigeration purposes due to its excellent cooling properties, energy efficiency, and low cost. However, despite its prevalence, ammonia is still dangerous, so mishandling or failing to adequately maintain ammonia systems can result in serious consequences.
Ammonia is a highly toxic compound and has a corrosive effect on the human body. Direct exposure to ammonia can cause respiratory distress, burns to people’s eyes, skin, and lungs, and even death at high enough concentrations. The Immediate Dangerous to Life or Health (IDLH) concentration for anhydrous ammonia is just 300 parts per million (ppm). Moreover, ammonia leaks can have detrimental effects on the environment, such as contaminating water sources and harming wildlife.
From a business perspective, ammonia leaks can result in costly shutdowns, product losses, legal liabilities, and damage to a company's reputation. For example, about a decade ago, workers at a large chicken refrigeration plant experienced a massive leak that resulted in a wave of tens of thousands of pounds of anhydrous ammonia washing over them. The leak injured more than 100 employees, contaminated countless chicken tenders, and ultimately led to an EPA investigation that culminated in a multi-million-dollar civil penalty.
Ammonia leaks occur for a wide variety of reasons. But according to the EPA, the most common causes of ammonia leaks are plant upsets, maintenance errors, piping failures, collisions, hose failures, and hydraulic shocks.
Tips for Preventing Ammonia Leaks
To mitigate the risks associated with ammonia and prevent dangerous leaks, food and beverage organizations must adopt comprehensive preventive measures and best practices. These include establishing standard operating procedures, defending tank, piping, valves, and seals, and deploying sensors to help monitor for leaks.
Below are some additional key considerations that will help your team effectively prevent ammonia leaks:
- Perform Regular Inspections: Conduct routine inspections of ammonia storage and refrigeration systems to identify potential leaks, corrosion, or faulty components. Utilize specialized equipment, such as vibration detectors to enhance the typical OEM leak detection capabilities, which alert after there’s already a problem. Handheld vibration monitors are most commonly used, but wireless vibration sensors also now exist that can be integrated with CMMS.
- Conduct Employee Training: Provide regular comprehensive training to employees who work with or near ammonia systems. Educate them on safe handling procedures, emergency response protocols, and the importance of promptly reporting any potential issues.
- Carry Out Proper Maintenance: Implement a proactive maintenance program to ensure equipment reliability and minimize the risk of leaks. Regularly check and maintain seals, valves, and piping systems. Implement a preventive maintenance schedule based on manufacturer recommendations and asset performance data.
- Establish Ventilation and Containment: Ensure proper ventilation systems are in place to minimize the accumulation of ammonia vapors. In the event of a leak, employ effective containment measures to prevent the spread of ammonia to other areas.
- Adopt Leak Detection Systems: Install leak detection systems and utilize tools like precision acoustic imagers to monitor for leaks in vulnerable equipment. These systems provide early warnings, enabling swift action that can prevent a situation from escalating.
Preventing Ammonia Leaks with Predictive Maintenance and CMMS
While the above steps are the typical baseline, maintenance teams are also starting to move beyond that to reduce risks. Predictive maintenance involves monitoring and analyzing historical and real-time data from equipment sensors to predict potential failures or maintenance needs. By adopting predictive maintenance techniques, organizations can identify and address ammonia-related issues before they snowball into major problems or leaks. This proactive approach ultimately minimizes downtime, reduces maintenance costs, and enhances overall safety.
Predictive maintenance, especially when powered by growing technologies like data analysis software, offers significant benefits in managing the inherent risks associated with ammonia refrigeration. By continuously monitoring asset performance and analyzing data, maintenance teams can detect and address potential issues before they become serious problems.
A CMMS software can also dramatically enhance an organization’s predictive maintenance strategy by providing a centralized platform for managing maintenance activities, automating workflows, facilitating effective preventive measures, and making data-driven decisions.
Here are just some of the ways that predictive maintenance and a capable CMMS can contribute to a successful ammonia risk mitigation strategy.
- Early Detection: Predictive maintenance and CMMS leverage IoT sensors and utilize data analytics to identify abnormal patterns or anomalies in refrigeration systems. By quickly detecting early warning signs, such as abnormal vibrations, temperature fluctuations, or unusual pressure levels, maintenance teams can take timely action to prevent dangerous leaks.
- Condition-based Maintenance: With condition-based maintenance, maintenance activities can be scheduled based on actual equipment conditions rather than arbitrary time-based intervals. This approach optimizes maintenance efforts, reduces downtime, and minimizes the risk of failures that could lead to ammonia leaks.
- Task Management and Compliance: A CMMS streamlines maintenance workflows by assigning tasks, tracking progress, and ensuring compliance with industry regulations. Regular inspections, maintenance tasks, and safety checks can be scheduled, documented, and tracked systematically, reducing the likelihood of oversights, or missed maintenance activities.
- Asset Tracking and Maintenance Scheduling: A CMMS enables organizations to track their ammonia-related assets, including refrigeration units, pipes, and valves. It allows for the scheduling of regular maintenance tasks and ensures that equipment is inspected and serviced at appropriate intervals, minimizing the risk of failures or leaks.
- Comprehensive and Accurate Documentation: A CMMS assists in documenting maintenance activities, ensuring compliance with the strict safety regulations and standards in the food and beverage industry. It enables organizations to generate reports and maintain comprehensive records of maintenance tasks performed on ammonia systems, which is especially useful come audit time.
- Real-Time Monitoring and Alerts: A CMMS can integrate with a wide range of sensors and monitoring devices to provide real-time data on the condition of ammonia systems. It can generate automated alerts when anomalies or potential issues are detected, enabling maintenance teams to take immediate action.
- Data-Driven Decision Making: Predictive maintenance and CMMS solutions generate valuable insights, helping leadership analyze historical data, maintenance records, and real-time information. This data-driven approach results in detecting the early signs of deterioration or potential failures, allowing for timely preventive measures.
Ammonia risks in the food and beverage industry need to be taken very seriously to ensure the safety of employees, prevent equipment damage, and protect the environment. But by implementing best practices for prevention, such as regular inspections, employee training, adequate ventilation, and proper maintenance, organizations can significantly reduce the chances of ammonia leaks.
Moreover, integrating predictive maintenance techniques with capable CMMS software provides you with all you need to take a proactive approach to mitigating ammonia risks. Embracing these technology-driven strategies will enable your food and beverage organization to ensure the safety of workers, protect the environment, and safeguard the reputation and profitability of your operation.
Candice Potter is an enterprise account executive and Erin Sidwell is a key account manager for food & beverage at eMaint.com.