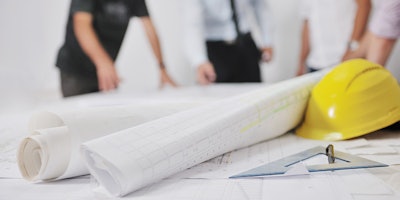
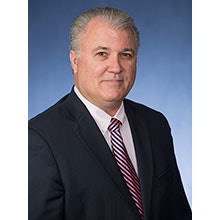
Technology and ever-increasing consumer demand are driving food and beverage companies to compete at a different level than ever before. Speed to market is increasingly important to doing business — the faster a new plant can be built or renovated, the sooner it can begin producing a return on investment.
So how can you ensure your next construction project stays on track? Let’s look at five ways to set yourself up for success, whether you’re tackling a greenfield project or a retrofit.
Define A Clear Project Scope
This may sound obvious, but it’s crucial to establish what this new facility is trying to achieve during the scope definition phase. This includes:
- Working closely with project stakeholders to define goals and expectations
- Identifying the original equipment manufacturers (OEMs) you’ll be working with
- Defining throughput and production expectations that align with budget and infrastructure
That being said, one of the major challenges in this industry is that it’s dynamic and driven by ever-changing consumer preferences. You may have certain expectations for a facility that ultimately change depending on your company’s needs. You may need to add new lines, capabilities or products.
While it’s impossible to plan for everything given the fast-paced food and beverage industry, consider building flexibility into your plant to accommodate potential changes in the future.
Factor Equipment Installation Into The Budget
Of course, the cost of your equipment is usually top of mind when determining budget, but the equipment itself isn’t all you need to think about.
Communicate with your OEMs and get a clear understanding of what the infrastructure needs are for your equipment early in the process. This will help you plan for the cost of actually installing the equipment once it arrives on site: It may be a simple plug-and-play situation or you may need major retrofits to accommodate the equipment.
Either way, equipment installation must be accounted for when determining the project budget, or else you may encounter an unpleasant surprise down the road.
Understand Infrastructure Capabilities
When it comes to food and beverage processing, you can only go as far as your utilities will allow. It’s important to get a grip on the infrastructure capabilities of your plant and what you will need to support your production.
Plan what your electrical, water and gas needs will be so that your facility is designed and built to match them. Taking the time to understand utility expectations before construction crews begin work is time well spent.
Factor Equipment Priorities Into Scheduling
In the food and beverage market, a lot of processing equipment has a long lead time, which means you may need to make some equipment decisions sooner than you realized.
A client recently delayed making an equipment purchase until the project was a year away from completion. That may seem like plenty of time, but some equipment requires a 9-month lead time, not to mention the time needed for testing and training employees. You can see how procrastinating on certain equipment decisions can end up pushing your entire project timeline back if you’re not careful.
My advice: Work backwards from the day your equipment needs to be running at 100% and build your schedule around that — and always build in buffer time to help cushion any unforeseen delays or internal roadblocks.
Set Realistic Expectations For Commissioning Times
As you know, the work isn’t done just because you have walls, flooring, a roof and utilities in a building. Preparing your facility to operate at full-speed requires activities such as:
- Installing, calibrating and testing new equipment
- Ensuring the equipment meets protocols
- Training employees on the equipment
Be realistic about how long these things will take.
If your project is a retrofit in an already operating facility, have the participation of your full plant team who will be affected by the project. Don’t make the mistake of planning as if the project is in a vacuum.
Construction may affect other parts of the facility, which if unplanned, can spell downtime and delays, if not disaster. For example, you may need part of the plant to go offline in order to install new equipment. Think several steps ahead and always communicate with your plant team to ensure everyone is on the same page.
Todd Allsup is VP, Food & Beverage Facility Services at Stellar.
About Stellar
Stellar is a fully integrated firm focused on planning, design, pre-construction, construction, refrigeration, mechanical & utility, building envelope, and total operations & maintenance services worldwide. Visit the company's blog at www.stellarfoodforthought.net or learn about its projects at stellar.net.