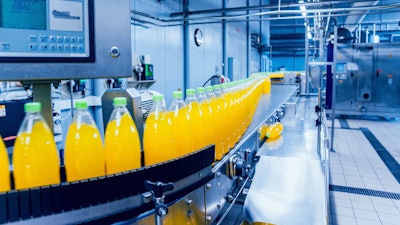
The food and beverage manufacturing industry has evolved dramatically in recent years. Faced with persistent supply chain challenges, many manufacturers have decided to adopt a range of advanced automation technologies, including artificial intelligence (AI), robotics and digital twins.
According to a recent McKinsey & Company report, the food and beverage sector's investment in automation is still less robust than industries such as retail and consumer goods and logistics and fulfillment. When companies do embrace automation, however, they are finding benefits like better performance, enhanced efficiency and improved safety with the convergence of information technology (IT) and operational technology (OT).
At the International Society of Automation (ISA), we see three key automation trends that could deliver an outsized effect on the food and beverage manufacturing industry in 2025: digital deglobalization, supply chain security and a renewed focus on people. All have positive implications for the workforce.
Digital Deglobalization
Many manufacturers are turning to more resilient supply chain practices as they face economic, political and other headwinds. Businesses seeking to guard against uncertainty are choosing to re-shore manufacturing and shift their attention to diversification and growth on their home turf.
In food manufacturing, adopting flexible manufacturing principles can help businesses respond with agility to shifting conditions, such as fluctuating production demands, availability of raw materials and ongoing labor shortages. This can set them up for greater resilience when the next crisis arises.
Automation professionals working with the latest automation technologies and techniques can support manufacturers in their digital deglobalization efforts. AI-driven predictive maintenance can help reduce unplanned downtime, for example, and digital twins can help model production scenarios to maximize efficiency and quality.
Supply Chain Security
Supply chain disruptions have become commonplace recently, and in fact, they have influenced the current move toward deglobalization. Securing supply chain infrastructure will become more important this year as cyberattacks on operational technology grow more sophisticated.
Every industry is seeing elevated cyber risk, and food manufacturing is not exempt. For example, a major beef supplier experienced a ransomware attack on its IT systems in 2021. This incident disrupted production in at least six processing facilities in the U.S.
Cyberattacks have the potential to damage valuable equipment or create food safety concerns. They can also cause chaos in the supply chain — and the supply chain itself can become a target. Without proper protections in place, threat actors can gain access to vendor infrastructure and make their way into industrial control systems.
Ensuring cybersecurity measures are implemented across the entire supply chain will be key in 2025. Food manufacturers can look into established conformance programs and OT cybersecurity standards like the ISA/IEC 62443 series to help safeguard their systems.
Renewed Focus on People
Automation is not magic. It depends on people to realize its greatest potential.
There is a strong demand for skilled and knowledgeable automation professionals. The Manufacturing Institute found that 65 percent of manufacturers in a survey named the attraction and retention of top talent as their top business challenge. And the World Economic Forum projected that, by this year, automation technologies — including AI and robotics — will have created at least 12 million more jobs than they displaced. I expect this trend to continue as advancing technology and automation creates new possibilities across industries — and for society as a whole. As the food and beverage industry incorporates more automation, it will need people with many different skills who understand when and how to integrate technologies into new or legacy systems.
Food manufacturers must prioritize equipping their broad workforce with the skills to meet the growing demand for engineers and technicians. Recruiting, retaining and training qualified staff is critical in 2025, and will only become more so as technology gets more complex.
Claire Fallon is CEO and executive director of the International Society of Automation (ISA), a non-profit professional organization founded in 1945 to create a better world through automation. ISA develops widely used global standards and conformity assessment programs; certifies professionals; provides education and training; publishes books and technical articles; hosts conferences and exhibits; and provides networking and career development programs for its members and customers around the world.