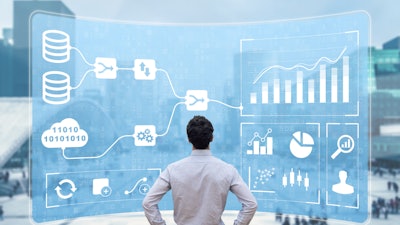
Digital transformation requires rigorous and targeted oversight to achieve strategic goals while measuring the return on investment. Yet, manufacturers select metrics that often provide little insight, measuring technology uptake rather than the transformation's results. Digitalization requires a careful selection of key performance indicators (KPIs) for strategic intent and the achievement of business goals.
KPI Alignment and Focus
In devising KPIs, it's important to distinguish between business improvement and the rate of technology rollout. After identifying improvements, you need to choose the business categories from which you’ll gather relevant metrics. Some will be externally focused, measuring digitalization's effect on customers, stakeholders, value creation or sustainability. Others will measure internal impacts, covering operational effectiveness or efficiency, employee engagement, or workforce productivity.
There are many generic measurements of business health, success and efficiency. The following six are common to most manufacturers. To better illustrate KPIs, we’re going to use the example of a fictitious carton manufacturing business.
1. Manufacturing availability is the ratio of machine uptime to machine downtime. Equipment availability is key to meeting client volumes and deadlines without incurring penalty costs from extra shifts and emergency maintenance interventions.
As a carton manufacturer, increased manufacturing capacity is one of the desired outcomes of digital transformation. This will involve using sensors on critical equipment to forecast equipment degradation and predictive maintenance techniques for better maintenance intervention planning - hopefully reducing breakdowns. Measuring improvements in process availability will provide empirical evidence of one aspect of digitalization's impact by being linked to a stated, strategic goal.
2. First-pass yield is a measure of plant effectiveness that tells a manufacturer the number of products that meet quality and compliance benchmarks without requiring rework. Reduced rework or scrap reduces waste and operational costs, increasing operating margins.
Cardboard strength can be damaged during the manufacturing process due to excessive pressure from the paper rollers during die-cutting. Digitalization lets you monitor and minimize roller pressure while ensuring the die-cut color block doesn't move. With die-cutting contributing significantly to high rework ratios, measuring first-pass yield helps you keep rework to a minimum.
3. Revenue generated per employee measures business efficiency and productivity. If one of the stated goals of implementing digitalization is to increase efficiency, revenue per employee is a useful metric to monitor. While the ratio may decrease due to learning curve impacts in the early days of digital transformation, the medium and long-term trends should improve from historical results.
4. Customer satisfaction. In the example of the carton manufacturing business, customers expect competitive pricing, high-quality manufacturing, and just-in-time delivery. Having benchmarked customer satisfaction metrics for two years before the digital transformation, the manufacturing business is well-placed to understand the impact of its digital initiatives on clients.
5. Your customer churn rate is the percentage of customers who cease to do business with you when measured over a defined time. They may cancel subscriptions, future work, or fail to make a repeat purchase within a nominated period. Customer churn is expensive, and attracting new customers costs considerably more than retaining existing clients. Customer churn will inevitably reduce if your digital transformation is successful and you pass on some of your gains to stakeholders. If you're seeing great internal returns from digitalization, but customer churn is static or increasing, you have tactical decisions to make to ensure your investment is not in vain.
6. The rate of innovation can be described as the pace at which a company introduces new products, processes or strategies. It is a metric that assess adaptability and forward momentum of your organization. Management guru Peter F. Drucker categorizes innovation into three main types: product, social, and managerial.
Digital transformation in the context of manufacturing is more than just the adoption of advanced technologies. It embodies the very spirit of innovation by introducing new ways of working, empowering workers, refining workplace culture, and flattening hierarchical structures. These changes, especially when driven by digital tools and processes, align directly with Drucker's concept of product and managerial innovation.
Through digital transformation, manufacturers are not only equipped to produce novel product choices, but also redefine the management structures supporting them. Identify the specific innovations you wish to see in your manufacturing business — be it improved customer experience, cutting-edge product developments, or precise tracking of actual versus expected breakeven time on products — and measure for that.
Measuring the success of digital transformation requires capturing meaningful data. It doesn’t hurt knowing how long digital transformation actually took, how well you stuck to the budget, or how many new tasks were completed with the new tools. But those are, in a way, vanity metrics. Those can all be positive, but not result in any meaningful improvement on an operational level.
Instead, focus on measuring the impact of the digital change on the business improvements you originally identified as strategic project goals. These figures support tactical decision-making for continuous improvement while evidencing the consequential return on your digital investment to stakeholders.
For over 30 years, Eric Whitley has been a leader in the Manufacturing space. In addition to the many articles Eric has written, you may know him from his efforts leading the Total Productive Maintenance effort at Autoliv ASP or from his involvement in the Management Certification programs at The Ohio State University. Eric is now with L2L, where he currently serves as the Director of Smart Manufacturing.